Understanding Factory Defect Shoes: A Complete Tutorial on Quality Control
Learn about factory defect shoes, quality control issues, and buying considerations.
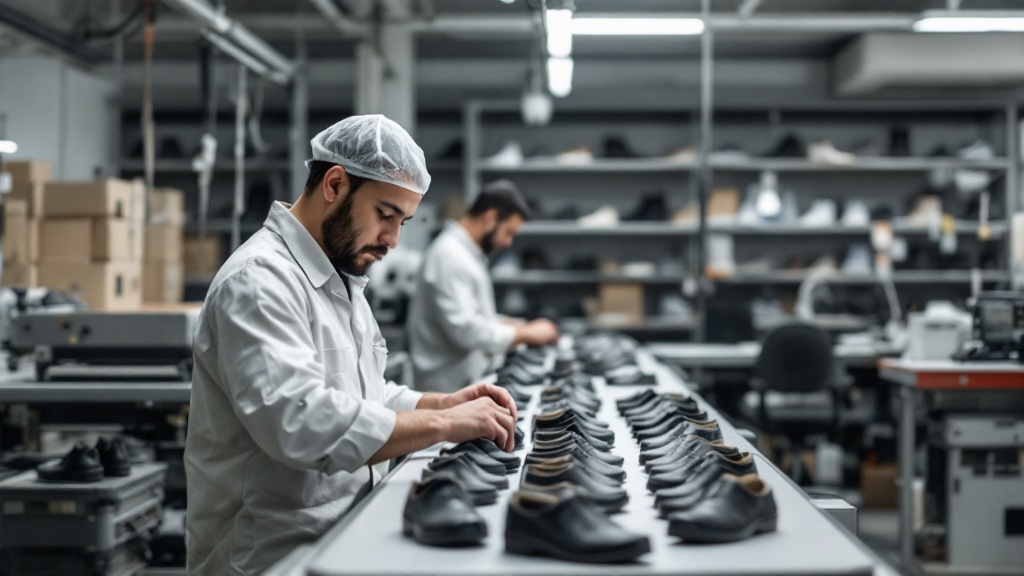
Key Highlights:
- Factory defect shoes are products that do not meet manufacturer standards due to flaws in materials, assembly, or aesthetics.
- These shoes are often sold as 'factory seconds' at discounted prices, impacting consumer perception and trust.
- Quality assurance measures, like those from OpsNinja, help reduce negative feedback and improve customer experiences.
- The fashion industry contributes to 10% of global carbon emissions, with factory defects exacerbating waste issues.
- Defects in shoes are classified into critical, major, and minor categories, affecting safety, functionality, and aesthetics.
- Common quality control issues include misaligned stitching, uneven color distribution, and improper sizing.
- Best practices for manufacturers include comprehensive staff training, advanced technology use, and transparent communication.
- Consumers can benefit from purchasing factory defect shoes due to reduced prices but should be aware of potential durability and comfort issues.
- Understanding return policies and inspecting for visible defects are essential for consumers when buying factory defect shoes.
Introduction
In the complex world of footwear manufacturing, factory defect shoes represent a significant yet often misunderstood segment. Defined as products that fail to meet the manufacturer's quality standards, these shoes can arise from various issues, including material flaws and assembly errors.
While marketed as 'factory seconds' at discounted prices, understanding their implications is crucial for both consumers and brands alike. The challenges posed by these defects extend beyond individual purchases; they can influence brand perception, sustainability efforts, and consumer trust.
As the fashion industry grapples with its environmental impact, the need for robust quality control measures becomes paramount. By examining the nuances of factory defect shoes, manufacturers can not only enhance product reliability but also foster brand loyalty and protect their reputation in an increasingly competitive market.
What Are Factory Defect Shoes? An Overview
Factory defect shoes are described as footwear that does not comply with the manufacturer's set standards during production. These flaws can arise from different origins, including inferior material standards, assembly mistakes, or aesthetic shortcomings. Typically, such shoes are marketed as 'factory seconds' and sold at a discounted price.
Comprehending the complexities of factory defect shoes is vital, as these factory defect shoes can greatly affect perception and consumer trust. By applying strong assurance measures, as demonstrated by OpsNinja's method, D2C companies can reduce unfavorable feedback and improve customer experiences. For example, Clara Mae Silvestre, COO of Hash Stash, explained how OpsNinja optimized their assurance processes, enabling them to scale operations efficiently.
In a fashion sector accountable for 10% of global carbon emissions, the consequences of these defects reach beyond individual labels; they can influence market dynamics and sustainability initiatives. Notably, 15% of used textiles are shipped overseas, often ending up in landfills, highlighting the broader context of waste within the industry. A recent study revealed that 81% of footwear industry experts identified rising merchandise costs as the most pressing challenge, indicating a need for manufacturers to prioritize control standards to maintain consumer confidence.
Comprehending AQL figures—particular metrics signifying acceptable standards—can assist companies in ensuring product reliability and safeguarding their reputation. By understanding the difference between minor flaws and significant defects, consumers can make informed purchasing choices, while manufacturers can implement improved assurance practices to enhance their reputation and foster brand loyalty. This comprehensive view underscores the multifaceted challenges that could impact the sector’s stability and growth in the near term.
Common Quality Control Issues in Factory Defect Shoes
Producers of footwear frequently face various typical standards issues concerning factory defect shoes that can greatly impact product integrity and customer satisfaction. Among these, misaligned stitching stands out as a critical concern, as it can greatly compromise a shoe's durability. Not only does misalignment weaken the overall structure of factory defect shoes, but it can also lead to premature wear and tear.
Additionally, uneven color distribution affects the aesthetic appeal of the product, potentially deterring customers. Improper sizing issues in factory defect shoes can lead to significant consumer dissatisfaction, resulting in increased returns and lost sales opportunities. Inferior materials further worsen these issues, resulting in a decrease in the standard of factory defect shoes.
To tackle these challenges successfully, manufacturers must establish strong assurance procedures. OpsNinja's comprehensive inspections play a pivotal role in this regard, particularly for D2C companies struggling with sizing errors and high return rates. Their customized assurance solutions not only improve product integrity but also safeguard reputation by reducing defects and tackling negative customer experiences.
As emphasized by entrepreneur Neil Ayton in his case studies, managing diverse suppliers and establishing control processes are essential for successful brand management. Significantly, there are 18 Respiratory Protection items that emphasize the necessity for stringent standards. As demonstrated in the case study titled 'Improvement Measures for Safety Footwear,' several actions can enhance the standard of safety footwear, including:
- Standardizing product identification
- Increasing oversight of raw materials
Furthermore, as noted by industry experts, 'technical audits are conducted as a systematic assessment of capabilities and capacities so that improvements can be plotted out more effectively.' By adopting proactive measures in quality control, including those offered by OpsNinja, manufacturers can significantly reduce the occurrence of factory defect shoes, ultimately enhancing both product quality and consumer trust.
Understanding Defect Classifications: Critical, Major, and Minor
Defects in factory defect shoes are classified into three distinct categories: critical, major, and minor.
-
Critical flaws in factory defect shoes pose significant risks to the shoe's safety or usability, including issues like loose soles or exposed sharp edges. As a Quality Control Expert highlights,
A slanted heel not only ruins the aesthetic of a shoe but poses a serious safety risk.
-
Major issues, while not immediately hazardous, can negatively impact the shoe's functionality or visual appeal; examples include poor stitching or visible color discrepancies.
-
Minor flaws are largely cosmetic and do not impact performance, such as small scuffs or slight color variations.
Understanding these classifications is essential for manufacturers of factory defect shoes, as it enables them to allocate resources effectively during quality control inspections. By leveraging OpsNinja's comprehensive inspection reports, which include detailed photos and videos, D2C owners can safeguard their reputation against negative reviews and customer issues. For instance, a robust sampling plan may dictate inspecting 200 pairs from a batch of 10,000 pairs of shoes, ensuring a cost-effective method to identify defects while upholding high-quality standards.
This organized method not only improves product reliability but also cultivates consumer trust in the company. Implementing real-time assurance allows for immediate feedback and corrective actions, minimizing the prevalence of defective products. Additionally, during pre-shipment inspections, a pull-gauge measures the strength of rivets, ensuring they can withstand normal wear and tear.
OpsNinja's streamlined assurance process is essential for enhancing brand reputation and operational efficiency, ultimately averting returns and unfavorable reviews for D2C businesses. A case study with Hash Stash demonstrates how OpsNinja has allowed them to scale operations by tackling control challenges effectively.
Best Practices for Preventing Common Shoe Defects
To effectively reduce common shoe issues, manufacturers must adopt a range of best practices focused on assurance and continuous enhancement. First and foremost, conducting comprehensive training programs for production staff is crucial. This training guarantees that employees are knowledgeable about standards, greatly minimizing errors.
Any significant flaw discovered frequently leads to batch rejection, highlighting the serious repercussions of lapses in standards. Firms such as Tetra Inspection, which functions in 40 nations, stress the importance of training in improving standards.
OpsNinja's dedicated assurance support team plays a pivotal role in this process, offering services such as:
- Detailed product inspections
- Audits
- Supplier assessments
These services provide exceptional customer support and insights into discrepancies, such as supplier sizing issues highlighted by satisfied clients. As Kari Fineran notes, "I appreciated how the team informed me that the size was different from what my supplier told me, as I really did not know."
This testimonial highlights the effectiveness of OpsNinja's approach to quality management.
Utilizing advanced technology is another key strategy; precision cutting and stitching technology can drastically improve production accuracy. Regular material inspections before use are essential, ensuring that only high-quality inputs are utilized in the manufacturing process. Furthermore, encouraging transparent communication between design and production teams can assist in recognizing potential problems early, stopping flaws from advancing through the production line.
Citing the case study on 'Risk Management and Continuous Improvement,' it is clear that applying adaptive measures and supplier self-QC programs greatly improves the inspection process and minimizes flaws. With OpsNinja's dedication to impartial standards, brands can safeguard their reputation and integrity against manufacturing problems. Finally, cultivating a culture of continuous improvement and encouraging immediate feedback are vital practices.
This approach not only helps in identifying and correcting issues proactively but also aligns with the goal of providing the best value for money. As industry experts state, "Our goal is to provide you with the best value for your money," reiterating the importance of investing in effective training and the latest technology to drastically enhance overall quality control in footwear manufacturing.
Consumer Considerations: Buying Factory Defect Shoes
Acquiring factory defect shoes necessitates thorough assessment of both advantages and risks related to such transactions. On one hand, consumers can enjoy substantial cost savings, often gaining access to premium products at significantly reduced prices. For instance, the planned expenditure by U.S. consumers on back-to-college shoes has shown a consistent trend from 2007 to 2024, indicating a strong market for footwear purchases.
However, it is crucial to be aware of potential downsides, including concerns over durability and comfort, which may arise from sizing inconsistencies. To make well-informed decisions, buyers should meticulously inspect shoes for any visible defects and seek clarity on defect classifications from retailers. This is where OpsNinja's customized excellence assurance solutions come into play, providing tailored inspections that ensure peace of mind for D2C companies by safeguarding against negative reviews and customer dissatisfaction.
Comprehending the return policy is crucial to reduce risks, and investigating the company's reputation and its quality control practices can promote greater confidence in the purchasing process. Moreover, consumer behavior statistics indicate an increasing interest in purchasing factory defect shoes, which reflects a growing trend among budget-conscious shoppers. As Tansy E. Hoskins aptly noted,
No one wants to be deceived and at the moment the major sneaker companies are misleading us all – we cannot continue as usual and there will be no point to all these shoes on a dead planet.
By prioritizing transparency and excellence, consumers can navigate the market for factory defect shoes with greater assurance. Additionally, OpsNinja’s cost-effective inspection strategies and proactive approach to quality assurance are pivotal for D2C owners looking to adapt to evolving consumer preferences, especially as interest in digital fashion assets continues to rise. To learn more about how OpsNinja can protect your brand and enhance your purchasing decisions, contact sales or create a free account today.
Our competitive rates and scalable options ensure that we can meet your specific business needs.
Conclusion
The exploration of factory defect shoes highlights the intricate challenges faced by manufacturers and consumers alike. Understanding the nature of these defects, categorized into critical, major, and minor classifications, is essential for both parties. For manufacturers, implementing robust quality control measures can significantly mitigate risks associated with misaligned stitching, improper sizing, and substandard materials, thereby enhancing product integrity and fostering customer trust. The insights gained from industry experts underscore the importance of proactive quality assurance practices in maintaining brand reputation and operational efficiency.
Consumers, on the other hand, stand to benefit from the cost savings associated with purchasing factory defect shoes, provided they approach these transactions with diligence. By carefully inspecting products and understanding defect classifications, buyers can make informed decisions that balance affordability with quality. The growing trend towards purchasing factory seconds reflects a shift in consumer behavior, driven by a desire for transparency and value in an increasingly competitive market.
In conclusion, the footwear industry must prioritize quality control to navigate the complexities of factory defect shoes effectively. By fostering a culture of continuous improvement and leveraging innovative inspection strategies, manufacturers can not only enhance product reliability but also protect their brand’s reputation. As consumers become more discerning, a commitment to quality and transparency will ultimately strengthen the bond between brands and their customers, paving the way for sustainable growth in the footwear sector.