Understanding Defect Categories: A Comprehensive Tutorial for Professionals
Explore key defect categories to enhance quality management and improve product integrity.
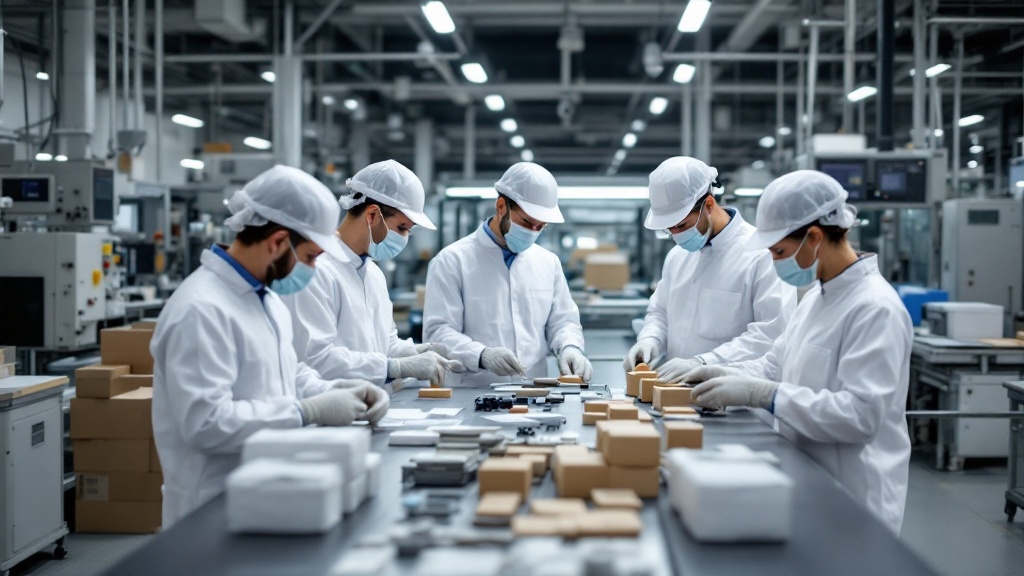
Key Highlights:
- Defect categories help quality management experts identify and address issues in items or materials, including critical, major, and minor flaws.
- Critical issues pose direct safety hazards and can lead to product failure, while major issues significantly deviate from specifications, affecting functionality.
- Minor flaws are aesthetic and do not hinder safety or functionality but can impact customer satisfaction.
- Understanding Acceptable Quality Levels (AQL) is crucial for D2C brands to establish quality standards and manage permissible defect quantities.
- Defects can be classified into design, manufacturing, and labeling categories, each affecting customer satisfaction and brand reputation.
- Design defects arise from inherent flaws, manufacturing defects occur during production, and labeling defects involve inaccuracies that mislead consumers.
- Industries like manufacturing, healthcare, and consumer goods face unique challenges from defects, impacting financial performance and brand trust.
- OpsNinja offers advanced inspection methods, including visual inspections, automated systems, tailored quality checks, and statistical process control to enhance defect management.
- Setting appropriate AQL levels balances customer satisfaction and cost-effectiveness, while ongoing monitoring ensures adaptability to product performance and customer feedback.
Introduction
In the realm of quality management, understanding defect categories is crucial for ensuring product integrity and customer satisfaction. Defects can manifest in various forms, from critical safety hazards to minor cosmetic flaws, each requiring a tailored approach for effective resolution. As industries increasingly recognize the importance of robust quality control measures, professionals must familiarize themselves with the different types of defects—design, manufacturing, and labeling—and the specific challenges they pose.
This article delves into the significance of categorizing defects, the impact they have across diverse sectors, and the methodologies available for detection and classification. By equipping themselves with this knowledge, brands can enhance their quality assurance practices, foster customer trust, and ultimately drive growth in an ever-competitive marketplace.
Introduction to Defect Categories: Understanding the Basics
Defect categories serve as crucial classifications that enable experts in quality management to recognize, evaluate, and tackle various issues encountered in items or materials. This systematic approach not only streamlines diagnostics but also enhances overall integrity. The main flaw categories are as follows:
-
Critical Issues: These issues present a direct safety hazard or can cause product failure, rendering the item unfit for consumer use. Their impact is profound, often leading to severe consequences for both the manufacturer and the end user. OpsNinja's tailored checklist support ensures that quality checks are specifically designed to identify and mitigate these risks effectively.
-
Major Issues: Although not immediately life-threatening, major issues signify substantial deviations from established specifications. These flaws can severely compromise functionality, potentially resulting in customer dissatisfaction and compliance issues. By tailoring inspection processes according to the recognition of significant issues, OpsNinja assists companies in upholding compliance and operational standards.
-
Minor Flaws: Usually aesthetic in nature, minor flaws do not significantly hinder the item’s functionality or safety. However, they can affect customer perceptions and satisfaction, which is crucial in a competitive marketplace. OpsNinja's customized strategy enables companies to tackle these cosmetic problems without sacrificing overall product excellence.
Comprehending these defect categories is essential for executing effective control measures. Furthermore, understanding AQL (Acceptable Quality Level) numbers is essential for D2C brands to establish quality standards and protect against negative reviews. AQL figures assist in identifying the permissible quantity of flaws in a batch, thereby directing the sampling procedure during evaluations. For example, a significant flaw may have a stricter AQL number compared to a minor issue, guiding inspectors on how many items to test based on the severity of the flaw.
Traditional methodologies, such as Lean and Six Sigma, emphasize the importance of addressing critical and major defects, with Six Sigma aiming for a defect rate of just 3.4 per million opportunities. Significantly, the contributions of management pioneers such as Walter A. Shewhart and W. Edwards Deming have established the foundation for these methodologies, showcasing their effectiveness in enhancing service standards.
Furthermore, as reported by Statista, the average expenditure per employee on learning and development rose in 2021 to nearly $1300 per worker, emphasizing the significance of investing in training for management practices. This investment not only promotes a culture of continuous improvement but also ensures that employees are equipped with the necessary skills to maintain quality standards.
By focusing on these classifications and utilizing customized quality control solutions from OpsNinja, companies can enhance reliability and build customer trust, ultimately unlocking greater growth potential in the eCommerce sector.
Exploring Different Types of Defects: Design, Manufacturing, and Labeling
Defects in development can be classified into three primary categories, each presenting unique challenges that can significantly affect customer satisfaction and brand reputation:
-
Design Defects: These flaws arise when an item is inherently flawed in its design, resulting in functionality issues or safety hazards. For instance, a chair designed without adequate support not only fails to perform as intended but can also pose serious risks to users. According to Columbia Business School Publishing, a staggering 66% of new offerings fail within two years of launch, often due to design shortcomings that do not align with customer needs.
-
Manufacturing Defects: These arise during the production process when the final item deviates from its intended design. An illustrative example is a batch of electronics that malfunctions due to improper assembly. Research indicates that the manufacturing defect rates vary widely by industry, with some sectors facing challenges that can lead to significant recalls and financial losses. Recent item recalls have highlighted the necessity of strict control measures, as demonstrated by Ops Ninja's inspections, which assisted Amazon seller Maurice Mann in recovering $1 million in revenue by enhancing ratings from 3.5 to 4.7 stars. Such quality control initiatives not only mitigate risks but also enhance partnerships with brands, enabling them to thrive in competitive markets.
-
Labeling Defects: These involve inaccuracies or omissions in labeling that can mislead consumers or fail to provide essential safety information. A relevant example is a food item lacking allergen warnings, which could have dire consequences for sensitive consumers. The consequences of labeling defects go beyond consumer safety; they can result in legal liabilities and harm to company integrity.
Comprehending these types of defects is vital for professionals in the field. By proactively addressing potential risks associated with design, manufacturing, and labeling, brand owners can foster a more reliable development process that enhances customer engagement and loyalty. Moreover, it’s important to note that highly engaged customers tend to spend 23% more, underscoring the financial impact of ensuring quality.
As highlighted by Steve Jobs, > You’ve got to start with the customer experience and work back toward the technology, not the other way around. < This philosophy is essential for minimizing defects and ensuring success. Furthermore, OpsNinja's comprehensive inspection reports provide detailed recommendations, including photos, videos, and actionable inspection instructions, that protect companies against negative reviews, ensuring a strong market presence.
Certain brands, including Caddent Golf and Karma Heart, have gained from these insights, emphasizing the importance of thorough inspections in maintaining quality.
The Impact of Defects Across Industries: From Manufacturing to Healthcare
Defects pose significant challenges across various industries, with each industry facing its own defect categories and consequences.
- Manufacturing: In this sector, flaws that fall under various defect categories can trigger product recalls, leading to substantial financial losses and lasting damage to a company's reputation.
Based on recent industry insights, unplanned downtime caused by issues can severely affect productivity, reinforcing the need for predictive maintenance strategies. As highlighted by Jim Davison, region director at Make UK,
One of the biggest challenges manufacturers face is reducing the amount of unplanned downtime, and the figures in Senseye’s report clearly show the huge cost impact of not doing this.
This is where OpsNinja excels as a modern control platform, offering tailored teams and high-touch services that help D2C brands effectively address defect categories.
OpsNinja utilizes advanced technology, including real-time data analytics and customizable inspection protocols, to enhance operational efficiency and minimize risks. With Fictiv's experience in producing over 25 million components, the significance of addressing flaws becomes even more evident, as it directly relates to maintaining operational efficiency and minimizing risks.
Healthcare: The stakes are particularly high in the healthcare industry.
Defects in medical devices or pharmaceuticals can be classified into defect categories that jeopardize patient safety and result in severe legal ramifications. A notable statistic reveals that medical device recalls affected a staggering 83.3 million units, reflecting a dramatic increase of over 34%. An issue in a heart valve can lead to serious patient complications, underscoring the critical nature of quality assurance in this field.
OpsNinja's expert inspections play a vital role in ensuring compliance and safeguarding patient safety, reinforcing company integrity.
Consumer Goods: In the realm of consumer products, defect categories can lead to customer dissatisfaction, high return rates, and a detrimental loss of brand loyalty. The implications of these defects extend beyond immediate financial losses; they can erode trust and long-term relationships with customers.
Brands must recognize these impacts to effectively prioritize quality control measures and enhance customer safety, ultimately safeguarding their market position. As Christine Evans, Sr. Director of Marketing at Fictiv, states,
From technological advancements and changes in labor, to shifts in international trade, these insights will give you a comprehensive overview of the state of manufacturing in 2024.
This perspective emphasizes the pressing need for companies to adapt to evolving challenges, particularly those highlighted in customer pain points, to ensure sustained success.
OpsNinja's dedication to delivering dependable inspections guarantees that D2C companies can safeguard their reputation and uphold customer trust. As Amy Wees observes,
We prevent manufacturing problems from reaching customers, safeguarding your brand from negative reviews and poor customer experiences,
highlighting the increasing necessity for stringent control in today's competitive environment.
Methods for Detecting and Classifying Defects: Techniques and Tools
Identifying and categorizing issues in items is essential for upholding standards, and Ops Ninja offers various advanced methods and tools to aid this process:
-
Visual Inspection: This essential method depends on skilled individuals to assess products for visible flaws, acting as the primary barrier against quality concerns. Recent advancements have improved the effectiveness of visual inspections, with enhanced training techniques leading to better detection rates. Comprehensive reports, including photos and inspection instructions, empower brand owners to act on results effectively by identifying specific areas for improvement and addressing potential issues proactively.
-
Automated Inspection Systems: Utilizing sophisticated technology like high-resolution cameras and sensors, automated inspection systems can detect defects in real-time during production. These systems have demonstrated impressive effectiveness, with the YOLOv5s model achieving an accuracy rate of 98.4% for fractures and 85.1% for bubbles, alongside a remarkable processing speed of 137.2 frames per second (FPS). Techniques such as Mosaic data augmentation further enhance system capabilities, tripling the training set size and improving mean Average Precision (Map) significantly.
-
Tailored Quality Checks: OpsNinja collaborates closely with your quality team to recommend quality checks specifically designed for your offering, ensuring that every inspection is unique to your needs. For instance, a tailored checklist for a fragile product may focus more on impact resistance, while one for a food item might prioritize hygiene standards. This customized approach is crucial for direct-to-consumer brands aiming to safeguard their reputation against negative reviews.
-
Statistical Process Control (SPC): This method employs statistical tools to monitor and control manufacturing processes, enabling the identification of variations that may signal potential defects. By analyzing data trends, manufacturers can proactively address defect categories related to quality issues before they escalate.
Failure Mode and Effects Analysis (FMEA): A systematic approach to identifying potential defect categories within a product and assessing their impact, FMEA assists professionals in prioritizing risk factors and implementing preventive measures.
Universal Framework for Random Sample Consensus (USAC): This framework enhances the robustness of defect detection techniques, ensuring that systems are resilient against outliers and improving overall accuracy.
By integrating these techniques, professionals can significantly enhance their defect management processes. This is essential in safeguarding companies from negative customer experiences and evaluations. Embracing advancing inspection technologies, such as those provided by OpsNinja, is crucial for ensuring item excellence and customer contentment. As one expert aptly stated,
Build trust with stakeholders during a private equity exit by communicating regularly, involving them in decisions, and being transparent about risks.
This philosophy is crucial in fostering a quality-driven culture within organizations.
Understanding Acceptable Quality Levels (AQL) in Defect Management
The Acceptable Quality Level (AQL) serves as a pivotal statistical metric that delineates the maximum number of defective items deemed acceptable within a defined sample size. A clear understanding of AQL is crucial for effective issue management and strong quality assurance, especially for D2C label owners seeking economical inspection solutions.
-
Setting AQL Levels: Establishing suitable AQL levels requires a careful balance between ensuring customer satisfaction and maintaining cost-effectiveness. An excessively stringent AQL can lead to inflated costs due to unnecessary rework or product rejection, while a lenient AQL risks harming the company's reputation by permitting too many flaws to slip through. For example, with a lot size of 50,000 units and an AQL of 2.5, sampling 500 units would allow a maximum of 21 flaws, underscoring the importance of precision in setting these levels. OpsNinja's customized pricing options guarantee that your control strategies stay cost-effective while enhancing protection and offering reassurance.
-
AQL Sampling Plans: Implementing AQL effectively requires developing a comprehensive sampling plan that defines the methodology for selecting and evaluating samples. Common approaches include single, double, and multiple sampling plans, each offering different levels of scrutiny and acceptance criteria. A recent conversation among industry experts emphasized that surpassing minor defect limits could result in a rejection, even when significant flaws are present—an aspect vital for D2C companies striving to improve control standards and boost revenue recovery. For example, Neil Ayton's expertise in overseeing standards control for his e-commerce ventures demonstrates how customized inspections can greatly reduce risks linked to defects.
-
Ongoing Monitoring: Ongoing assessment and modification of AQL levels are crucial to adjust to changing product performance and customer input, guaranteeing ongoing enhancements in standards. By committing to a dynamic SQL strategy, professionals can uphold high-quality standards while simultaneously controlling costs. This adaptability is especially pertinent considering recent discussions, like Big Jim's remark that no one is presently certified to AS9100:2004, questioning the significance of outdated requirements in today's management landscape. Moreover, as articulated by industry expert Heretical Statistician, 'All they really do is make you feel better about the lot without any real evidence that the feeling is warranted.' Therefore, grounding AQL practices in real-world data and outcomes is essential to justify their use. By understanding and implementing AQL effectively, quality assurance professionals can navigate the complexities of defect management and address various defect categories, all while enhancing brand integrity and customer trust—central to OpsNinja's mission to provide customized quality control solutions that offer peace of mind for D2C brands.
Conclusion
Defect categories play a pivotal role in quality management, offering a structured approach to identifying and addressing various types of defects that can compromise product integrity. By categorizing defects into critical, major, and minor classifications, professionals can tailor their quality assurance strategies effectively. Understanding the implications of these defects across industries—from manufacturing to healthcare—highlights the necessity for rigorous quality control measures. The consequences of neglecting defects can range from financial losses to serious safety hazards, reinforcing the importance of proactive defect management.
Moreover, the methodologies for detecting and classifying defects are vital for maintaining high-quality standards. Advanced techniques such as visual inspections, automated systems, and tailored quality checks facilitate early detection and resolution of potential issues. By incorporating statistical tools like AQL and FMEA, organizations can not only manage defects more efficiently but also enhance overall product reliability.
Ultimately, the commitment to understanding and addressing defect categories is essential for fostering customer trust and ensuring long-term success in a competitive marketplace. By leveraging robust quality management practices, brands can safeguard their reputation, enhance customer satisfaction, and drive growth in the evolving landscape of eCommerce. The emphasis on continuous improvement and investment in quality control is not just beneficial; it is imperative for thriving in today's business environment.