How to Conduct an Effective Procedure of Inspection: A Step-by-Step Guide
Master the procedure of inspection with our step-by-step guide for effective quality control.
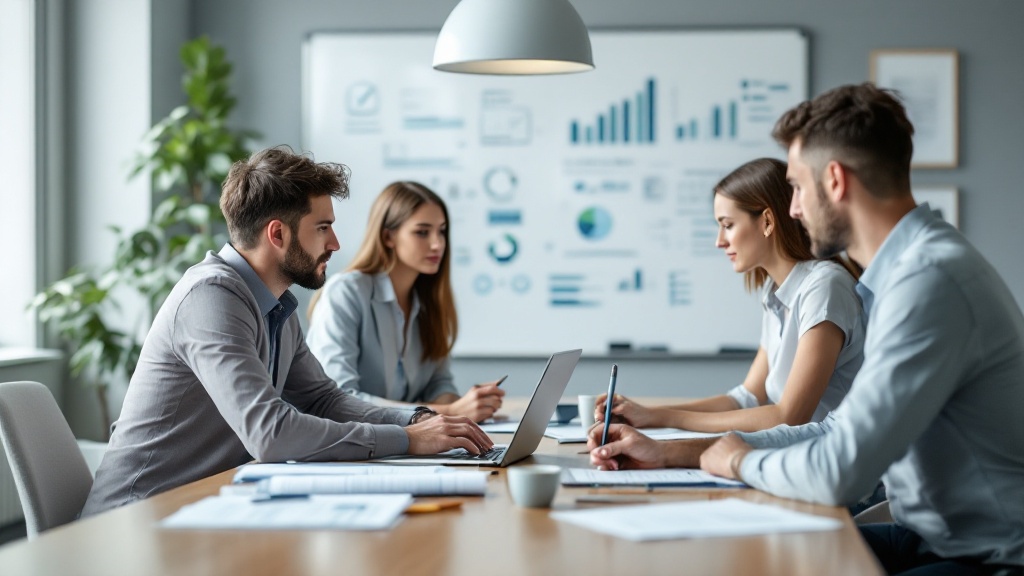
Key Highlights:
- First Article Inspections (FAIs) assess initial production runs to ensure compliance with specifications and industry standards.
- FAIs involve collaboration between buyers and suppliers for effective communication and compliance.
- Key documentation, such as the FAI Report, outlines inspection criteria and results for regulatory adherence.
- AQL (Acceptable Quality Level) numbers guide inspectors on testing standards within production batches.
- Effective preparation for inspections includes defining criteria, gathering data, training personnel, and scheduling assessments.
- Critical actions during inspections involve visual assessments, measuring dimensions, checking compliance, and documenting findings in real-time.
- Post-inspection actions include compiling reports, communicating findings, implementing corrective actions, and fostering a culture of continuous improvement.
- Successful FAIs can lead to significant revenue recovery and brand protection, as demonstrated by case studies of Maurice Mann and The Mindful Collective.
Introduction
In the dynamic realm of manufacturing, First Article Inspections (FAIs) serve as a critical checkpoint, ensuring that the initial production runs meet stringent quality standards and specifications. These inspections not only confirm that processes are capable of consistently delivering compliant components but also foster essential collaboration between buyers and suppliers.
By understanding the intricacies of FAIs, organizations can proactively address potential issues, safeguarding against costly errors and enhancing regulatory adherence. The importance of meticulous documentation, such as the FAI Report, cannot be overstated, as it provides a clear framework for quality assurance and compliance.
Real-world success stories, like those of Maurice Mann and The Mindful Collective, further underscore the tangible benefits of robust inspection processes, illustrating how effective quality control can lead to improved product ratings and significant revenue recovery.
This article delves into the foundational elements of FAIs, offering a comprehensive guide to conducting inspections that not only meet but exceed industry expectations.
Understanding First Article Inspections: A Foundation for Effective Procedures
First Article Inspections (FAIs) play a crucial role in the manufacturing landscape, acting as a thorough evaluation of the initial production run for any part or product. The primary objective of an FAI is to confirm that the manufacturing process can consistently produce components that align with predefined requirements and industry standards. A successful FAI encompasses a detailed assessment of critical factors, including design specifications, material requirements, and production capabilities.
The collaborative nature of evaluations is emphasized by the roles and responsibilities of both the buyer and supplier, which are pivotal in ensuring effective communication and compliance throughout the FAI process. By meticulously understanding the procedure of inspection, organizations can proactively identify potential issues, thereby mitigating the risk of expensive errors and ensuring adherence to regulatory standards. Key to this procedure of inspection is the FAI documentation, particularly the FAI Report, which delineates the criteria and results of the inspection.
AQL (Acceptable Quality Level) numbers represent specific values that indicate the standard of excellence acceptable for a batch, guiding inspectors on the number of items to randomly test from a batch to statistically assure the overall standard meets specified criteria. As Ing. Mario Toyo states, 'The statistical analyses are based on the collection and evaluation of data related to the condition and operation of these pipes and equipment, in order to determine the probabilities of failure or deterioration in different parts of the system to inspect and quantify the conditions under this methodology.'
This documentation serves as a crucial reference point for compliance and assurance, emphasizing the procedure of inspection necessary to ensure manufacturing excellence. Real-world applications of FAIs, like the case study of Maurice Mann, who recovered $1 million by raising his Amazon item ratings from 3.5 to 4.7 stars through effective evaluations, illustrate the tangible advantages of adopting strong control measures. Furthermore, The Mindful Collective's shift in their method of evaluations demonstrates how their services can empower D2C brands to grow effectively on platforms such as Amazon, ultimately enhancing revenue recovery and safeguarding their brand from adverse customer experiences.
The successful evaluations not only enhanced item ratings but also guaranteed that both Maurice Mann and The Mindful Collective complied with quality standards, further strengthening their market presence.
Step-by-Step Guide to Conducting Effective Inspections
To perform effective evaluations with OpsNinja's streamlined services, adhere to the following structured steps:
- Define Inspection Criteria: Establish precise criteria that align with product specifications and regulatory requirements. This foundational step not only establishes the benchmark for your evaluations but also ensures compliance with industry standards, protecting your brand from potential negative reviews.
- Create a Review Plan: Develop a comprehensive review plan that details the scope, including specific items to be assessed, the methodologies to be employed, and the timeline for completion. With OpsNinja’s simple reservation procedure and storefront integrations, you can swiftly arrange evaluations customized to your requirements, ensuring effective assurance of standards.
- Gather Necessary Tools: Compile all required tools and equipment for the evaluation phase. This includes calipers, gauges, and digital checklists, which enhance accuracy and efficiency. Employing the latest tools and technologies, like those available in Six Sigma.us' Live Virtual classes, supported by a community of over 4,346 followers, can offer invaluable training in quality assessment processes. Follow the procedure of inspection by methodically assessing each aspect of the product according to the established criteria. It’s crucial to maintain consistency and thoroughness to ensure all elements are evaluated effectively. By scheduling evaluations through the platform, you can ensure that skilled experts perform this essential duty.
- Document Findings: Accurately record all observations, measurements, and any deviations from the defined criteria in a detailed evaluation report. Thorough evaluation reports from OpsNinja are essential for transparency and protecting your brand from adverse customer experiences.
- Review and Analyze Data: Analyze the collected data to identify trends or recurring issues that may require attention. This step is essential for ongoing enhancement and upholding high standards, ensuring customer satisfaction through the procedure of inspection and proactive management of excellence.
- Implement Corrections: Should any non-conformities arise, take immediate corrective actions to resolve the issues. As Will Jocson, Founder of MaintainIQ, emphasizes,
By bringing simplicity & ease-of-use to food safety, digital checklists & preventive maintenance help boost productivity and streamline operations.
Implementing such strategies can enhance the effectiveness of your evaluations and ensure compliance with quality standards.
For example, a case study on surface finish measurement highlights how effective assessment criteria can evaluate product surfaces for roughness and imperfections, ensuring they meet desired quality standards. By adhering to these steps and utilizing the evaluation services, manufacturers can not only enhance their assessment processes but also boost customer satisfaction and loyalty, ultimately resulting in a stronger market position. To learn more about how OpsNinja can help you, Contact sales or Create a Free Account today!
Preparing for Inspections: Planning and Data Collection
Effective preparation for evaluations necessitates a systematic approach that encompasses several critical steps:
-
Develop a Review Plan: It is essential to create a detailed review plan that outlines objectives, scope, and methodologies. This plan should clearly define timelines and responsibilities, ensuring all team members understand their roles. OpsNinja's dedicated support team is available to assist in crafting these plans, enhancing the overall customer experience in supply chain management across 16+ countries.
Collect Relevant Data: Gather all pertinent documentation, including product specifications, historical review reports, and applicable standards. Comprehensive data gathering is essential for informed decision-making throughout the evaluation process. OpsNinja’s commitment to unbiased quality control ensures that all necessary data is accurately collected and assessed using proven methodologies tailored to client needs. -
Train Evaluation Personnel: Training evaluation personnel is paramount, especially considering that 83% of organizations recognize the importance of developing leaders at all levels. However, it's important to note that less than 5% of businesses have adopted leadership development at all levels, indicating a significant gap in training initiatives. A well-organized staff training program acts as the initial step toward success, equipping employees to thoroughly comprehend the procedure of inspection and evaluation standards. OpsNinja emphasizes the importance of training to prevent product returns and ensure a reliable procedure of inspection.
Prepare Inspection Tools: Confirm that all tools and equipment are calibrated and in optimal working condition before the assessment. This preparation minimizes the risk of errors and enhances the reliability of evaluation results. At OpsNinja, we ensure that the tools utilized for evaluations meet the highest standards to guarantee quality.
Schedule the Assessment: Coordinate with all relevant stakeholders to arrange the assessment. Timing is essential; the evaluation should be scheduled to minimize disruption to production while ensuring the availability of all necessary personnel. With the assistance of OpsNinja's support, brands can optimize the scheduling process to improve operational efficiency.
Considering recent developments, including the anticipation that 41% of L&D leaders will receive a larger budget in 2023, organizations have a chance to invest more in training programs that enhance the skills of evaluation personnel. Addressing the challenges in compliance training—where 23% of companies lack a formal compliance training plan, as highlighted in the case study 'Challenges in Compliance Training'—underscores the necessity for improved strategies that ensure thorough and effective training. OpsNinja’s leadership excellence in the field offers a model for best practices in compliance and assurance.
Executing the Inspection: Key Actions and Considerations
When conducting an evaluation for clothing and fashion items, especially D2C brands, it is essential to concentrate on the following key actions to guarantee thoroughness and adherence, thereby improving control standards and boosting customer satisfaction:
- Follow the procedure of inspection: Strict adherence to the established criteria and methodologies outlined in the procedure of inspection is essential for maintaining consistency and reliability throughout the process.
- Conduct Visual Inspections: An initial visual assessment should be carried out to identify any obvious defects, irregularities, or signs of damage that could compromise the standard. This step is vital, as statistics reveal that common faults in various settings often include issues with structural integrity and system functionality.
- Measure Critical Dimensions: Employ calibrated tools to accurately measure critical dimensions of the product. These measurements should be compared against specifications to ensure conformity, as even minor discrepancies can lead to significant issues with standards. For instance, a customer testimonial from Kari Fineran highlights how OpsNinja identified sizing discrepancies that her supplier overlooked, showcasing the importance of precise measurements in preventing returns.
- Check for Compliance: It's imperative to ensure that the procedure of inspection verifies the item meets all relevant regulatory and excellence standards. This not only ensures safety but also avoids potential legal ramifications for non-compliance.
- Engage with Production Staff: Effective communication with production personnel is necessary to gain insight into any challenges or issues encountered during production. Such discussions can uncover underlying concerns that may not be readily apparent, assisting in addressing issues proactively.
- Document Findings in Real-Time: The importance of real-time documentation cannot be overstated. Recording observations and measurements as they occur ensures accuracy and completeness. Adam Long, president of HomeTeam Inspection Service, emphasizes this point, noting that immediate documentation aids in tracking defects and guiding prompt corrective actions. This is especially pertinent in the clothing sector, where prompt recognition of flaws can greatly lessen expenses linked to returns and unsellable stock.
By focusing on these measures, evaluation specialists can improve the efficiency of their assessments and aid in achieving better overall product standards. With an excellent customer rating of 4.8 out of 5, OpsNinja is committed to providing tailored quality control solutions for D2C brands. Get started today—talk to sales to learn how we can assist in enhancing your evaluation processes.
Post-Inspection Actions: Reporting and Continuous Improvement
Upon completing an inspection, it is crucial to take the following post-inspection actions to ensure effective outcomes:
-
Compile Evaluation Reports: Begin by summarizing the findings from the assessment, detailing any non-conformities. A detailed report, which includes photos, videos, and guidance, not only documents the issues identified but also serves as a baseline for future improvements. This detailed reporting is vital for safeguarding your brand against negative reviews and customer issues.
-
Communicate Findings: Transparency is key; share the inspection results with all relevant stakeholders, including production teams and management. This open communication fosters accountability and encourages collaborative problem-solving, crucial for maintaining high product ratings.
-
Implement Corrective Actions: When issues are identified, it is essential to collaborate with the production team to develop and implement corrective actions that address the root causes. As emphasized by Garcia, "later we see the problem being manifested or we do not see that there is a continuous analysis of the quality data sources to see whether the problem repeats itself." This highlights the necessity of proactive measures in the procedure of inspection to prevent recurrence, especially during peak periods for accidents, which typically occur in the second to fourth hours of working hours and the first hour before the end of work.
-
Review and Adjust Processes: Analyze the evaluation findings to identify trends or recurring issues. Adjusting processes based on this analysis is vital for preventing future occurrences, particularly in environments where operational issues are prevalent, such as in coal mine safety management systems. OpsNinja’s evaluation services have proven transformative, enabling brands to scale effectively.
-
Foster a Culture of Continuous Improvement: Cultivating a mindset of continuous improvement within the organization is essential. Consistently evaluating assessment methods and results, while soliciting input from all parties involved, improves overall standards. The application of structured approaches like the PDCA (Plan, Do, Check, Act) cycle can significantly support organizations in systematically planning, implementing, assessing, and revising corrective actions to mitigate nonconformities. For instance, the successful application of the PDCA cycle in addressing nonconformities in construction projects demonstrates how organizations can effectively manage corrective actions and prevent recurrence.
By adopting these post-inspection actions within their procedure of inspection, organizations not only improve their operational standards but also align themselves with evolving best practices in management. The experiences of clients like Maurice Mann, who recovered $1 million in revenue by boosting product ratings from 3.5 to 4.7 stars, and The Mindful Collective, which transformed their approach to quality control, illustrate the potential for significant brand protection and revenue recovery through effective inspection practices.
Conclusion
First Article Inspections (FAIs) are undeniably pivotal in the manufacturing sector, serving as a safeguard for quality assurance and compliance. Throughout the article, the critical steps involved in conducting effective FAIs have been meticulously outlined, from defining inspection criteria to implementing corrective actions post-inspection. These processes not only help in identifying and mitigating potential issues but also foster collaboration between buyers and suppliers, ultimately enhancing product quality and brand reputation.
Moreover, real-world examples, such as:
- Maurice Mann's remarkable revenue recovery
- The Mindful Collective's successful transformation
demonstrate the tangible benefits of a rigorous inspection framework. These success stories underscore the importance of investing in quality control measures, which can lead to improved product ratings and significant financial gains.
In conclusion, understanding and effectively implementing FAIs is essential for any organization aiming to thrive in a competitive market. By prioritizing quality assurance through meticulous documentation and proactive inspections, manufacturers can ensure compliance, safeguard their brand, and drive customer satisfaction. The pathway to operational excellence lies in embracing these best practices, ultimately leading to a sustainable and successful manufacturing process.