How to Conduct a Pre Shipment Inspection in China: A Step-by-Step Guide
Learn how to effectively conduct a pre-shipment inspection in China with our comprehensive guide.
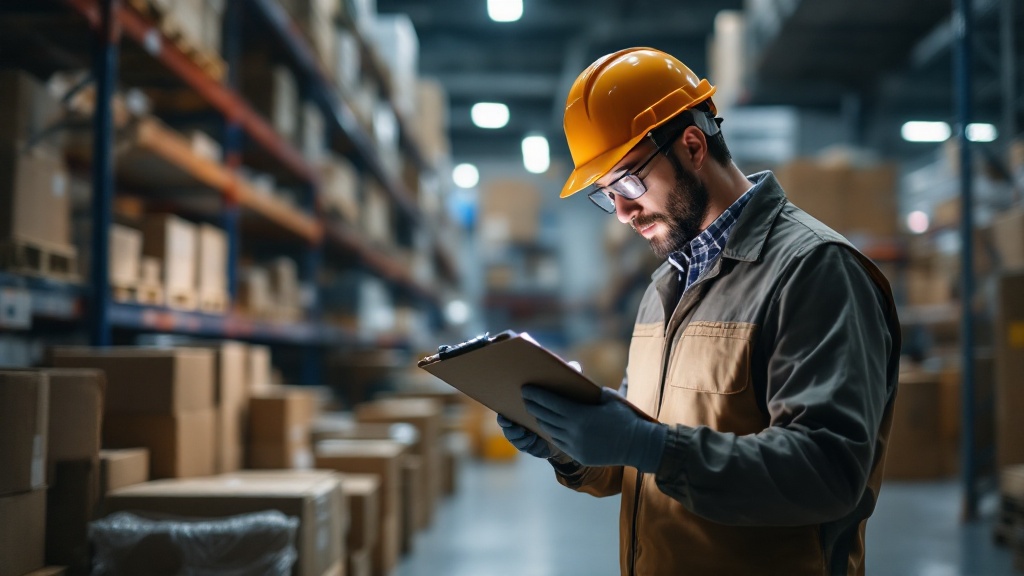
Key Highlights:
- Pre-shipment inspections in China confirm goods meet standards, are defect-free, and comply with contracts before shipment.
- OpsNinja enhances D2C companies' control processes, exemplified by The Mindful Collective's success on Amazon.
- Implementing PSIs can lead to a 30% reduction in defects, improving consumer trust and brand loyalty.
- A comprehensive inspection process includes preparation, initial assessments, sampling, product inspections, documentation, and follow-ups.
- Adopting Acceptable Quality Level (AQL) standards ensures a statistically significant sample is evaluated to maintain quality.
- The final inspection report details defects and required actions, aiding in future production improvements.
- Challenges in PSIs include language barriers and differing standards; local expertise can mitigate these issues.
- Investing in PSIs is a strategic decision that enhances customer satisfaction and strengthens supplier relationships.
Introduction
In the competitive landscape of direct-to-consumer (D2C) brands, ensuring product quality before reaching customers is paramount. Pre-shipment inspections (PSIs) serve as a vital safeguard, verifying that products meet established standards and are free from defects.
As the industry evolves, advancements in technology are reshaping the inspection process, making it more efficient and effective. Companies like OpsNinja are at the forefront of this transformation, demonstrating the significant impact of PSIs on brand reputation and customer satisfaction.
By understanding the intricacies of PSIs and implementing robust quality control measures, brands can not only minimize risks associated with product quality but also enhance their market presence and consumer trust.
This article delves into the essential aspects of pre-shipment inspections, providing a comprehensive guide to navigating this critical process.
Understanding Pre-Shipment Inspections: What You Need to Know
Pre-shipment inspections in China act as essential control measures carried out before the dispatch of items from manufacturers to buyers. Their main objective is to confirm that goods adhere to predefined standards, are free from defects, and comply with contractual agreements. This process encompasses thorough evaluations of product specifications, packaging integrity, and labeling accuracy.
OpsNinja has shown the transformative influence of PSIs on D2C companies, assisting organizations like The Mindful Collective to grow on Amazon by enhancing their control processes. Additionally, entrepreneur Neil Ayton has shared insights on how OpsNinja assists in managing diverse suppliers and establishing robust quality control processes for his portfolio of brands, including Cadent Golf, Karma Heart, and Luminate Press. As the pre-shipment evaluation market evolves, recent technological advancements are revolutionizing the industry, enhancing efficiency and precision in the assessment process.
According to industry experts, 'there is significant innovation on the horizon,' which is set to transform how evaluations are conducted. Moreover, recent news underscores key trends in the pre-shipment evaluation market, emphasizing the role of technology in enhancing assessment outcomes. For D2C brand owners, comprehending the scope and purpose of pre shipment inspection in china is crucial; these inspections not only protect a brand's reputation but also play a key role in ensuring customer satisfaction.
Studies indicate that adopting strong PSIs can result in a 30% decrease in defects, effectively reducing risks linked to standards and ultimately enhancing consumer trust and loyalty. Furthermore, success stories from clients such as Maurice Mann demonstrate how OpsNinja's inspections aided in recovering $1 million in revenue by enhancing product ratings from 3.5 to 4.7 stars, highlighting the tangible benefits of incorporating comprehensive assurance measures. Hash Stash's experience further highlights how Ops Ninja has streamlined their control processes, allowing them to scale operations effectively.
For more insights and success stories, explore additional resources on how OpsNinja can transform your brand's oversight.
Step-by-Step Guide to Conducting a Pre-Shipment Inspection
- Preparation: Effective pre shipment inspection in China begins with thorough preparation. Gather all pertinent documents, such as purchase orders, product specifications, and applicable quality standards. Confirm the assessment date and time with your supplier to ensure mutual understanding and readiness.
Initial Assessment: Upon arriving at the factory, conduct a preliminary assessment of the production environment. Evaluate cleanliness, organization, and overall operational efficiency. This initial observation sets the stage for a more detailed inspection and highlights the importance of maintaining high standards to protect your brand from negative reviews.
- Sampling: Selecting a representative sample of products is crucial for precise evaluation. Adhere to Acceptable Quality Level (AQL) standards to ensure that your sample is statistically significant, allowing you to gauge the overall standard of the shipment effectively. AQL numbers assist inspectors in determining how many items to randomly test from a batch, ensuring that standards are met and protecting your brand's reputation.
Product Inspection: Methodically inspect the selected samples for defects and conformity to the established specifications. This step involves scrutinizing dimensions, functionality, and appearance. Thorough evaluations allow you to recognize potential problems early, which is essential for upholding product quality and preventing adverse customer experiences.
Documentation: Meticulous documentation is essential throughout the evaluation process. Record your findings in detail, noting any defects or discrepancies. Accompany your notes with photographs and videos as evidence to support your assessments and recommendations, thus creating a comprehensive review report that can protect your brand's integrity.
Final Report: After concluding the assessment, prepare a comprehensive review document that summarizes your findings and recommendations. This report should include photos and videos, and be distributed to all relevant stakeholders, ensuring transparency and informed decision-making, which plays a crucial role in preventing negative reviews from dissatisfied customers.
Follow-Up: Should any defects be identified, promptly communicate with your supplier to rectify the issues before shipment. This proactive approach not only addresses potential problems but also helps uphold the manufacturer’s reputation, as highlighted in the case study on workmanship verification, where visual checks classified defects and maintained quality standards prior to customer delivery. Significantly, some nations mandate a pre shipment inspection in China for customs clearance, emphasizing the importance of thorough assessments at this stage. Furthermore, QIMA assessors can be present anywhere globally within 48 hours, with evaluation reports provided on the same day as the assessment, highlighting the effectiveness and quickness of the assessment process to protect your reputation.
The Importance and Benefits of Pre-Shipment Inspections
The implementation of pre shipment inspection in China is crucial for upholding quality and dependability in the competitive environment of D2C companies. By identifying defects prior to delivery, a pre shipment inspection in China significantly reduces the likelihood of returns, safeguarding brand reputation. For instance, OpsNinja helped Maurice Mann recover $1 million in revenue by boosting his Amazon product ratings from 3.5 to 4.7 stars, showcasing the tangible benefits of effective inspections.
Similarly, The Mindful Collective transformed their approach to quality control through OpsNinja's services, enabling them to scale on Amazon successfully. Additionally, OpsNinja offers customized pricing options tailored to the specific needs of D2C brands, which enhances the financial implications of implementing PSIs. These evaluations can yield substantial cost savings; they minimize the necessity for post-shipment assessments and the associated expenses of handling returns, particularly when implementing pre shipment inspection in China.
The final inspection report produced from the pre shipment inspection in China consolidates inspection results into a detailed document that highlights defects and required actions, providing insights that assist in enhancing future production processes and control measures. According to HTF Market Intelligence, 'Insights are drawn using financial analysis, surveys, and industry consultants,' confirming that leveraging such evaluations leads to better decision-making and supplier relationships. Furthermore, the Enterprise User Access costs $4750, which can be shared globally by unlimited users within the organization, highlighting the financial implications of implementing PSIs.
In 2024, companies that implement pre shipment inspection in China can expect enhanced customer satisfaction and trust, ultimately fostering long-term partnerships with suppliers. Therefore, incorporating pre shipment inspection in China into the sourcing strategy is not merely an operational task; it is a critical investment in the brand's future success, reinforcing the insights of Neil Ayton on managing diverse suppliers and establishing quality control processes across his portfolio.
Key Standards and Criteria for Effective Inspections
Effective pre-shipment inspection in China hinges on adhering to key standards, prominently including the Acceptable Quality Level (AQL). AQL specifies the maximum permissible number of defective items within a sample batch; for instance, an agreed AQL of 1% for a batch of 500 items means that if one or fewer defects are detected, the batch is accepted. As noted by experts, if 1 or fewer defects are found, the batch will be accepted.
If 2 or more defects are found, the entire batch will be rejected. However, it is important to note that AQL sampling does not guarantee zero defects, which sets realistic expectations for assurance. OpsNinja addresses this by providing customized checklist assistance, ensuring that checks are tailored for each unique product, rather than using a one-size-fits-all strategy.
This flexibility is crucial for D2C companies, particularly when collaborating with unfamiliar manufacturers. Additionally, OpsNinja provides total peace of mind, allowing your team to focus on building the business rather than managing operations and customer complaints. The importance of on-location evaluations cannot be overstated, as Return Logic indicates that 60% of returns stem from preventable quality issues.
By implementing thorough pre-shipment inspection in China, you not only adhere to AQL but also enhance reliability, ultimately safeguarding your brand's reputation against negative reviews. Beyond AQL, it is crucial to consider other criteria such as precise specifications, packaging requirements, and adherence to safety regulations. For instance, recent updates on examination gloves standards include:
- AS/NZS 4011:2014
- ASTM D3578:19
- EN 455-1:2020
- ISO 11193-1:2020
- JIS T9115:2008
These highlight the importance of AQL application in ensuring compliance with safety regulations.
Understanding these standards is vital for ensuring that items not only meet buyer expectations but also comply with relevant regulatory frameworks. This thorough method for evaluations, supported by OpsNinja’s expertise, is crucial for promoting assurance while reducing risks linked to non-compliance, particularly through pre-shipment inspection in China.
Navigating Challenges in Pre-Shipment Inspections in China
Carrying out a pre shipment inspection in China poses distinct challenges, such as language barriers, cultural differences, and differing standards that can hinder effective communication and jeopardize product integrity. Utilizing OpsNinja's dedicated support team can significantly enhance this process. Our local assessors provide invaluable market knowledge and linguistic skills, ensuring that evaluations are thorough and expectations are clearly communicated with suppliers.
As one pleased client, Kari Fineran, observed, our team identified inconsistencies in sizing that her supplier had missed, highlighting our dedication to impartial standards management in supply chain evaluations.
OpsNinja provides a variety of services, including:
- Thorough item assessments
- Supplier evaluations
- Assurance consulting
All tailored to meet the particular requirements of companies sourcing from China. To further mitigate risks, it's crucial to establish clear communication channels with suppliers before evaluations. This ensures that expectations are well-defined, reducing misunderstandings and improving overall efficacy.
Conducting a risk assessment beforehand can help identify potential control issues, allowing brands to proactively address challenges that may arise.
Recent statistics reveal that the European Union enforces stringent requirements for goods entering the market to protect consumers from substandard products. This highlights the critical need for rigorous standards in pre shipment inspection in China. An expert insight reminds us to 'address unexpected expenses by reviewing spending, tapping into savings, and negotiating with vendors,' emphasizing the importance of being prepared and adaptable in assurance practices.
Brands that invest in local expertise and proactive communication strategies typically experience higher quality products and reduced inspection-related costs, reinforcing the value of quality support services like those offered by OpsNinja.
Conclusion
Pre-shipment inspections (PSIs) are an indispensable component of quality control for direct-to-consumer brands, ensuring that products meet established standards before reaching consumers. By implementing thorough PSIs, brands can significantly reduce the risk of defects, thereby minimizing returns and enhancing customer satisfaction. The case studies highlighted throughout the article, such as Maurice Mann's success in recovering $1 million in revenue and The Mindful Collective's improved quality control processes, underscore the tangible benefits that effective inspections can yield.
Moreover, the evolution of technology is transforming the PSI landscape, streamlining inspections and improving accuracy. As brands increasingly recognize the importance of PSIs, they are also finding that adhering to key standards, such as Acceptable Quality Levels (AQL), is crucial for maintaining product reliability. The insights shared by industry experts further emphasize the necessity of customized quality checks to suit diverse product needs, ensuring that brands can confidently navigate the complexities of international sourcing.
In conclusion, integrating robust pre-shipment inspections into a brand's operational strategy is not merely an operational task; it is a strategic investment in the brand's future success. By prioritizing product quality through diligent inspections, brands can enhance their reputation, build consumer trust, and ultimately drive sustainable growth in an increasingly competitive market.