Mastering ISO 13485 Auditing: An In-Depth Tutorial for Quality Managers
Master ISO 13485 auditing with essential steps for quality managers to ensure compliance and success.
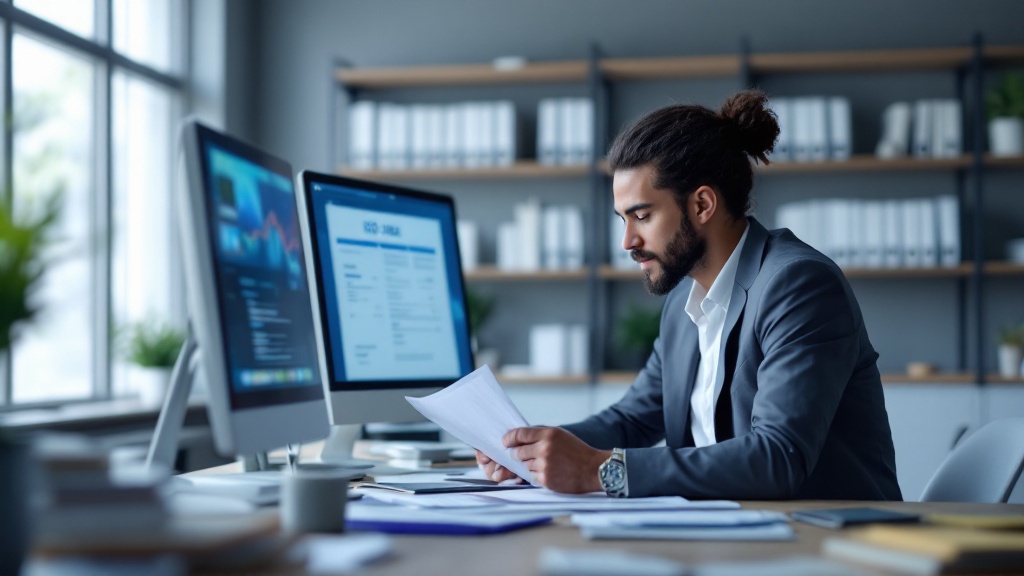
Key Highlights:
- ISO 13485 sets a framework for quality management systems specifically for the medical device industry, focusing on compliance and excellence.
- Key components of ISO 13485 include risk management, documentation control, and a commitment to continuous improvement.
- 3D printing can reduce energy usage by up to 64% in manufacturing processes, showcasing efficiency in the medical device sector.
- Conducting a gap analysis is essential for identifying discrepancies between current practices and ISO 13485 standards.
- Developing a structured review plan and involving stakeholders is crucial for effective audit preparation.
- Training staff on ISO 13485 standards enhances compliance and operational efficiency.
- Thorough documentation is vital for audit success, including maintaining records of training, process validation, and change control.
- Common pitfalls in ISO 13485 audits include neglecting documentation, inconsistent processes, and poor management reviews.
- Implementing corrective actions promptly after audits is essential for maintaining compliance and improving quality management systems.
- Promoting a culture of quality and continuous improvement within organizations enhances adherence to ISO 13485 standards.
Introduction
In the highly regulated medical device industry, adherence to quality standards is not just a regulatory requirement; it is a commitment to safety and efficacy that can significantly impact patient outcomes. ISO 13485 serves as the cornerstone of a robust quality management system, guiding organizations through the complexities of compliance while promoting continuous improvement.
This article delves into the fundamental principles of ISO 13485, offering insights into:
- Effective audit preparation
- Common pitfalls to avoid
- The critical role of documentation in achieving and maintaining compliance
By understanding these key aspects, organizations can not only meet but exceed the expectations of regulatory bodies and customers alike, ensuring that their products are safe, effective, and of the highest quality.
Understanding ISO 13485: The Foundation of Quality Management Systems
ISO 13485 establishes the framework for a robust management system (QMS) tailored specifically for the medical device sector. This standard underscores a process-oriented methodology encompassing the entire lifecycle of medical devices—from development and manufacturing to distribution. By emphasizing compliance with customer and regulatory standards, ISO 13485 guarantees that items not only satisfy but consistently surpass expectations for excellence.
A significant statistic is that 3D printing individual components on site can lower energy usage from manufacturing, storing, and shipping parts by up to 64 percent, demonstrating the efficiency advantages linked to management practices in this sector. Critical components of this standard include:
- Risk management, which is essential for identifying and mitigating potential hazards
- Documentation control to maintain compliance and traceability
- A commitment to continuous improvement that enhances reliability and efficacy
As Steve Bennett, a Business Formation Expert, states, 'With LLCBuddy, you're not just getting a tutorial; you're gaining a trustworthy partner for your entrepreneurial journey,' emphasizing the significance of dependable systems in achieving excellent results.
Moreover, Fluicel's Biopixlar Technology, which employs high-resolution 3D printing to produce biocomposites that replicate the insulin-producing role of the pancreas, illustrates how management systems can improve product development and efficacy in the medical device sector. Mastering these core principles is crucial for any organization aiming to excel in the field of ISO 13485 auditing, especially considering the recent updates to the standard's requirements and the increasing focus on risk management as a key aspect of quality assurance in the medical device industry.
Preparing for ISO 13485 Audits: Essential Steps and Strategies
-
Conduct a Gap Analysis: Initiating the review preparation process with a thorough gap analysis is essential. This step involves identifying discrepancies between your current practices and the standards set by ISO 13485 auditing. By pinpointing areas needing improvement, you can prioritize your efforts effectively. As highlighted by ISO 13485 auditing, conducting a gap analysis is fundamental to understanding where you stand in relation to compliance standards.
-
Develop a Review Plan: A well-structured review plan is crucial for success. Outline the scope, objectives, and timeline for the evaluation to ensure clarity. Involving key stakeholders in this process fosters alignment and commitment across the organization, which is vital for effective implementation. The 'Management Review Metrics Scorecard' can serve as a valuable tool in this phase, providing a clear overview of performance and areas needing attention, guiding future management decisions.
-
Train Your Team: Proper training is fundamental to success in evaluations. Ensure that all personnel involved in the ISO 13485 auditing are thoroughly familiar with the ISO 13485 standard and the audit process. Training sessions not only enhance team confidence but also prepare them to address potential challenges. As observed in success stories such as Maurice Mann's, where comprehension of standards directly impacted their star ratings and revenue, informed team members are essential in promoting compliance. The Mindful Collective also benefited from comprehensive training, which transformed their approach to control standards and contributed to their growth on Amazon.
-
Review Documentation: A meticulous review of all relevant documentation is necessary prior to the evaluation. Ensure that standard manuals, procedures, and records from prior evaluations are up-to-date and readily available. This step reduces surprises during the evaluation and reinforces the importance of compliance testing in maintaining product quality assurance, as demonstrated by D2C brands utilizing OpsNinja's services. Hash Stash's experience illustrates how thorough documentation led to improved operational efficiency and reduced returns.
-
Conduct Pre-Reviews: Implementing internal pre-reviews is a strategic way to simulate the evaluation environment. This practice enables you to recognize weaknesses and opportunities for enhancement before the formal evaluation occurs, thus improving your organization’s preparedness. High-risk organizations may find that conducting ISO 13485 auditing through more frequent pre-audits is beneficial, ensuring ongoing adherence to the standards. This proactive strategy not only equips you for adherence but also aligns with the effective tactics used by brands that have utilized OpsNinja's on-site inspections to avert product returns and guarantee quality.
Common Pitfalls in ISO 13485 Audits: What to Avoid
-
Neglecting Documentation: One of the primary reasons for audit failures is inadequate or poorly maintained documentation. ISO 13485 requires medical device organizations to establish a system for the identification, documentation, verification, control, and safeguarding of customer property. It is crucial to ensure that all records related to ISO 13485 auditing adherence are not only complete but also systematically organized. This documentation acts as proof of adherence and operational integrity, and its absence can lead to significant repercussions during audits. Ignoring staff training can severely compromise compliance, as failing to provide comprehensive training on ISO 13485 auditing requirements is detrimental. Regular training and awareness sessions are essential to provide staff with the knowledge they require to comply with standards. As noted by Juran,
It is most important that top management be quality-minded. In the absence of sincere manifestation of interest at the top, little will happen below.
This statement underscores the importance of a quality-focused culture initiated by leadership, which includes investing in staff education. -
Inconsistent Processes: Variability in how processes are executed can erode the credibility of the Quality Management System (QMS). It is imperative that all employees consistently adhere to established procedures. Such consistency not only enhances the reliability of the QMS but also fosters an environment of accountability and trust. Additionally, monitoring and measuring equipment must be calibrated or verified to standards, with records maintained for accuracy and precision, further ensuring quality management.
-
Poor Management Review: Regular management reviews are essential for identifying and addressing potential issues within the QMS. Management should routinely assess the system’s performance and implement necessary adjustments to ensure continuous improvement. Neglecting these reviews can result in unresolved issues that may escalate into regulatory failures. For instance, a case study on ISO 13485 requirements highlights that medical device organizations must establish and maintain suitable infrastructure for producing safe and effective devices, including controlled environments that prevent contamination and mix-ups.
-
Assuming Compliance: Complacency stemming from past compliance can be detrimental. Organizations must engage in continuous evaluation of their processes to ensure compliance with ISO 13485 auditing standards. Regular audits and evaluations can help identify gaps and strengthen a proactive approach to management, ultimately safeguarding against nonconformities, especially in the face of emerging challenges in 2024.
The Role of Documentation in Successful ISO 13485 Audits
-
Standards Manual: It is essential to maintain an up-to-date standards manual that clearly outlines the structure, processes, and procedures of your Management System (QMS). This manual not only acts as an essential reference for auditors but also demonstrates your dedication to excellence. As Juran famously stated,
It is most important that top management be quality-minded. In the absence of sincere manifestation of interest at the top, little will happen below.
This underscores the need for leadership to actively engage with the quality processes documented within the manual. -
Records of Training: Keeping meticulous records of employee training sessions—including dates, topics, and participant lists—is crucial. This documentation is not merely a formality; it shows adherence to training requirements and assures auditors of your organization’s commitment to maintaining skilled personnel, which is essential for ISO 13485 auditing. Statistics suggest that organizations with comprehensive training document adherence are more likely to succeed in ISO 13485 auditing.
-
Process Validation Records: Documenting all validation activities is imperative. This involves documenting outcomes and formulating conclusions pertinent to the item’s adherence. Such documentation provides concrete evidence that your products meet established requirements, which is vital for maintaining regulatory adherence and ensuring device safety. Records of past evaluations are essential, outlining discoveries and measures implemented. These reports are not only necessary for regulatory compliance but also showcase your organization’s commitment to continuous improvement. Comprehending previous evaluations assists in enhancing procedures and avoiding the reappearance of problems. In an ideal world, organizations should spend 2 hours planning for every hour of audit time, ensuring thorough preparation and effective outcomes.
-
Change Control Documentation: Maintaining thorough records of any modifications made to processes, items, or the QMS is crucial for guaranteeing traceability and compliance. New ISO 13485 auditing requirements emphasize the need for timely corrective actions that ensure safety and performance are not compromised. A recent case study highlighted that organizations are now held accountable for timely corrective actions and must verify that preventative changes do not adversely affect safety or performance, as outlined in recent updates concerning the responsibilities of third-party vendors involved in the medical life cycle.
-
Integrated Inspection Tracking: Leveraging OpsNinja's integrated inspection tracking platform can significantly improve your management processes. By directly integrating with your storefront, this platform not only helps you track inspections efficiently but also ensures that you adhere to best-in-class product inspection standards. With features such as real-time tracking and comprehensive reporting capabilities, OpsNinja enables you to monitor assurance metrics closely. This proactive method to assurance prevents potential issues, ultimately enhancing customer satisfaction and reinforcing your brand's reputation in the direct-to-consumer market. Moreover, the platform can facilitate the documentation of training records and evaluation results, creating a cohesive management ecosystem that aligns with your overall operational objectives.
Maintaining Compliance: Continuous Improvement After ISO 13485 Audits
-
Implement Corrective Actions: It is essential to address any nonconformities identified during the audit without delay. Organizations should develop a comprehensive corrective action plan that outlines specific steps to rectify issues and track progress diligently. For example, the situation of The Mindful Collective demonstrates how prompt corrective measures, such as isolating nonconforming items, changed their control strategy and facilitated growth on Amazon, resulting in a 25% rise in favorable customer feedback. Insufficient corrective and preventive action procedures have consistently ranked among the most frequent FDA inspectional observations in the medical device industry since fiscal year 2010, underscoring the need for robust action plans.
-
Regular evaluations of your Quality Management System (QMS) are essential to ensure its continued effectiveness and adherence to ISO 13485 auditing standards. This practice not only helps identify areas for improvement but also solidifies a company’s commitment to maintaining high-quality standards. For instance, OpsNinja's thorough inspections have improved control for brands such as Hash Stash, illustrating how systematic QMS updates can result in a 30% decrease in product returns and enhanced customer satisfaction ratings.
Conduct Regular Training: Ongoing training and refresher courses for staff are critical in keeping everyone informed about the latest requirements and implications of ISO 13485 auditing. This ongoing learning strategy guarantees that your team is prepared to maintain standards of excellence and regulation efficiently. Organizations that emphasize employee education, like those highlighted in our case studies, have reported a 40% rise in management efficiency, illustrating the tangible advantages of training programs.
Promote a Culture of Excellence: Nurturing an organizational environment that emphasizes high standards and adherence is essential. Encourage employees to report issues proactively and suggest improvements. A culture of quality can lead to significant enhancements in overall adherence rates and operational efficiency, as highlighted by Maurice Mann's experience before and after partnering with OpsNinja, where he improved his Amazon star ratings from 3.5 to 4.7, recovering $1 million in revenue.
Plan for Future Reviews: Preparation for upcoming evaluations should start as soon as the current one concludes. By establishing a continuous readiness mindset, organizations can facilitate smoother audits and reinforce their overall compliance framework. This proactive approach not only mitigates risks but also demonstrates a commitment to quality management.
- Illustrate with Case Studies: For instance, the Design and Development Transfer process exemplifies a continuous effort to prepare a medical device for manufacturing, culminating in a final review once development is complete and regulatory permissions are obtained. This ensures that all aspects of the development project are ready for transition to manufacturing. Furthermore, insights from Neil Ayton concerning managing diverse suppliers and establishing quality control processes for his e-commerce brands, including Caddent Golf and Karma Heart, underscore the significance of supplier management in enhancing quality.
By implementing these strategies, companies can significantly improve their corrective action processes and ensure compliance through ISO 13485 auditing, ultimately benefiting their operational integrity and reputation in the market. Additionally, it is crucial to capture and document all product requirements during the design and development phase, as highlighted by the quote: 'Design and development inputs are where you capture and document all of the product requirements for the device being developed.
Conclusion
Adhering to ISO 13485 is essential for organizations within the medical device industry, as it not only fulfills regulatory obligations but also reinforces a commitment to quality and patient safety. The article has highlighted the significance of effective audit preparation, emphasizing the need for:
- A thorough gap analysis
- Meticulous documentation to ensure compliance
Organizations must prioritize:
- Training their teams
- Conducting pre-audits
- Maintaining consistent processes to avoid common pitfalls that could jeopardize their quality management systems
Furthermore, the critical role of documentation has been underscored as a foundational element in successful ISO 13485 audits. From quality manuals to records of training and process validations, maintaining accurate and comprehensive documentation ensures transparency and accountability throughout the organization. By embracing a culture of continuous improvement and actively addressing nonconformities, organizations can not only enhance their compliance but also drive operational excellence.
In conclusion, the journey towards ISO 13485 compliance demands a proactive approach that encompasses preparation, training, and documentation. By mastering these principles, organizations can not only meet regulatory expectations but also cultivate a reputation for quality and reliability in the medical device sector. Ultimately, those who commit to these practices will not only safeguard their operations but also contribute positively to patient outcomes, underscoring the vital role of quality management in healthcare.