What Are the Basic Issues of Quality Control Inspection? A Comprehensive Overview
Discover what are the basic issues of quality control inspection and their implications for product quality.
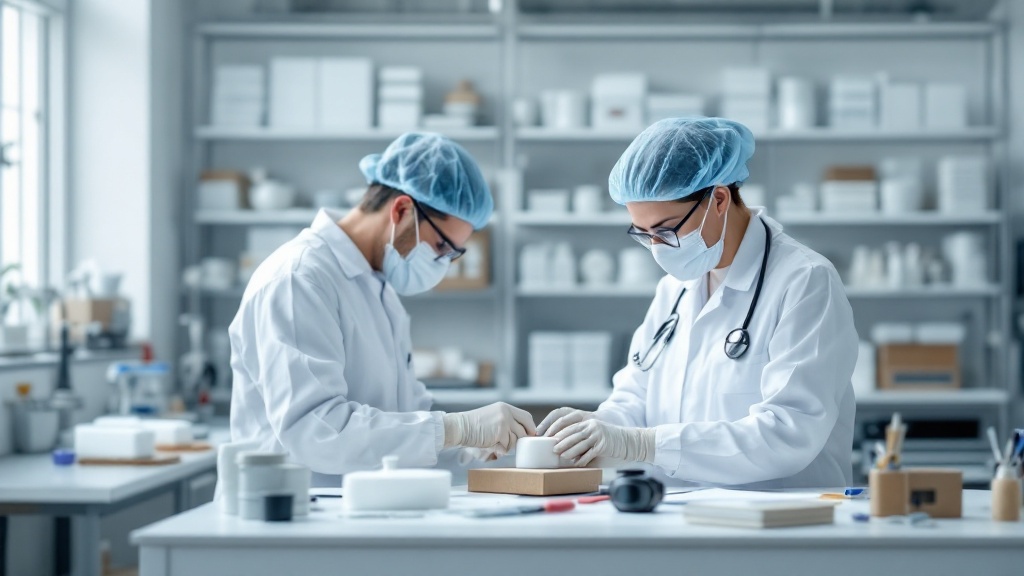
Key Highlights:
- Quality assurance (QA) ensures products meet standards, while quality control (QC) identifies and resolves issues in completed items.
- OpsNinja's inspections helped Amazon seller Maurice Mann improve his ratings from 3.5 to 4.7 stars, recovering $1 million in revenue.
- Quality control inspections can be categorized into three types: incoming checks, in-process assessments, and final reviews.
- Efficient incoming evaluations can reduce defects by up to 30%, highlighting their importance in maintaining product quality.
- Compliance with industry standards is crucial, with OpsNinja aiding brands in meeting regulations and minimizing risks.
- Challenges in QC include globalization, regulatory changes, and the need for human involvement in assessments.
- Effective QC inspections lead to improved product quality, reduced return rates, and enhanced customer satisfaction.
- OpsNinja offers customized inspection services that adapt to specific product needs, ensuring cost-effectiveness and quality.
Introduction
In the competitive landscape of modern manufacturing, maintaining high-quality standards is not just a goal but a necessity. Quality control (QC) serves as a vital mechanism that ensures products consistently meet established specifications, safeguarding both brand reputation and customer satisfaction.
Companies like OpsNinja exemplify the transformative power of tailored inspection services, helping businesses navigate the complexities of quality management. From enhancing product ratings to recovering significant revenue, effective QC practices are essential for organizations striving to thrive in a dynamic marketplace.
As industries evolve and consumer expectations rise, understanding the nuances of quality control and its various methodologies becomes increasingly critical for success. This article delves into the key concepts, challenges, and benefits associated with quality control inspections, providing insights that can empower brands to optimize their quality assurance efforts.
Understanding Quality Control: Definitions and Key Concepts
Quality assurance (QA) is a vital systematic procedure focused on making certain that items consistently satisfy designated standards, and OpsNinja demonstrates this with its customized inspection services. This multifaceted method includes a variety of activities aimed at monitoring and assessing the standard of items to address what are the basic issues of quality control inspection throughout the manufacturing process. Unlike quality assurance (QA), which focuses on defect prevention, oversight functions reactively by recognizing and resolving issues found in completed items.
For instance, OpsNinja's inspections assisted Amazon seller Maurice Mann elevate his ratings from 3.5 to 4.7 stars, ultimately recovering $1 million in revenue. Similarly, The Mindful Collective transformed their approach to control with OpsNinja’s tailored checklist support, allowing them to scale effectively on Amazon. OpsNinja creates its customized checklists by closely working with clients to comprehend the distinct features of their offerings, ensuring that evaluations are pertinent and efficient.
This tailored approach not only improves product standards but also boosts operational efficiency. Comprehending what are the basic issues of quality control inspection is essential for overseeing standards within any organization. Recent advancements in standards oversight highlight its importance; businesses that adopt strong management practices experience an impressive 40% decrease in customer grievances, as per the American Society for Quality (ASQ).
This statistic not only highlights the efficacy of QC but also reinforces its critical role in addressing what are the basic issues of quality control inspection to enhance customer satisfaction through minimized defects and errors. Advanced tracking systems play a crucial role in this process, enabling efficient coordination between departments to ensure timely completion and adherence to excellence standards. Additionally, software solutions are progressively being employed across sectors to maintain consistent excellence standards, showcasing how technology is impacting assurance practices.
The focus on tailored standards assessments, as demonstrated by OpsNinja's method, enables D2C brands to improve their oversight efforts and greatly boost operational efficiency. To learn more about how OpsNinja can assist your brand in enhancing quality management and driving revenue recovery, contact us today.
Types of Quality Control Inspections: Methods and Applications
Quality control evaluations are essential in ensuring that products meet the necessary standards, addressing what are the basic issues of quality control inspection throughout the manufacturing process. These evaluations can be categorized into three main types:
- Incoming checks
- In-process assessments
- Final reviews
Incoming assessments evaluate raw materials prior to their entry into the production line, ensuring all components conform to specified performance standards.
This essential step is vital; research indicates that efficient incoming evaluations can decrease flaws by as much as 30%, highlighting their significance in preserving item standards. In-process evaluations take place at multiple production phases, playing a crucial role in detecting flaws early, enabling prompt adjustments that can avert expensive rework or item failure. Ongoing monitoring and enhancement of control, as highlighted by Graham Immerman from Machine Metrics, are crucial for upholding high standards in production.
Final assessments review the completed item prior to delivery, verifying that it satisfies all quality standards. OpsNinja empowers D2C brands, such as Hash Stash, by optimizing these verification processes, enabling them to scale operations effectively while safeguarding their reputation. Each evaluation technique is important for identifying what are the basic issues of quality control inspection, which are essential for maintaining item integrity throughout the production lifecycle.
Additionally, the recent case studies demonstrate how OpsNinja's evaluations have assisted brands in regaining substantial revenue, including Maurice Mann’s Amazon store, which improved item ratings from 3.5 to 4.7 stars, recouping $1 million in revenue. Furthermore, Hash Stash encountered difficulties in upholding consistent product standards as they expanded, which OpsNinja resolved through its thorough evaluation services and simple booking system, enabling them to swiftly arrange assessments and guarantee excellence without interruption. As we enter 2024, comprehending these evaluation types remains essential for D2C brands striving to maintain quality in a progressively competitive market, and OpsNinja establishes itself as a reliable partner in this effort.
The Role of Quality Control Inspections in Compliance and Standards
To ensure compliance with industry standards and regulations, including ISO certifications and safety guidelines, it is essential to address what are the basic issues of quality control inspection during quality assurance evaluations. They play a crucial role in helping organizations identify what are the basic issues of quality control inspection before they escalate, minimizing the risk of costly penalties and reputational damage. In the electronics industry, for example, adherence to stringent safety standards is paramount.
Quality assessments confirm that products satisfy the standards related to what are the basic issues of quality control inspection, safeguarding both producers and consumers equally. OpsNinja's dedicated support team improves customer experience in supply chain management by offering impartial standards assessment during evaluations, a commitment that is crucial for D2C brands. This emphasis on excellence is underscored by recent findings, such as Beazley’s report revealing that:
- 67% of global executives believe that ESG regulation is too complex
- 70% want more guidance from regulators
Moreover, with 40% of supply chain experts emphasizing risk management and resilience, understanding what are the basic issues of quality control inspection is essential in reducing risks. For instance, OpsNinja's inspections have assisted Amazon seller Maurice Mann in recovering $1 million in revenue by improving ratings from 3.5 to 4.7 stars, showcasing how effective inspections can enhance brand protection and drive revenue recovery. Similarly, brands like Caddent Golf and Karma Heart have benefited from OpsNinja's comprehensive control processes that tackle what are the basic issues of quality control inspection, ensuring their products consistently meet market expectations and regulatory standards.
Recent initiatives, such as the New Inspection Protocol Project (NIPP) by the CDER, aim to address issues related to drug shortages, demonstrating the industry's commitment to improving management practices. Furthermore, the recent Producer Price Index (PPI) changes, which indicated a 0.4% increase in final demand, reflect inflationary pressures that can affect compliance and management practices across industries. Therefore, OpsNinja's assurance services go beyond evaluations to encompass supplier management and process enhancement, rendering them essential for D2C brand owners aiming to grow and thrive.
Challenges in Quality Control Inspections: Navigating Complexities
In the context of quality assurance evaluations, it is essential to understand what are the basic issues of quality control inspection, including various obstacles related to globalization, regulatory changes, and human factors. As businesses grow into global markets, they face a complex array of regulatory conditions that complicate assurance processes. A significant case study demonstrates how OpsNinja changed The Mindful Collective's method to ensure standards, allowing them to succeed on Amazon by applying efficient inspections.
Furthermore, entrepreneur Neil Ayton discusses how OpsNinja's platform assisted him in managing various suppliers and setting up control processes for his e-commerce brands, including Caddent Golf and Karma Heart. The World Quality Report recommends that teams maintain QA budgets at 25% by enhancing in-house capabilities, automating where possible, and utilizing the right testing tools. This emphasizes the need for adaptability amidst evolving regulations and increased release pressures.
In 2024, these challenges will likely intensify, with over 52% of IT teams attributing rising QA budgets to the frequency of releases. Human elements also significantly influence the effectiveness of assessments, where staff training and involvement are vital for ensuring consistency. For example, Maurice Mann's experience from 3.5 to 4.7 stars on his Amazon account demonstrates how OpsNinja's inspections aided in recovering $1 million in revenue by guaranteeing item excellence.
Furthermore, OpsNinja employs advanced technologies, including blockchain, to enhance transparency and security in supply chain management, addressing issues such as mislabeled items and missing units. QC executives often face pressure to reduce costs while upholding high standards, leading to outsourcing and automation. To address what are the basic issues of quality control inspection, QC teams need to implement robust monitoring systems for both human and machine processes, balancing cost and standards while leveraging advanced technologies for real-time reporting.
To tackle these complex challenges, organizations must adopt a forward-thinking strategy and dedicate themselves to ongoing enhancement in their management practices, especially as new technologies improve efficiency and item excellence in the changing environment of oversight.
Benefits of Effective Quality Control Inspections: Enhancing Quality and Efficiency
Establishing efficient standards assessments helps to clarify what are the basic issues of quality control inspection, providing numerous benefits such as improvements in item excellence, significant cost savings, and heightened customer satisfaction. OpsNinja's mission to transform retail assurance for sustainable consumer goods is clear in their customized inspection services, which safeguard brands from manufacturing problems and enhance their reputation. D2C brands that emphasize control often experience notably lower return rates due to defects, translating to significant savings in production and logistics.
Customers have praised OpsNinja's services, with one stating, 'Thanks to OpsNinja, we have drastically reduced our return rates and improved our brand's reputation.' Furthermore, OpsNinja offers customized pricing solutions designed to align with specific product ranges and manufacturing needs, ensuring peace of mind for brand owners. For instance, our pricing can adjust according to the number of inspections needed and particular regional manufacturing obstacles, enabling brands to uphold competitive rates while guaranteeing excellence.
As Forrester predicts, software testers utilizing generative AI technologies can achieve a 15% productivity gain, illustrating the potential for enhanced efficiency in control processes. This corresponds with the findings from the case study titled 'Productivity Gains from Generative AI,' which demonstrates how incorporating such technologies streamlines testing and improves overall output. Furthermore, recent statistics suggest a direct connection between strict assurance processes and heightened customer satisfaction levels, emphasizing the financial advantages of these practices.
As Dayana Mayfield, a QA engineer turned technology writer, notes, 'Shockingly, Forrester found that QA is not a priority in mobile development for the majority of teams,' revealing a critical area for improvement in the industry. By consistently delivering high-quality products, companies can strengthen customer loyalty and develop a robust market reputation. By investing in efficient standards checks, organizations can address what are the basic issues of quality control inspection, cultivate a culture of excellence, and drive long-term success, positioning themselves advantageously in an increasingly competitive environment.
As we near 2024, the focus on excellence management will only increase, with companies prepared to benefit from these careful practices. Don’t wait—partner with OpsNinja today to elevate your quality control processes and ensure your brand stands out in the market.
Conclusion
Quality control inspections are indispensable for businesses aiming to thrive in today's competitive manufacturing landscape. By understanding the various types of inspections—incoming, in-process, and final—organizations can implement comprehensive strategies that significantly enhance product quality while minimizing defects. OpsNinja exemplifies how tailored inspection services can transform quality management, as demonstrated by success stories from brands like Maurice Mann and The Mindful Collective.
Moreover, the importance of compliance with industry standards cannot be overstated. Quality control inspections not only ensure adherence to regulations but also protect brands from potential risks and penalties. As illustrated by the challenges faced in global markets, organizations must navigate complex regulatory environments and human factors effectively. The proactive measures taken by companies like OpsNinja showcase the critical role of quality inspections in maintaining operational integrity and consumer trust.
Ultimately, the benefits of effective quality control inspections extend beyond mere compliance; they drive substantial cost savings and foster customer satisfaction. By investing in robust quality management practices, organizations can enhance their reputation and reduce return rates, leading to improved financial outcomes. As the manufacturing landscape evolves, prioritizing quality control will be essential for sustained success. Embracing these practices not only empowers brands to meet and exceed consumer expectations but also positions them advantageously for future growth.
Discover how OpsNinja can elevate your quality management—schedule a tailored inspection today!