What Are Production Monitoring Systems? A Comprehensive Overview
Discover the essentials of production monitoring systems and their impact on manufacturing efficiency.
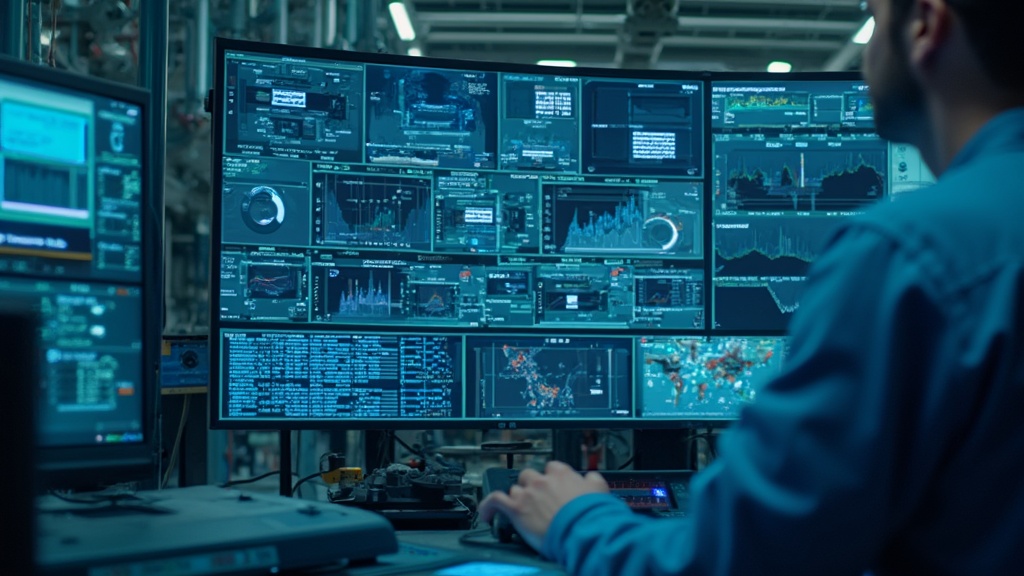
Key Highlights:
- Production monitoring systems integrate various technologies to oversee and control manufacturing processes, improving operational oversight.
- Real-time data from these systems helps manufacturers quickly identify and resolve issues, enhancing product quality and resource allocation.
- Case studies, such as those from OpsNinja, demonstrate significant improvements in quality control for D2C brands, leading to increased revenue.
- Key components of effective production monitoring systems include advanced information gathering tools, real-time dashboards, and analytics software.
- Overall Equipment Effectiveness (OEE) is a crucial metric for assessing operational efficiency, combining availability, performance, and quality.
- A structured approach to implementing monitoring frameworks is essential, with clear objectives and integrated technology being critical for success.
- Effective production monitoring can lead to cost savings of up to 20% by 2024 through improved oversight and reduced downtime.
- Future trends in production monitoring include the integration of IoT and AI for enhanced data collection, predictive maintenance, and operational efficiency.
- Adopting innovative technologies will provide manufacturers with a competitive edge in a rapidly evolving market.
Introduction
In the dynamic landscape of modern manufacturing, production monitoring systems have emerged as essential tools for enhancing operational efficiency and ensuring product quality. These sophisticated frameworks integrate cutting-edge technologies to provide real-time insights into various production parameters, enabling manufacturers to swiftly identify and rectify issues that may hinder performance.
As organizations increasingly pivot towards data-driven decision-making, the importance of effective monitoring cannot be overstated; it not only optimizes resource allocation but also plays a crucial role in maintaining customer satisfaction.
With compelling case studies illustrating significant improvements in quality control and revenue recovery, the adoption of these systems is becoming a strategic imperative for businesses aiming to thrive in a competitive marketplace.
As manufacturing processes grow more complex, understanding the components, implementation steps, and future trends of production monitoring systems is vital for any organization seeking to enhance its operational capabilities and drive sustainable growth.
Understanding Production Monitoring Systems: Definition and Importance
Production monitoring systems serve as extensive frameworks that integrate diverse technologies to supervise and control manufacturing processes in industrial settings. These setups serve as production monitoring systems that meticulously monitor a range of parameters, including machine performance, production rates, and quality metrics, providing manufacturers with an invaluable tool for operational oversight. The importance of executing these frameworks, particularly production monitoring systems, is highlighted by their ability to provide real-time data, which enables manufacturers to swiftly recognize and resolve problems, thus improving product quality and refining resource distribution.
For D2C brands, effective quality control is paramount; as demonstrated by OpsNinja’s case studies, companies like Maurice Mann's Amazon store saw a remarkable increase in their star ratings from 3.5 to 4.7, recovering $1 million in revenue through enhanced inspections. OpsNinja’s inspections feature a rigorous process that includes:
- Thorough product evaluations
- Ensuring compliance with quality standards
- Addressing challenges such as mislabeled products and UPC code verification
Similarly, The Mindful Collective transformed their approach to quality control, facilitating significant growth on Amazon by implementing OpsNinja’s systematic inspection processes.
Considering the contemporary manufacturing environment, which encounters growing intricacy and a transition from conventional management approaches like whiteboards and spreadsheets, the implementation of production monitoring systems is essential. Toyota's innovative methods in overseeing operations are exemplary, demonstrating how effective integration can result in substantial operational enhancements. By utilizing production monitoring systems, companies not only strengthen their operational efficiency but also improve customer satisfaction and minimize returns.
Furthermore, supporting clients through denied warranty claims with empathy and clear explanations reinforces the human element in this technological evolution. Integrating insights from eCommerce analytics, D2C brands can further enhance their supply chain management and quality control, ensuring they meet customer expectations and maintain competitive advantage.
Key Components and Indicators of Production Monitoring Systems
The basis of efficient production monitoring systems for output relies on several essential elements, including:
- Sophisticated information gathering tools
- Interactive real-time dashboards
- Strong analytics software
These elements work collaboratively to provide a clear picture of manufacturing performance. Critical indicators such as Overall Equipment Effectiveness (OEE), production yield, and defect rates play vital roles in this assessment.
OEE, in particular, is a powerful metric that integrates availability, performance, and quality, offering a holistic view of operational efficiency. Recent trends emphasize the growing reliance on OEE metrics as manufacturers strive for excellence and competitive pricing. Furthermore, manufacturing reporting software can streamline reporting processes by automatically processing information and consolidating it into a central location, providing instant updates that enhance information management.
A case study titled 'Streamline Reporting with Manufacturing Reporting Software' illustrates this, showing how such software aids companies in managing large sets of information efficiently, leading to prompt performance insights and alerts for underperforming KPIs. By focusing on these components and indicators, organizations can leverage production monitoring systems to obtain actionable insights that not only improve reporting processes but also encourage continuous enhancement in their operational environments. As emphasized by industry specialist Madis Kuuse, 'Utilizing these tools efficiently is crucial in maneuvering through the intricacies of contemporary manufacturing,' especially considering the continual developments in reporting software that enhance information management and offer real-time updates.
Implementing Production Monitoring: Steps for Effective Data Collection and Analysis
Implementing a monitoring framework requires a structured approach to ensure alignment with overarching business objectives. Initially, it is essential to define precise objectives and key performance indicators (KPIs) that reflect the goals of your organization. Following this, selecting the appropriate technology and tools for information collection is paramount.
The selected tools must integrate seamlessly with existing infrastructure to avoid disruption. As Dr. Ori Cohen aptly states,
As you have seen, picking one tool requires thorough analysis
this highlights the need for careful consideration in tool selection. After the framework is established, create strong protocols for analysis, focusing on detecting trends and anomalies that could affect efficiency in manufacturing.
Regular review of this information is crucial for informed decision-making and proactive adjustments to production monitoring systems. Logging plays a critical role in this context, as it is essential for troubleshooting, auditing, and compliance in machine learning applications, ensuring that all data management aspects within production monitoring systems are thoroughly addressed. Training staff in the use of these systems can significantly enhance effectiveness, ensuring that everyone is equipped to leverage the data for operational improvements. A noteworthy example comes from H&T Waterbury, which achieved a remarkable 71% reduction in downtime through effective oversight practices.
Additionally, the idea of 'start simple, think big, move fast' motivates manufacturers to begin with manageable implementations, gradually scaling up as they enhance their tracking processes. This philosophy can be applied directly to the steps for implementation, emphasizing the importance of starting with foundational elements before expanding. Ultimately, maintaining a focus on both functional and operational oversight is essential, as it ensures that the entire ecosystem supporting output is optimized.
Effective oversight encompasses both aspects, preserving the value and performance of deployed models throughout their lifecycle.
Benefits of Production Monitoring Systems: Enhancing Efficiency and Reducing Costs
Oversight frameworks offer numerous benefits that greatly improve operational efficiency while concurrently minimizing waste and manufacturing expenses. By utilizing production monitoring systems for real-time oversight, organizations can quickly pinpoint bottlenecks within the manufacturing line, enabling prompt corrective actions that reduce downtime and enhance throughput. Recent statistics indicate that companies utilizing production monitoring systems can achieve cost savings of up to 20% by 2024, demonstrating a growing trend in operational savings linked to improved oversight practices.
Furthermore, robust quality control mechanisms foster lower defect rates, translating into significant savings on materials and labor. Companies that utilize the strength of overseeing their outputs frequently discover they are endowed with enhanced decision-making abilities, as data-informed insights enable them to adjust quickly to market changes and shifting consumer needs. This coincides with recent specialist views claiming that effective oversight provided by production monitoring systems is a vital element in reducing manufacturing expenses and enhancing overall efficiency.
Additionally, OpsNinja's commitment to preventing manufacturing issues through reliable inspections protects your brand from negative reviews and poor customer experiences, thus safeguarding your brand integrity. With budget-friendly inspection strategies, such as the 'Budget-Friendly Plan' and the 'Inspection Budgeting & ROI guide,' D2C brands can maximize ROI while ensuring quality. The 'Budget-Friendly Plan' allows brands to conduct inspections on every batch at minimal cost, ensuring consistent quality control.
Furthermore, basic digital self-check alternatives provide a cost-effective way for brands to implement quality assurance measures internally, enabling them to maintain high standards without significant investment. As one expert remarked, 'Resolve volunteer conflicts effectively by listening actively, finding common ground, and setting clear expectations to restore harmony,' highlighting the significance of communication in successfully executing these processes. Grasping market influences and trends will be crucial for navigating the future environment of oversight.
Future Trends in Production Monitoring: Embracing Technology and Innovation
The future of manufacturing oversight is set for change, significantly shaped by technological progress. With nearly 30% of industrial product manufacturers planning to invest in XR technologies over the next few years, the integration of the Internet of Things (IoT) is paramount. This technology facilitates enhanced connectivity between machines, significantly improving the scope and accuracy of data collection and analysis.
Furthermore, artificial intelligence (AI) is emerging as a pivotal force in predictive maintenance, allowing manufacturers to foresee equipment failures before they disrupt operations. Gartner highlights that by 2030, AI-based management of employee skills will be essential for meeting business needs. As these technologies keep advancing, businesses that adopt creative methods for overseeing their operations will discover a competitive edge in a progressively changing market.
Insights from Deloitte's 2025 Manufacturing Industry Outlook further underscore the significance of smart operations and talent management as manufacturers adapt to these changes. Real-world examples of IoT integration, such as the implementation of smart sensors in automotive manufacturing, showcase how data-driven decision-making enhances operational efficiency. Furthermore, the case study on clean technology manufacturing trends demonstrates how automakers are adapting their strategies in response to market uncertainties, highlighting the need for flexibility in manufacturing processes.
Moreover, customer reviews play a significant role in building vendor lists, necessitating a review-centric marketing approach that influences production monitoring systems and the selection of vendors. Together, these elements provide a robust framework for future growth and agility in manufacturing.
Conclusion
The integration of production monitoring systems into modern manufacturing is not merely beneficial; it is essential for organizations aiming to enhance operational efficiency and ensure product quality. As outlined, these systems provide real-time insights into various production parameters, allowing manufacturers to swiftly identify and address potential issues. The compelling case studies presented highlight the tangible benefits realized by companies that have embraced these technologies, such as significant improvements in quality control and revenue recovery.
Key components, including advanced data collection tools and critical performance indicators like Overall Equipment Effectiveness (OEE), serve as the backbone of effective monitoring systems. Implementing these systems requires a structured approach, focusing on clear objectives and robust data analysis protocols. Organizations that invest in training their staff and adopting a philosophy of starting simple and scaling up will find themselves better positioned to navigate the complexities of modern manufacturing.
Looking ahead, the future of production monitoring systems is bright, driven by advancements in IoT and AI technologies. These innovations promise to enhance connectivity and predictive capabilities, enabling manufacturers to stay ahead of equipment maintenance and operational challenges. By embracing these trends, businesses can not only optimize their production processes but also maintain a competitive advantage in an ever-evolving marketplace.
In conclusion, the strategic adoption of production monitoring systems is indispensable for manufacturers seeking to thrive. By prioritizing data-driven decision-making and leveraging advanced technologies, organizations can achieve greater efficiency, reduce costs, and ultimately deliver superior products that meet customer expectations.