Understanding Quality vs. Compliance: An In-Depth Tutorial for Professionals
Explore the critical differences and relationship between quality versus compliance in professional settings.
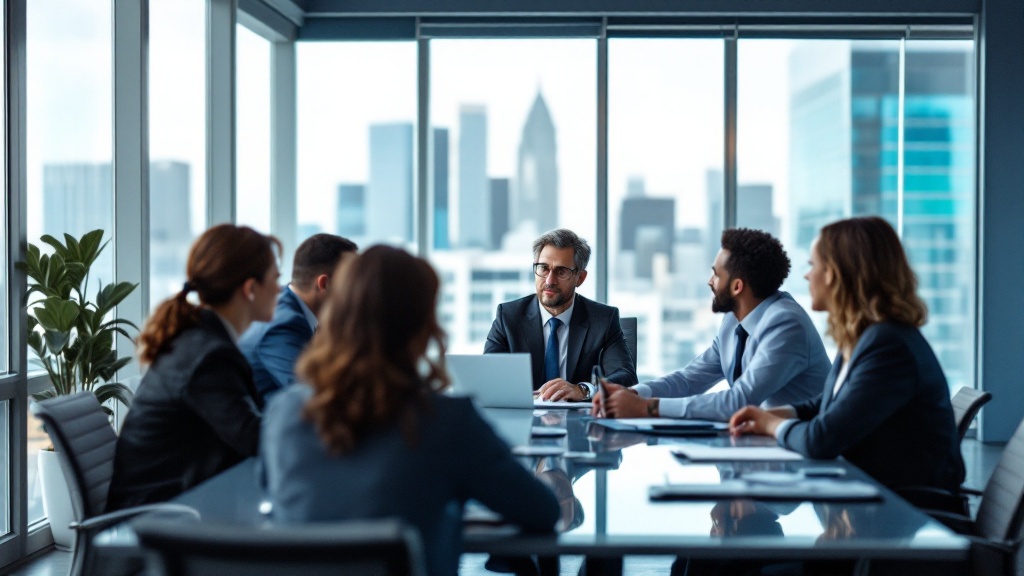
Key Highlights:
- Quality refers to the fulfillment of specified requirements and customer expectations, while compliance involves adherence to regulations and standards.
- Understanding the difference between quality and compliance is essential for safeguarding consumer safety and satisfaction.
- Direct-to-consumer (D2C) brands must implement effective assurance measures to enhance customer satisfaction and mitigate negative reviews.
- Acceptable Quality Level (AQL) metrics guide the evaluation of product batches, helping brands maintain quality standards.
- Training employees on Quality Management System (QMS) standards is crucial for adherence and improved management.
- AI and automation are believed to significantly impact risk management, enhancing data breach responses and compliance outcomes.
- Operational excellence requires a risk-oriented strategy that values both quality and compliance, utilizing methodologies like Lean and Six Sigma.
- Regular audits and inspections are vital for identifying gaps in quality and compliance with regulatory guidelines.
- The consequences of neglecting quality or compliance can include recalls, legal penalties, and damage to brand reputation.
- D2C brands can leverage inspection solutions to improve quality control and protect their reputation while driving revenue recovery.
Introduction
In an increasingly competitive marketplace, the importance of quality and compliance cannot be overstated. As organizations strive to meet customer expectations and adhere to stringent regulations, understanding the nuances of these two concepts becomes paramount.
Quality is not merely about meeting standards; it is about delivering value through performance, reliability, and durability. Compliance, on the other hand, ensures that these quality attributes align with legal and industry mandates, safeguarding consumer safety and satisfaction.
This article delves into the intricate relationship between quality and compliance, exploring:
- Best practices
- The risks of neglect
- The strategic approaches organizations can adopt to achieve operational excellence
By integrating effective quality management systems and compliance measures, businesses can enhance their reputation, drive customer loyalty, and ultimately secure their position in the market.
Defining Quality and Compliance: Key Concepts for Professionals
Quality is characterized by the extent to which a good or service fulfills specified requirements, customer expectations, and established industry criteria. It encompasses key attributes such as performance, reliability, and durability, which collectively contribute to the overall value of an item. Compliance, in contrast, pertains to the adherence to specific regulations, laws, and standards set forth by governing bodies or industry organizations.
Grasping the difference between these two ideas is crucial; while excellence emphasizes the inherent attributes of products and services, understanding quality versus compliance ensures that these attributes align with mandated requirements, thereby safeguarding consumer safety and satisfaction. For direct-to-consumer (D2C) brands, implementing effective assurance measures is crucial for mitigating negative reviews and enhancing customer satisfaction. The competitive nature of the market for assurance solutions necessitates that D2C brands distinguish themselves through robust management practices.
An essential part of this method is comprehending AQL figures; these metrics signify the acceptable standards for batches and direct the sampling procedure during evaluations. For example, if a D2C brand sets an AQL of 1.5%, it means that in a batch of 100 products, no more than 1 or 2 defects are acceptable. By utilizing AQL guidelines, brands can statistically guarantee excellence, minimizing the chance of customer grievances and returns.
As mentioned in industry conversations, the average expenditure per employee on learning and development rose in 2021 to nearly $1300 per worker, emphasizing the significance of training employees on Quality Management System (QMS) standards, such as ISO 9001, for adherence and enhanced management. Furthermore, the emergence of industry-specific QMS solutions has led to intense competition within each solution type, making the market highly competitive. This competitive nature highlights the importance for organizations to prioritize quality versus compliance, as failing to do so can greatly affect consumer trust and satisfaction in today’s market.
Additionally, a majority of risk management leaders believe that AI will significantly impact their functions in the next one to five years, with organizations using AI and automation extensively reporting significantly lower data breach costs and faster breach identification and containment. This demonstrates how incorporating AI into regulatory functions can improve results and further emphasize the significance of following excellence standards.
Balancing Quality and Compliance: Strategies for Operational Excellence
Attaining operational excellence necessitates organizations to embrace a risk-oriented strategy that equally values quality versus compliance. Implementing continuous improvement methodologies such as Lean and Six Sigma is essential for identifying inefficiencies that could compromise quality versus compliance. Significantly, a process functioning at Six Sigma standards generates only 3.4 defects per million opportunities, highlighting the potential for excellence in operational processes.
For instance, OpsNinja's inspections assisted Amazon seller Maurice Mann in recovering $1 million in revenue by enhancing his product ratings from 3.5 to 4.7 stars, demonstrating the direct influence of control on business success. In contrast, The Mindful Collective initially hesitated to implement inspections but ultimately transformed their approach to control through OpsNinja, enabling them to scale effectively on Amazon.
Furthermore, understanding the Process Capability Index (CPK) is vital for assessing how well a process can produce output within specified limits, which is crucial for maintaining assurance. Frequent training sessions for staff on standards and regulatory requirements promote a culture of responsibility and ongoing enhancement. Institutions like SixSigma.us offer versatile online certification options, including Live Virtual and Self-Paced training. As John Doe, an instructor at SixSigma.us, states, 'This versatility not only enhances career prospects but also allows organizations to benefit from cross-industry insights and best practices.'
Additionally, the University of Massachusetts, Amherst offers a Post Graduate Program in Lean Six Sigma, combining hands-on projects with training in Six Sigma methodologies, which provides further educational opportunities in this critical field. A pertinent example is the case study of Children’s Health Ireland, which utilized Lean Six Sigma to enhance workplace safety during the Covid-19 pandemic, reducing the number of staff exposed to infected patients from 13 to one. Moreover, utilizing advanced technology, such as Quality Management Systems (QMS) and regulatory software, streamlines data collection and reporting processes, ultimately enabling more informed decision-making that balances quality versus compliance for sustained operational excellence.
Navigating Regulatory Requirements: The Role of Quality and Compliance
Navigating the regulatory environment is essential for D2C brand owners involved in development and assurance to effectively manage quality versus compliance. Regulatory organizations, such as the FDA, ISO, and OSHA, create essential guidelines that outline performance criteria, emphasizing the importance of quality versus compliance expectations. For example, ISO 8124 safety guidelines are employed by toy makers to evaluate aspects such as sharp points, lead content, and chemical hazards, demonstrating the direct influence of these regulations on safety.
A key metric in this realm is the Acceptable Level of Excellence (AQL) numbers, which guide the sampling process during assessments. These figures dictate the quantity of items to be examined and the acceptable degree of flaws, thereby ensuring that product excellence balances quality versus compliance while safeguarding your brand from adverse customer experiences. Detailed reporting, including comprehensive inspection reports with photos and instructions, plays a critical role in this process.
As Jubina Prabhakaran states, 'In this guide, you will learn how to develop Quality Assurance Guidelines,' emphasizing the importance of structured approaches in this field. It is imperative for professionals to remain updated on the evolving regulatory environment, particularly regarding the quality versus compliance issues highlighted by recent alerts concerning contaminated pediatric syrup medicines, which underscore the need for stringent manufacturing practices. This case emphasizes the urgency for Member States to enforce international guidelines to safeguard public health and ensure the quality and safety of medicines in circulation.
Regular audits, thorough inspection reports, and adherence evaluations are crucial for identifying any gaps in quality versus compliance with these guidelines. Collaborating with regulatory specialists or advisors can provide organizations with valuable insights to effectively navigate the complexities of legal frameworks, ensuring a balance between quality versus compliance in their processes. Resources for implementing the QAPP Standard, such as the One Pager and FAQs, can also be instrumental in guiding these efforts.
As we approach 2024, staying informed of the latest updates from the FDA, ISO, and OSHA regarding standards is not just advisable; it is essential for maintaining consumer trust and safeguarding public health.
Integrating Quality Management and Compliance: Best Practices for Success
Effectively merging standards management with regulations necessitates organizations to create a unified structure that aligns their performance goals with regulatory requirements. Start by carefully outlining current procedures and identifying areas where standards and regulations converge. This strategic approach not only clarifies responsibilities but also enhances collaboration across departments.
Creating cross-functional teams is vital; these groups promote communication between assurance and regulatory divisions, ensuring that everyone is aligned and informed. To facilitate effective data governance, it is crucial to explain policies to staff and prioritize key performance indicators (KPIs) that guide performance evaluations. Key roles such as a steering committee, a data owner, and a data steward should be established to distribute responsibilities among employees effectively.
Regular training sessions and workshops are essential for keeping all stakeholders informed about improvements in standards and regulations. Furthermore, setting specific goals and measurable metrics is essential for directing and evaluating the effectiveness of data improvement initiatives. Embracing technology solutions, particularly integrated software platforms, can significantly improve data visibility and simplify reporting, ultimately leading to more effective governance.
Moreover, performing routine audits and compliance evaluations guarantees alignment with set criteria, while non-destructive testing (NDT) methods can improve product excellence without jeopardizing integrity. Comprehending the Process Capability Index (CPK) enables organizations to assess their processes' capacity to generate output within defined limits, thus strengthening assurance efforts. As Gorkem Sevinc aptly noted, 'Their leadership helps to maintain high standards for data integrity throughout the organization.'
This leadership is essential in driving initiatives that enhance both quality versus compliance and adherence performance, ultimately leading to improved business outcomes.
The Risks of Neglecting Quality or Compliance: Understanding the Consequences
Ignoring assurance and compliance can result in severe consequences for businesses, including recalls, significant legal penalties, and irreversible damage to brand reputation. A significant example of this is the recent CPSC warning regarding Garberiel Lithium-Ion Battery Chargers, known to overheat and cause fires, potentially resulting in serious injuries or fatalities. The CPSC advised consumers to unplug and dispose of these chargers immediately—an urgent reminder that quality failures can endanger consumer safety and lead to costly recalls.
In 2023, Zuru LLC encountered a substantial challenge with 7.5 million units recalled, illustrating the scale of recalls and their implications for businesses. Statistics indicate that in 2023 alone, the CPSC imposed civil penalties amounting to $55.3 million in the U.S., highlighting the financial consequences of regulatory failures. Organizations must consider recall and contamination insurance as vital safeguards against the financial losses associated with product recalls.
According to D. Tighe, a research expert in consumer behavior, 'The recall is an effort to ensure public safety, limit ruination of the corporate image, and limit liability for corporate negligence, which can cause the responsible company significant legal costs.' This highlights the necessity for organizations to prioritize quality versus compliance in their operations. By leveraging OpsNinja's comprehensive inspection solutions and supplier management strategies, D2C brand owners can enhance quality control, protect their brands from negative reviews, and ultimately drive revenue recovery.
For instance, in a recent case study, OpsNinja helped a D2C brand reduce their return rate by 30% through tailored inspection processes. Additionally, OpsNinja's pricing is customized to meet the specific needs of D2C brands, offering competitive rates and scalable options that ensure brands maintain consumer trust and long-term viability. These customized solutions provide peace of mind against bad batches, ensuring that brands can focus on growth while safeguarding their reputation.
Conclusion
The relationship between quality and compliance is not just a matter of operational necessity; it is a fundamental aspect of maintaining consumer trust and ensuring business success. By understanding the key concepts of quality and compliance, organizations can better navigate the complexities of regulatory requirements and establish robust quality management systems. This article has explored the significance of implementing effective quality assurance practices, the importance of adhering to compliance mandates, and the risks associated with neglecting either aspect.
Strategically balancing quality and compliance through continuous improvement methodologies, employee training, and the use of advanced technologies can lead to operational excellence. The examples illustrated, such as successful interventions by OpsNinja and the application of Lean Six Sigma principles, demonstrate that organizations can achieve significant improvements in product quality and customer satisfaction. Furthermore, the case studies highlighted reinforce the idea that a proactive approach to quality management is essential for safeguarding against potential pitfalls, such as product recalls and legal repercussions.
Ultimately, integrating quality management and compliance is not just a best practice; it is a critical strategy for organizations aiming to thrive in today’s competitive marketplace. By prioritizing these elements, businesses can enhance their reputation, foster customer loyalty, and secure their position in the market, ensuring long-term success and sustainability. As the landscape continues to evolve, staying informed and adaptable will be key in navigating the challenges and opportunities that lie ahead.