Understanding INMETRO Brazil Certification: A Complete Tutorial for Medical Device Manufacturers
Explore the INMETRO Brazil certification process for medical devices and ensure compliance.
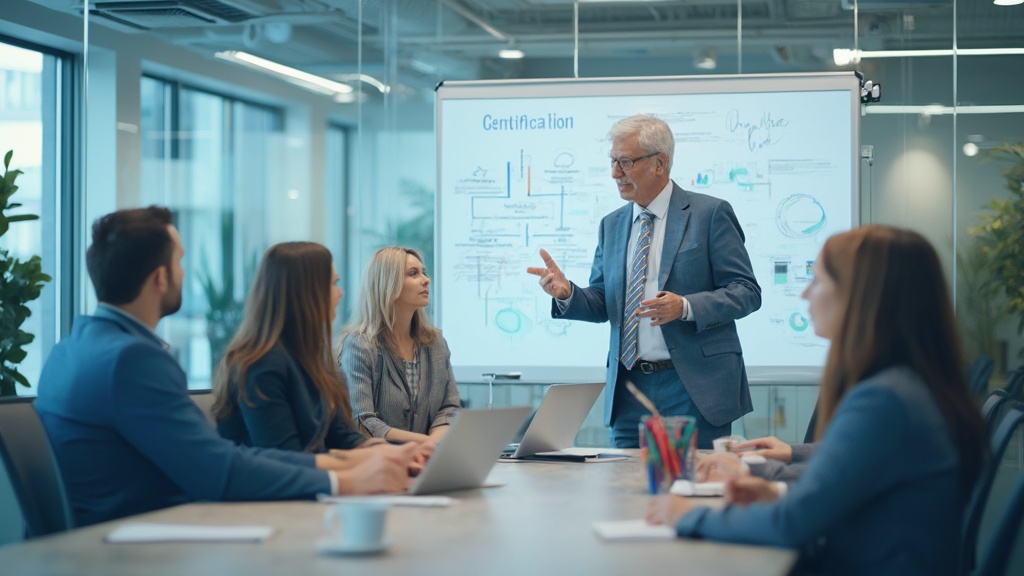
Introduction
Navigating the landscape of medical device certification in Brazil can be a complex endeavor, particularly with the stringent requirements set forth by INMETRO, the country's national institute for metrology, quality, and technology. As the regulatory authority, INMETRO plays a crucial role in ensuring that medical devices meet rigorous safety and quality standards before they can be marketed.
For manufacturers, securing INMETRO certification is not just a legal obligation; it is a vital step that enhances consumer trust and positions their products favorably in a competitive market.
This article delves into the intricacies of the INMETRO certification process, outlining essential steps for compliance, common challenges faced by manufacturers, and the significant benefits that come with achieving this certification.
By understanding the landscape and proactively addressing certification requirements, companies can effectively navigate the complexities of the Brazilian market while ensuring the highest standards of safety and quality in their medical devices.
Overview of INMETRO Certification for Medical Devices in Brazil
Inmetro Brazil, officially known as the Instituto Nacional de Metrologia, Qualidade e Tecnologia, acts as the foundation of regulatory supervision for medical equipment in Brazil. This national institute is pivotal in ensuring that all medical devices adhere to stringent safety and quality standards prior to entering the Brazilian market. For manufacturers, obtaining INMETRO approval is essential to verify compliance with national regulations, which is paramount for safeguarding public health.
The validation process is thorough, involving rigorous testing and evaluation of products to ensure they meet established criteria. According to recent updates, the complexity and duration of the authorization process can vary depending on the category, with Class III and IV categories requiring a B-GMP certificate that is valid for two years. The cost of obtaining a GMP certificate can be up to approximately EUR 25,000, highlighting the financial implications for manufacturers seeking certification.
As Margret Seidenfaden observes,
Authorizations issued for Class III and IV items are valid for 10 years,
indicating the long-term commitment to safety and quality in these higher-risk categories. Additionally, the documentation requirements for registering medical equipment in Brazil vary according to the classification, with higher classes necessitating more extensive documentation. Obtaining approval from INMETRO Brazil not only meets legal requirements but also boosts consumer confidence in the medical products available.
This validation process offers manufacturers a competitive advantage by highlighting their commitment to quality and safety, ultimately leading to improved health outcomes for the public.
Step-by-Step Guide to Achieving INMETRO Certification
-
Determine Product Classification: Begin by categorizing your medical instrument in accordance with Brazilian regulations. This classification is crucial as it dictates the specific requirements and testing protocols applicable to your product.
-
Select an Accredited Certifying Body: Choose an accredited certifying body recognized by INMETRO Brazil for the specific type of medical device you intend to certify. This selection is pivotal to navigating the certification landscape effectively.
-
Prepare Documentation: Compile all necessary documents, including detailed product specifications, management system (QMS) documentation, and previous test results. According to the regulatory agency, there are 386 important passages marked in their collection that highlight the depth of information available, emphasizing the importance of thorough documentation that aligns with their stringent standards.
-
Quality Management System (QMS) Compliance: Implement a robust quality management system that adheres to ISO 13485 standards, a prerequisite for local accreditation. This system should encompass every aspect related to the design, production, and post-market surveillance of your medical device.
-
Technical Evaluation and Testing: Submit your product for thorough technical evaluation, which includes performance testing, safety assessments, and comprehensive risk analysis. The chosen accreditation organization will perform these assessments according to established standards, ensuring your product's conformity. As noted by the relevant authority, their certification process differs from other product certifications in Brazil in several aspects, making it crucial to adhere to their specific guidelines.
-
Certification Issuance: Upon successful completion of all evaluations and compliance checks, INMETRO Brazil will issue a certificate of conformity. This critical document verifies that your medical device meets all regulatory requirements stipulated by Brazilian law.
-
Post-Certification Activities: To maintain compliance, regularly review and update your quality management system and conduct periodic audits. It is also essential to stay informed about any regulatory changes that may affect your status. For example, TÜV SÜD’s accreditation scope demonstrates practical application, as they are authorized to verify a wide range of products including medical devices under relevant standards.
By carefully adhering to these steps, manufacturers can successfully obtain approval, ensuring their medical devices are well-prepared for the Brazilian market.
Common Challenges in the INMETRO Certification Process
Manufacturers navigating the certification process encounter several significant challenges that can impede timely compliance and market entry. Key among these challenges are:
-
Complex Documentation Requirements: The extensive and detailed documentation required by the regulatory agency, including Inmetro Brazil standards, can be daunting, especially for those entering the Brazilian market for the first time. Establishing a dedicated team that can manage these requirements effectively is critical to ensure compliance and accuracy. Furthermore, incorporating customized standards checks from Movley can streamline this process by ensuring that documentation aligns with product-specific benchmarks.
-
Understanding Regulatory Changes: The regulatory landscape in Brazil is dynamic, with frequent changes that can complicate compliance efforts. To mitigate this risk, manufacturers should regularly consult the official announcements from Inmetro Brazil and engage with local experts who can provide timely insights into regulatory updates and implications. Proactive standards measures, such as Movley's on-site inspections, can also help manufacturers stay ahead of regulatory changes by identifying potential issues early.
-
Quality Management System Gaps: A common oversight among manufacturers is the failure to implement a comprehensive quality management system (QMS). Adhering to ISO 13485 standards is essential; a robust QMS not only facilitates compliance but also streamlines the certification process, minimizing potential delays. For instance, all medical device manufacturers must adhere to the resolutions RDC 16/2013, which outlines the B-GMP regulations established by ANVISA. By utilizing customized checklists from Movley's standards team, manufacturers can ensure their QMS meets the necessary standards.
-
Testing Delays: The technical evaluation phase is frequently hindered by delays, primarily because of backlogs at approval organizations. In 2019, ANVISA conducted 84 inspections, highlighting the demand on these bodies. To avoid setbacks, manufacturers should proactively submit their documentation and product samples well in advance, allowing ample time for review and evaluation. Applying Movley’s proactive inspections can also assist in avoiding issues that result in delays in the approval process.
As highlighted by LNE/G-MED North America, "Join LNE/G-MED North America in its Free webinar, 'The Role in the Brazilian Medical Device Registration Process' to discover more about navigating these challenges."
By acknowledging these obstacles and proactively tackling them with customized standards, manufacturers can greatly diminish the chances of facing typical setbacks, thus simplifying their accreditation process.
The Role of Post-Market Surveillance in INMETRO Certification
Post-market surveillance is a crucial component for maintaining certification, ensuring that medical devices consistently meet safety and performance standards after they enter the market. Manufacturers must adhere to several critical practices:
-
Conduct Regular Monitoring: It is imperative to continuously gather data on product performance and safety through user feedback and incident reports. According to reports from the Alternative Summary Reporting Program, the data collected from 1999 to April 2019 highlights the ongoing need for vigilance in monitoring adverse events, which is crucial for maintaining compliance with standards set by inmetro brazil. Participating in comprehensive supplier assessments and audits, as provided by Movley, can further guarantee that the sources of these products meet the required standards. For example, a customer remarked, "Movley’s inspections gave me the assurance I required to trust my suppliers and ensure product standards."
-
Implement Corrective Actions: In the event that issues are identified, manufacturers must be prepared to swiftly implement corrective actions to mitigate potential risks. This proactive approach is crucial in maintaining patient safety as a top priority. The prompt and detailed inspections provided by Movley can help identify these issues early, allowing for timely interventions. A case study demonstrates how a client was able to recover $1 million in revenue by addressing issues identified through Movley’s inspections.
-
Periodic Audits: Regular evaluations of the management system and production processes are necessary to ensure continued adherence to standards. These audits not only verify adherence to regulations but also facilitate the identification of areas for improvement. Morley's supplier audits significantly reduce risk while ensuring the quality and reliability of suppliers, enhancing overall operational efficiency and fostering long-term cooperation with partners.
-
Report Adverse Events: Manufacturers are required to report any adverse events or product failures to the relevant regulatory body. Understanding and adhering to reporting procedures is vital for healthcare professionals, as it allows for appropriate regulatory responses and bolsters consumer protection efforts. The FDA has actively encouraged healthcare professionals, patients, and caregivers to voluntarily report significant adverse events or product problems. This initiative, as demonstrated in the case study on Voluntary Medical Equipment Reporting, aims to gather more comprehensive data on safety and performance, highlighting the collaborative effort needed to enhance safety.
Engaging actively in post-market surveillance not only fulfills regulatory obligations but also significantly enhances a manufacturer’s reputation and trustworthiness in the marketplace. By prioritizing these practices and leveraging Movley’s expertise in supplier evaluation and inspections, brands can ensure they remain compliant while safeguarding their customers’ health.
Benefits of Achieving INMETRO Certification
Achieving INMETRO approval presents a multitude of advantages for medical device manufacturers, significantly influencing their operational success and market positioning:
- Market Access: Obtaining approval from Inmetro Brazil is a critical step for entering the Brazilian market, where compliance with regulations is often mandatory. This paves the way for a vast and expanding consumer base eager for excellent medical products.
- Enhanced Credibility: Approval from an official body serves as a strong endorsement, assuring consumers and healthcare professionals that your products comply with rigorous safety and quality standards. This fosters trust and enhances your brand’s reputation in a competitive landscape.
- Competitive Advantage: By obtaining the necessary validation, companies can effectively distinguish their products from those of rivals without this approval. This distinction positions certified products as safer and more reliable, appealing to discerning customers.
- Reduced Liability Risks: Adherence to regulations helps manufacturers mitigate legal risks associated with product failures or safety incidents. Non-compliance can result in fines, legal action, and even criminal charges, emphasizing the importance of certification.
- Enhanced Quality Management: The validation process promotes the adoption of robust quality management practices. As a result, producers frequently encounter improved product performance and a decrease in recalls, contributing to both consumer safety and brand integrity.
The effects of this approval extend well beyond simple regulatory compliance; they significantly strengthen brand reputation, ease market access, and ultimately boost overall business success. As evidenced by Brazil's choice to establish its own quality assurance system, tailored to local needs, the strategic advantages of aligning with Inmetro Brazil's standards are clear. This approach not only fosters local industry growth but also ensures that products meet the specific safety and quality requirements demanded by the market.
Furthermore, global certification schemes like ATEX and IECEx exist for safe equipment use in hazardous areas, positioning Inmetro Brazil certification as a vital component in the landscape of international standards.
Conclusion
Achieving INMETRO certification is a critical milestone for medical device manufacturers aiming to succeed in the Brazilian market. The process, while complex, is essential for ensuring compliance with stringent safety and quality regulations set by INMETRO. By understanding the detailed steps required—from product classification to maintaining a robust quality management system—manufacturers can effectively navigate the certification landscape and position their products for success.
The challenges faced during this process, including intricate documentation requirements and evolving regulatory standards, can be daunting. However, by proactively addressing these issues and implementing effective quality measures, manufacturers can streamline their certification journey. Post-market surveillance further plays a vital role in maintaining compliance and enhancing product safety, reinforcing the commitment to quality long after the initial certification is granted.
Ultimately, the benefits of INMETRO certification extend far beyond mere compliance. It enhances credibility, provides a competitive edge, and fosters consumer trust, all of which are essential for thriving in a dynamic healthcare market. By prioritizing INMETRO certification, manufacturers not only safeguard public health but also unlock significant opportunities for growth and success in Brazil’s medical device industry.