Understanding Battery Quality: A Comprehensive Tutorial on Key Metrics and Testing
Explore essential metrics and testing methods to ensure optimal battery quality and performance.
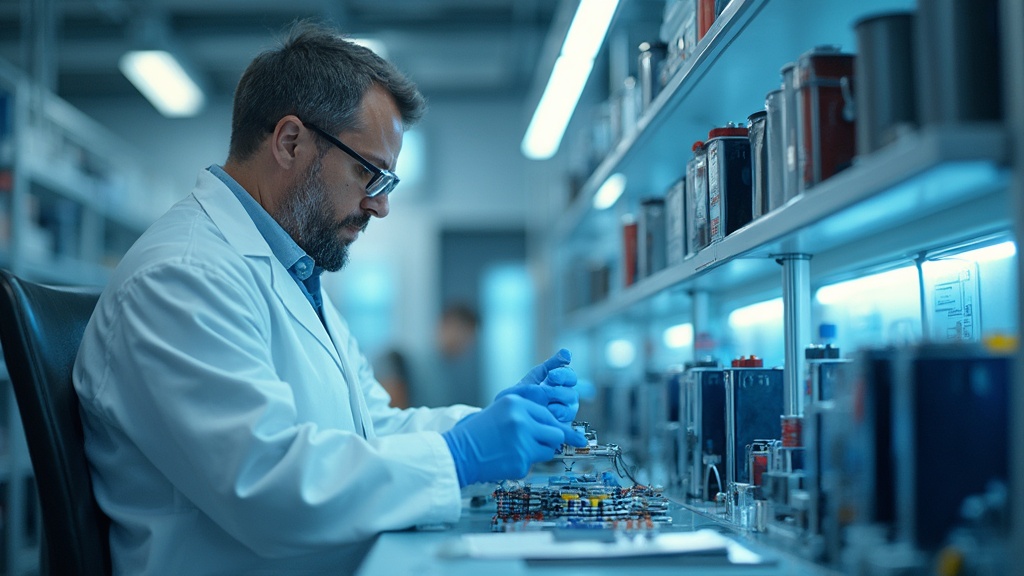
Key Highlights:
- Key metrics for battery evaluation include capacity, voltage, cycle life, internal resistance, self-discharge rate, temperature stability, and safety ratings.
- Best-in-class inspections are essential to verify these metrics and ensure product reliability and longevity.
- Rigorous testing methods such as visual inspection, electrical testing, cycle testing, temperature testing, metallographic analysis, safety testing, and environmental testing are vital for quality assurance.
- Recognized certifications like UL, CE, ISO 9001, RoHS, and UN38.3 enhance buyer confidence and ensure safety and quality standards are met.
- Future trends in battery technology include solid-state energy storage, recycling innovations, smart cells, fast-charging technologies, and sustainable materials like sodium-ion chemistries.
- Common battery quality issues include capacity loss, overheating, leakage, swelling, and inconsistent performance, with recommended solutions for each to mitigate risks.
Introduction
In the rapidly evolving world of battery technology, understanding the key metrics that determine battery quality is essential for manufacturers and consumers alike. As the demand for reliable energy storage solutions continues to surge, the importance of rigorous testing and certification processes cannot be overstated.
This article delves into the critical factors that influence battery performance, including:
- Capacity
- Voltage
- Safety ratings
While also exploring the latest trends shaping the industry, such as:
- The emergence of solid-state batteries
- Advancements in recycling
- Smart technology
Staying informed about these developments is crucial for making informed decisions in a competitive market. By addressing common quality issues and implementing effective solutions, stakeholders can enhance product reliability and consumer trust, ultimately driving the future of battery innovation.
Key Metrics for Evaluating Battery Quality
When evaluating power cell quality, several key metrics should be considered to ensure optimal performance and longevity, supported by best-in-class inspections that prevent quality issues:
-
Capacity (Ah): This metric quantifies the total charge a power source can hold, playing a crucial role in determining its longevity under specific loads. Best-in-class inspections can measure capacity through controlled discharge tests, ensuring that consumers receive products that meet their runtime expectations.
-
Voltage (V): The nominal voltage reflects the energy output of the power source and its compatibility with various devices. Inspections that test voltage output under various loads can confirm that the power source performs reliably across different applications.
-
Cycle Life: This indicates the number of charge and discharge cycles a cell can endure before experiencing significant capacity degradation. Inspections that simulate multiple cycles help verify cycle life claims, ensuring durability and value over time.
-
Internal Resistance: A critical quality indicator, lower internal resistance results in improved efficiency and reduced heat generation during both charging and discharging. Inspections can measure internal resistance to ensure that energy cells maintain high performance and safety standards.
-
Self-Discharge Rate: This metric measures how quickly a cell loses its charge when not actively in use. Inspections that evaluate self-discharge rates can identify higher quality cells that retain their charge longer when idle, minimizing customer dissatisfaction.
-
Temperature Stability: Quality cells should demonstrate dependable operation across a wide temperature range. Inspections can test performance under extreme conditions, confirming the robustness of design and materials.
-
Safety Ratings: Adherence to acknowledged safety standards, like UL or IEC certifications, is essential for evaluating the reliability and safety of energy storage devices in real-world applications. Thorough evaluations guarantee that safety certifications are fulfilled, safeguarding both customers and brands.
Failing to conduct these inspections can result in serious repercussions, such as heightened customer complaints, product returns, and harm to brand reputation.
In 2023, energy pack prices decreased by nearly 14% compared to 2022, indicating a significant change in the market that may affect consumer decisions. According to Visual Capitalist, the lithium-ion power source market size by installed capacity globally is projected to grow, indicating increasing demand and innovation in energy technology.
A deep understanding of these metrics, combined with rigorous inspections, is vital for evaluating performance and ensuring that users can make informed choices regarding battery quality to meet their specific needs. As trends in energy storage technology advance, staying aware of these key indicators will enable D2C brand owners to choose products that provide both excellence and safety. Furthermore, as stakeholders increasingly scrutinize ESG issues in the metals and mining sector, awareness of these policies can guide brand owners in aligning their product offerings with sustainable practices.
Testing Methods for Ensuring Battery Quality
To ensure optimal battery quality, several rigorous testing methods are employed:
-
Visual Inspection: This initial step involves a thorough examination for physical defects, including leaks, corrosion, or damaged terminals. It serves as the first line of defense in quality assurance, identifying potential issues before further testing.
-
Electrical Testing: Utilizing specialized equipment, this method assesses essential parameters such as voltage, capacity, and internal resistance, determining the efficiency of the energy storage device under load conditions. Such testing is critical to ensuring that the battery quality of energy sources can deliver the required power reliably.
-
Cycle Testing: This process executes a series of charge and discharge cycles to assess the lifespan and degradation in function over time. Cycle testing results are crucial for predicting energy storage longevity, which is increasingly important as demands for efficiency grow.
-
Temperature Testing: Batteries must be tested under extreme environmental conditions to gauge their performance and safety. This testing ensures that power sources can operate effectively in varied climates, which is especially relevant for products marketed in diverse regions.
-
Metallographic Analysis: This advanced technique involves examining the internal structure of power source components to identify potential weaknesses. By preparing samples for microscopic examination, this method checks for material quality and defects that could compromise performance.
-
Safety Testing: Testing for short-circuit, overcharge, and puncture scenarios is essential to guarantee that power sources can withstand adverse conditions without failure. Such assessments are critical in preventing safety hazards associated with power cell failures.
-
Environmental Testing: This testing assesses cell functionality across different temperatures and humidity levels, ensuring reliability in various real-world conditions. The significance of this approach is highlighted by the increasing need for power sources that can operate dependably despite environmental variations.
These collective methods not only help ensure battery quality for these energy storage devices to meet stringent standards but also bolster performance reliability in real-world applications, addressing the increasing demand for thorough testing, inspection, and certification of lithium-ion systems, driven by their high energy density and efficiency. Significantly, the economic importance of energy storage testing is emphasized by Africa's equipment market value for this purpose, which was USD 428 million in 2021. As Arbin Instruments states, they are "expanding its offerings to support future advancements in the energy storage sector," reflecting the industry's evolution.
Additionally, the case study on the Power Storage Testing Market in the Middle East & Africa illustrates how economic growth is driving demand from various end-use industries, further emphasizing the necessity of rigorous testing.
Importance of Battery Certifications
When choosing power cells for retail items, it is crucial to emphasize acknowledged certifications that ensure quality and safety. The following certifications are particularly significant in 2024:
-
UL Certification: This certification guarantees that products comply with rigorous safety standards for battery design and performance, which is essential for public protection and market acceptance. As stated by UL LLC, "Our certification process is designed to ensure that manufacturers can deliver safe and reliable products to buyers."
-
CE Marking: This symbol signifies conformity with European safety and environmental standards, assuring buyers that the product meets vital performance criteria. SGS SA emphasizes that 'CE marking is crucial for buyer trust in the European market, as it signifies adherence to rigorous safety standards.'
-
ISO 9001: This certification indicates a dedication to quality management practices and ongoing enhancement, signaling to buyers that the manufacturer prioritizes reliability and excellence.
-
RoHS Compliance: Ensuring that power sources are free from hazardous substances not only meets regulatory requirements but also appeals to environmentally conscious individuals, enhancing product attractiveness.
-
UN38.3: This safety standard for lithium cells addresses their performance under various conditions, crucial for ensuring safe usage and transport.
These certifications are not merely regulatory checkboxes; they significantly enhance buyer confidence in the battery quality of battery-operated products. As emphasized in a case study by TÜV Rheinland, UL certification has been associated with heightened sales of energy storage devices in 2024, illustrating its essential role in building public confidence and fostering market expansion. With Asia Pacific dominating the consumer power cell market share in 2023, where companies like Intertek Group plc and Bureau Veritas play pivotal roles, manufacturers must prioritize these certifications to remain competitive and meet evolving consumer expectations.
Future Trends in Battery Technology
The landscape of energy storage technology is rapidly evolving, driven by several key trends that are set to redefine energy solutions.
- Solid-State Energy Storage Devices: These advanced systems offer substantial advantages, including higher energy densities and enhanced safety compared to conventional lithium-ion options.
The Asia Pacific region, particularly China, Japan, and South Korea, is at the forefront of this innovation. With solid-state energy storage systems projected to dominate the market, China is anticipated to lead the industry, benefiting from significant government support and a remarkable compound annual growth rate (CAGR) of 62% from 2023 to 2030. Notably, the number of solid-state energy storage patents submitted in the Asia Pacific region surged by 180% between 2015 and 2020, highlighting the rapid innovation in this field.
-
Recycling Innovations: As environmental sustainability becomes a pressing concern, advancements in energy storage recycling processes are crucial. Innovations in this area not only enhance the sustainability of energy storage production but also reduce environmental impact, aligning with the increasing consumer demand for eco-friendly products. The recycling rate of power cells is anticipated to increase notably, indicating a transition towards more responsible manufacturing practices.
-
Smart Cells: The incorporation of digital monitoring systems into energy storage units is transforming management. These intelligent power sources will provide real-time performance data, thereby optimizing usage and prolonging lifespan. This technological leap is essential for both manufacturers and users seeking reliability and efficiency.
-
Fast-Charging Technologies: Recent advancements in materials and designs aim to significantly decrease charging durations without compromising power cell life. This trend is gaining momentum as individuals increasingly seek products that offer convenience alongside performance.
-
Sustainable Materials: Research into eco-friendly energy storage materials is poised to transform the sourcing and manufacturing landscape.
Sodium-ion chemistries, for instance, present a promising alternative due to their abundance and lower environmental costs. As highlighted by specialists from Straits Research, sodium-ion technologies are particularly encouraging because sodium is low-cost and plentiful, unlike lithium, which is extracted at a significant environmental expense.
Grasping these trends is crucial for producers and buyers alike, as they will influence future anticipations concerning battery quality, energy storage efficiency, and safety. Staying informed about these advancements will ensure that D2C brand owners can align their strategies with evolving market demands. Furthermore, the Asia Pacific region's dominance in the solid-state energy storage market, driven by the growth in the electric vehicle sector, underscores the real-world implications of these trends.
Common Battery Quality Issues and Solutions
Problems with battery quality can greatly affect functionality and safety, particularly as the cell value chain is anticipated to produce over $400 billion in worth by 2030. To safeguard your brand against negative reviews and customer dissatisfaction, it's crucial to address these common problems with effective solutions:
-
Capacity Loss: Frequently linked to behaviors like overcharging or deep discharging, capacity loss can result in reduced performance of the cell over time.
Solution: Implementing proper charging techniques, alongside the use of a power management system, can mitigate this issue effectively. -
Overheating: This issue not only diminishes lifespan but can also result in catastrophic failure. In 2024, overheating continues to be a pressing concern, as evidenced by recent reports highlighting its prevalence.
Solution: Ensuring adequate ventilation and avoiding exposure to extreme temperatures are crucial steps in preventing overheating. Experts emphasize that maintaining optimal operating conditions can significantly enhance battery quality and the longevity of the power source. As Aruna Madrekar, editor at Smartphone Thoughts, notes, "Addressing overheating issues is essential for the safety and efficiency of battery-operated devices." -
Leakage: Leakage often results from corrosion or manufacturing defects and poses risks to both the device and user safety.
Solution: Regular inspections of power sources are essential, and any signs of leakage warrant immediate replacement to avoid potential hazards. Employing OpsNinja's extensive inspection reports, featuring detailed photos and videos, can guarantee that standards are met, thereby safeguarding your brand from negative reviews and poor customer experiences. -
Swelling: Swelling is a clear indicator of internal damage or manufacturing defects.
Solution: If swelling occurs, it is vital to discontinue use immediately and dispose of the power source properly to prevent accidents. -
Inconsistent Performance: This issue may arise from insufficient standards during production, resulting in unpredictable power source behavior.
Solution: Choosing cells from trusted manufacturers recognized for strong assurance practices can help guarantee consistent performance and dependability. AQL numbers play a significant role here, as they guide the sampling process during inspections, determining how many products should be examined and acceptable defect levels.
The manganese supply stability case study illustrates the importance of a reliable supply chain in addressing these challenges. Awareness of these issues and their respective solutions empowers users to enhance the longevity and reliability of their battery-operated devices. As the battery industry evolves, addressing battery quality concerns will be critical for manufacturers and consumers alike, and leveraging detailed reporting and quality metrics will be essential in protecting your brand from negative reviews.
Conclusion
Understanding the key metrics and rigorous testing methods essential for evaluating battery quality is crucial in today’s energy-driven landscape. The article has highlighted several pivotal factors, including:
- Capacity
- Voltage
- Cycle life
- Safety ratings
These factors emphasize their significance in ensuring optimal performance and longevity. Through diligent inspections and certifications, stakeholders can mitigate common quality issues such as:
- Overheating
- Leakage
- Capacity loss
This, in turn, enhances consumer trust and product reliability.
As the industry evolves, emerging trends such as:
- Solid-state batteries
- Innovations in recycling
- The integration of smart technology
are set to reshape the future of battery technology. Manufacturers and consumers alike must stay informed about these advancements to make educated choices that align with their needs and values. The demand for sustainable practices and responsible sourcing will only grow, underscoring the importance of certifications and quality assurance in maintaining a competitive edge.
In conclusion, prioritizing rigorous testing and understanding the critical metrics for battery quality not only protects brands from negative consumer experiences but also drives the future of battery innovation. By embracing these principles, stakeholders can foster a more reliable and sustainable battery ecosystem, ultimately contributing to the advancement of energy storage solutions in a rapidly changing market.