Understanding and Solving Quality Control Problems: An In-Depth Tutorial
Explore key insights and solutions to effectively address quality control problems in your business.
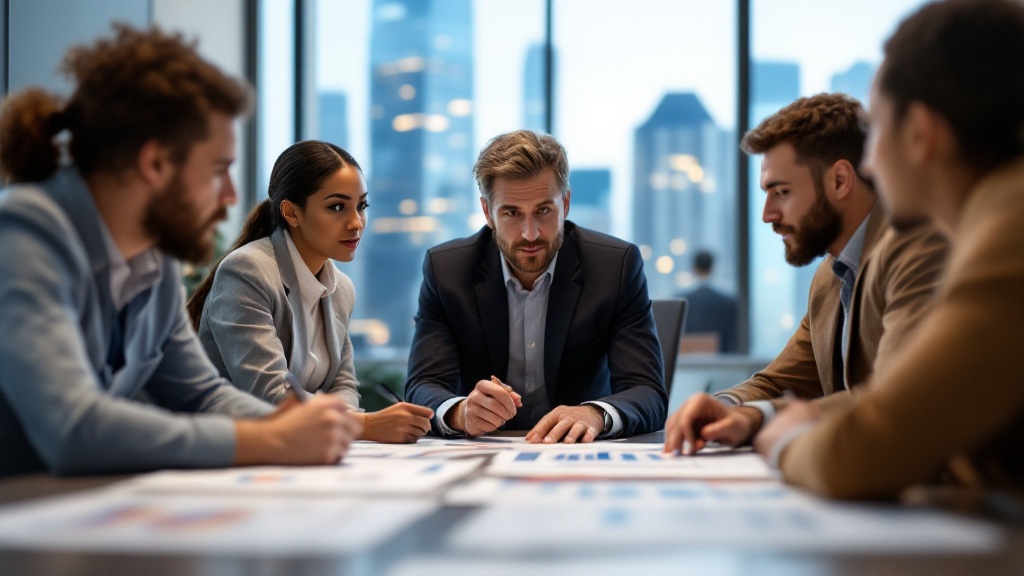
Key Highlights:
- Quality assurance (QA) involves systematic procedures to ensure products meet standards, with OpsNinja offering tailored checklist support for D2C brands.
- Key principles of quality control include defining benchmarks, evaluating performance, and implementing corrective actions for discrepancies.
- OpsNinja utilizes methodologies like risk assessment and root cause analysis to enhance product inspections and customer satisfaction.
- Investing in effective management practices can lead to a 40% reduction in customer complaints, as demonstrated by case studies involving OpsNinja's services.
- Common quality control mistakes include undefined standards, inadequate staff training, and poor documentation, which can lead to significant financial losses.
- Effective communication is crucial for quality control, with poor communication leading to wasted time and employee turnover.
- Lessons from aviation, such as the Boeing 737 MAX incidents, illustrate the severe consequences of quality control failures, emphasizing the need for strong management systems.
- Strategies for improving quality control processes include robust employee training, eCommerce analytics for monitoring, and fostering a culture of continuous improvement.
Introduction
In the competitive landscape of direct-to-consumer (D2C) brands, the significance of quality control cannot be overstated. As businesses strive to deliver exceptional products, the implementation of systematic quality measures becomes paramount.
This article delves into the principles of quality control, highlighting its critical role in safeguarding customer satisfaction and enhancing brand reputation. From identifying common pitfalls to exploring effective communication strategies, the discussion provides valuable insights into the multifaceted approach needed for robust quality management.
Furthermore, it draws parallels with the aviation industry, illustrating the dire consequences of quality failures and the lessons that can be applied across sectors. By embracing a culture of continuous improvement and leveraging advanced methodologies, organizations can not only mitigate risks but also drive sustainable growth through unparalleled product quality.
Defining Quality Control: Principles and Importance
Quality assurance (QA) includes the systematic procedures and measures established to ensure that items consistently meet set standards. OpsNinja specializes in offering customized checklist assistance, collaborating closely with D2C brands to suggest inspections specifically created for their unique products. This customized approach contrasts with one-size-fits-all solutions, ensuring that each brand receives the attention it deserves.
The foundational principles of control include:
- Defining specific benchmarks
- Evaluating actual performance against these criteria
- Undertaking corrective actions in response to any identified discrepancies
OpsNinja employs a variety of methodologies in their tailored checklist support, such as:
- Risk assessment
- Root cause analysis
These methodologies ensure that checks are not only relevant but also effective in addressing potential issues before they impact the customer. The necessity of an effective QC system cannot be overstated; it plays a pivotal role in:
- Safeguarding customer satisfaction
- Addressing quality control problems
- Mitigating costs associated with defects
- Bolstering brand reputation
Significantly, companies that invest in effective management practices can achieve an impressive 40% reduction in customer complaints. Recent case studies exemplify this impact:
- Maurice Mann, an Amazon seller, leveraged OpsNinja's inspections to boost his product ratings from 3.5 to 4.7 stars, recovering $1 million in revenue in the process. This case demonstrates how customized assessments can lead to significant financial recovery and enhanced customer trust.
- The Mindful Collective altered their method of assurance through OpsNinja, leading to substantial growth on Amazon, highlighting the wider effects of efficient management.
Considering recent data showing a 0.4% rise in the Producer Price Index (PPI) for final demand, with goods increasing by 0.7%, the pressure on manufacturers to avoid quality control problems and sustain high standards intensifies. As emphasized in the case study titled 'Importance of Statistics in Quality Management,' statistical methods such as:
- Statistical Process Management (SPM)
- Design of Experiments (DOE)
- Hypothesis testing
- Monitoring charts
These tools aid manufacturers in adapting to consumer demands and ensuring continuous improvement. In this competitive D2C environment, a strong assurance system not only ensures product dependability but also nurtures customer loyalty, which is vital for sustainable business expansion.
Common Quality Control Mistakes and How to Avoid Them
Common pitfalls in assurance often arise from quality control problems, which include:
- A lack of clearly defined standards
- Insufficient ongoing training for staff
- Inadequate documentation of processes
Many organizations fail to leverage data analysis to unearth trends and identify underlying quality control problems. The financial impact of quality control problems can be significant, as evidenced by our success in recovering over $2.6 billion for deserving clients, highlighting the necessity of addressing these challenges.
To effectively safeguard your brand from unfavorable reviews, utilizing OpsNinja's inspection services offers comprehensive reports that feature detailed photos, videos, and inspection instructions, allowing you to respond to the findings and improve product assurance. Establishing precise standards is essential to prevent quality control problems and serves as a foundation for all operations. Routine training sessions that strengthen these principles are essential for addressing quality control problems, improving staff comprehension and compliance with performance protocols.
The case study titled 'Enhancing Statistical Literacy for Junior Researchers' highlights the significance of training and ongoing education in assurance, preparing personnel to handle complexities in management. Moreover, understanding AQL numbers is crucial; these metrics indicate the standard of excellence acceptable for a product batch, guiding the inspection process by determining how many items to sample and what number of defects is permissible. Thorough documentation of standards management not only guarantees responsibility but also allows for the identification and resolution of quality control problems, enabling continuous assessment and enhancement.
By embracing a culture of continuous enhancement, organizations can proactively address potential quality control problems, thereby fostering an environment where excellence is prioritized at every level. As industry leaders highlight, 'Data integrity is a journey, not a destination,' emphasizing the necessity for a consistent and evolving approach to assurance in today's dynamic manufacturing landscape. Just as individuals doubting a misdiagnosis should ask about testing errors and think about obtaining a second opinion, D2C brand owners must perform comprehensive checks and assessments to ensure their offerings meet established standards.
The Role of Communication in Effective Quality Control
Effective communication is essential to strong control processes, as it directly impacts outcomes and operational efficiency. OpsNinja's dedicated support team exemplifies this by providing exceptional customer assistance, including detailed inspections, prompt feedback, and tailored recommendations, ensuring that all standards are clearly articulated and understood. Inefficient communication can lead to significant misunderstandings regarding standards, often resulting in quality control problems that affect brand reputation and financial performance.
Recent data reveals that:
- 70% of survey respondents identified wasted time as a consequence of poor communication.
- 12% indicated that lost employees represent a cost of ineffective business communication.
This highlights the urgent need for improvement in this area. As noted by customer Ernest Ofori, OpsNinja's thorough testing services and outstanding communication have proven invaluable, with comprehensive inspections supported by detailed pictures and videos that enhance transparency.
To cultivate a culture of clear communication, organizations should:
- Encourage open dialogue among team members and stakeholders.
- Adopt collaborative project management tools.
- Ensure that standards are consistently reinforced across all departments.
Regular meetings and updates act as vital tools for improving information flow, allowing teams to recognize and address issues more swiftly. Moreover, grasping the subtleties of communication is essential; the belief that 93% of communication is nonverbal has been disproven, highlighting the necessity for context-specific research that informs effective communication approaches in excellence management.
A recent survey indicates that 32% of teams now consider their organization to be ‘above average’ in terms of communication effectiveness, a notable increase from 25% last year. This change highlights the beneficial effect that targeted communication approaches, like those employed by OpsNinja, can have on overall standards and brand reputation, particularly in addressing quality control problems.
Consequences of Quality Control Failures: Lessons from Aviation
Quality control problems in the aviation sector can lead to catastrophic outcomes, with safety being the primary concern. The events related to the Boeing 737 MAX illustrate the severe consequences that emerge from quality control problems in standards. These failures not only led to tragic loss of life but also inflicted substantial financial damage—estimates suggest that the economic toll of such incidents can reach hundreds of millions annually, with the aviation insurance market struggling to break even as claims have surpassed premiums for six consecutive years.
Additionally, the economic impact of bird strikes, estimated at $400 million annually in the US and $1.2 billion globally, emphasizes the wider financial consequences of standards failures in aviation. As emphasized by industry expert Smith, as drone use expands into various sectors, claims will become more pertinent; this highlights the cascading effects of control failures, as heightened drone activity may result in more incidents and claims. Additionally, the financial ramifications are exacerbated by the costs associated with top-of-the-range aircraft engines, which can exceed $40 million each, significantly inflating repair and replacement expenses.
The examination of the impact of multipath effects on the electromagnetic surroundings of localizers offers additional context; it highlights how essential navigation systems can be undermined, emphasizing the necessity for careful management practices. Insights from this case study reveal that understanding and mitigating such effects is crucial for maintaining safety practices. As lessons learned from the Boeing 737 MAX incidents emerge, it becomes increasingly clear that strong management systems are essential to address quality control problems and ensure accountability across all organizational levels.
By paying attention to these lessons, organizations in all sectors can better understand the significance of upholding strict excellence measures to prevent similar disasters.
Strategies for Enhancing Quality Control Processes
To significantly enhance control processes, D2C brands should implement a multifaceted strategy that includes:
- Robust employee training programs
- The utilization of eCommerce analytics for ongoing monitoring
- Cultivating a culture centered on continuous improvement
Given the highly competitive nature of industry-specific Quality Management System (QMS) solutions, investing in employee development becomes crucial. In 2021, the average expenditure on training and development approached almost $1300 per employee, highlighting the significance of providing personnel with the essential abilities to maintain excellence.
Training on QMS standards, such as ISO 9001, not only ensures compliance but also enhances overall management practices, especially in a competitive landscape where adherence to standards can differentiate a brand. Routine audits and evaluations, especially those provided by OpsNinja, are crucial for identifying quality control problems within assurance processes and enabling prompt actions. Moreover, utilizing advanced technology—including automated oversight systems and real-time monitoring tools—can optimize operations and improve item standards.
For example, eCommerce analytics can be utilized to monitor customer feedback and item returns, enabling brands to make data-informed choices that enhance standards. As the World Quality Report suggests, product teams should strive to allocate up to 25% of their QA budgets towards extending in-house capabilities and integrating the right testing tools. By consistently improving these strategies and collaborating with reliable providers like OpsNinja, organizations can attain superior levels of assurance, thereby enhancing customer satisfaction and nurturing long-term loyalty.
The link between increased training expenditure and improved compliance outcomes is clear in case studies, which demonstrate that effective training on QMS standards leads to enhanced management practices, while OpsNinja protects over 650 brands from quality control problems and negative customer experiences through reliable inspections and audits. Contact OpsNinja today to see how our solutions can protect your brand from quality control problems.
Conclusion
In the realm of direct-to-consumer brands, quality control stands as a cornerstone of success, directly influencing customer satisfaction and brand reputation. The principles of quality control, including the establishment of clear benchmarks, continuous training, and effective communication, are essential for mitigating risks associated with product defects. Emphasizing a proactive approach through tailored inspections, as demonstrated by OpsNinja, can lead to significant improvements in product ratings and customer trust, ultimately resulting in financial recovery and sustainable growth.
Common pitfalls in quality control can be easily avoided by fostering a culture of continuous improvement and leveraging data analysis to identify trends and underlying issues. This approach not only safeguards against negative reviews but also enhances operational efficiency through precise documentation and ongoing training initiatives. As industry leaders highlight, the journey towards quality is ongoing, necessitating a commitment to refining processes and standards.
The lessons drawn from the aviation industry underscore the dire consequences of quality failures, reinforcing the critical need for robust quality management systems across all sectors. By adopting comprehensive strategies that prioritize communication, employee development, and advanced technology, D2C brands can navigate the complexities of quality control more effectively. In doing so, organizations not only enhance product reliability but also cultivate customer loyalty, paving the way for enduring success in a competitive landscape.