Understanding and Fixing QC Issues: An In-Depth Tutorial for Quality Control Professionals
Explore essential strategies for identifying and fixing QC issues to enhance product quality.
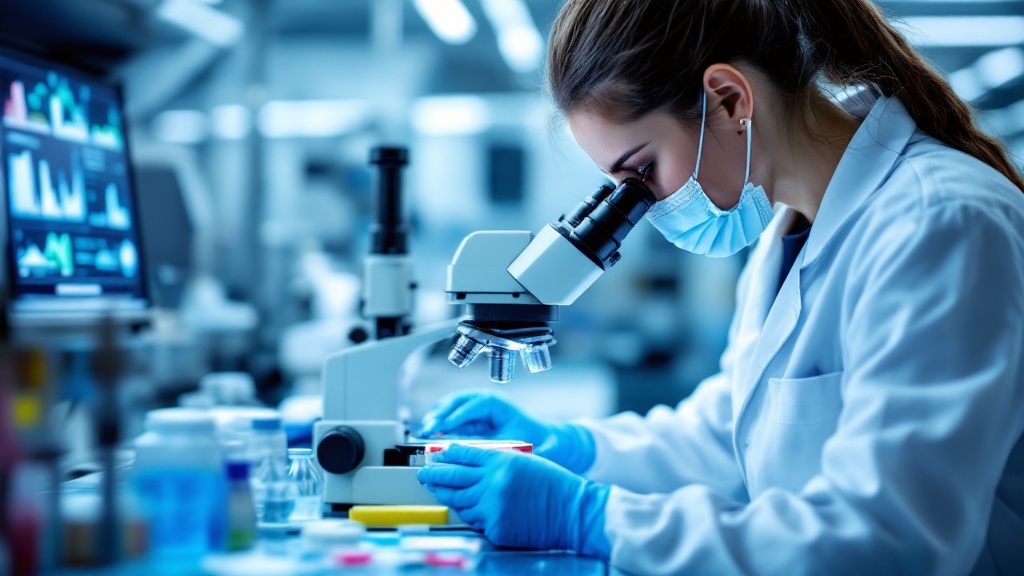
Introduction
In the competitive landscape of modern business, quality control (QC) has emerged as a cornerstone of operational success. As organizations strive to meet rising consumer expectations and navigate increasingly complex supply chains, understanding the fundamentals of QC becomes imperative.
This article delves into the critical aspects of quality control, including:
- Identifying common pitfalls
- Leveraging advanced technologies
- Implementing data-driven strategies
By highlighting the profound impact of effective QC practices on brand reputation, customer satisfaction, and overall profitability, it underscores the necessity for businesses to adopt a proactive and tailored approach.
Through real-world examples and actionable insights, readers will discover how robust quality control measures can not only prevent costly errors but also drive sustainable growth in today's dynamic market.
Fundamentals of Quality Control: Definitions and Importance
Quality control (QC) represents a systematic approach focused on ensuring products meet predefined requirements and standards. This process involves a range of activities, including inspection, testing, and thorough documentation. The significance of QC cannot be overstated; it is instrumental in preventing defects, minimizing waste, and significantly enhancing customer satisfaction.
The customized checklist assistance guarantees that inspections are specifically tailored for each distinct product, shifting away from generic solutions. This customized assurance not only safeguards a brand’s reputation but also enhances operational efficiency and profitability.
In 2024, the significance of QC in business operations has never been more crucial, as organizations aim for excellence in increasingly competitive markets. The efficient and detailed inspection services offered, which include comprehensive inspection checklists for all product components, stand out compared to traditional methods. This method decreases returns and improves client retention by tackling avoidable QC issues.
Significantly, client success narratives, like how Movley assisted an Amazon seller in regaining $1 million in revenue by enhancing star ratings from 3.5 to 4.7 through targeted assessments, demonstrate the tangible effect of effective control measures.
Additionally, as shown by the case study titled 'Data-Driven Service Strategies,' monitoring service statistics enables businesses to recognize operational inefficiencies and customize services to fulfill client needs, ultimately resulting in strategic enhancements and improved experiences. By grasping these fundamentals, professionals can truly appreciate the pivotal role QC plays within the broader context of business success, especially for D2C brand owners aiming to scale and optimize their operations.
Identifying Common Quality Control Issues
Frequent qc issues can greatly affect product standards and client satisfaction, with ineffective sampling being one of the most widespread problems. Poorly designed sampling methods can lead to qc issues, resulting in inaccurate assessments that allow defects to slip through the cracks. This concern is amplified by the fact that only 4% of dissatisfied customers express their grievances directly to companies, indicating a gap between perceived standards and actual experiences.
Insufficient feedback can conceal qc issues that assurance procedures should proactively tackle. Additionally, improper testing methods may result in qc issues, leading to undetected defects that ultimately jeopardize product integrity. Documentation challenges, particularly qc issues, also play an essential role; inadequate record-keeping can obscure the assurance process and lead to compliance issues.
As specialists observe, tackling these challenges is essential for professionals seeking to improve their operations. The thorough inspection reports, which include detailed assessments, actionable insights, and essential elements like photos, videos, and inspection instructions, safeguard brands against negative reviews and enhance customer experiences. Additionally, organizations such as The Mindful Collective have undergone significant growth—reaching 7-figure revenues—through improved oversight practices offered by Movie.
Similarly, Hash Stash has streamlined its operations and inspected over 10,000 units monthly, significantly improving its operational efficiency. Acknowledging that 88% of executives think call recording is the most utilized contact center technology highlights the crucial role of technology in enhancing control processes. However, the lack of mature tools remains a significant barrier in adopting AI for assurance activities.
By understanding and addressing these qc issues, teams can develop more effective strategies to ensure product excellence and elevate customer satisfaction. Significantly, Maurice Mann obtained $1 million in revenue through these efficient inspections, emphasizing the considerable influence of standards on brand success.
Consequences of Poor Quality Control Practices
Ineffective quality control practices can have profound and lasting repercussions for businesses, including:
- Increased Costs: Quality defects frequently lead to expensive recalls and rework, significantly impacting the bottom line. It is estimated that SDRs waste an average of 27% of their potential selling time due to unreliable data, which compounds the financial strain on organizations.
This inefficiency can also demoralize sales teams, leading to dissatisfaction and the potential departure of top sellers who feel hindered by inadequate data. For instance, Maurice Mann, an Amazon seller, encountered comparable challenges until he sought assistance from Movley, recovering $1 million in revenue and increasing his star rating from 3.5 to 4.7 through effective inspections.
- Loss of Client Trust: Ongoing qc issues can undermine brand image and reduce client fidelity. Stacy Roach, a Senior Data Advisor, emphasizes,
When sales teams can’t hit their numbers and they know it’s because of bad data, they’ll find somewhere else to work, fast.
This feeling emphasizes how qc issues not only impact sales but also endanger overall client trust.
The resulting low morale among sales teams can further exacerbate the situation, as disengaged employees may not deliver their best performance. The customized strategy for standards management has helped brands such as The Mindful Collective in reshaping their operations and encouraging expansion on platforms like Amazon. For instance, after implementing Movley's inspections, The Mindful Collective reported a 30% increase in customer satisfaction and a significant boost in their sales metrics.
- Regulatory Non-Compliance: Organizations that fail to adhere to industry standards may face legal penalties and a loss of market access, further complicating their operational landscape. Such non-compliance can lead to significant financial repercussions and damage to reputation, which may be difficult to recover from.
Comprehending these potential impacts highlights the critical need for strong control protocols to mitigate qc issues. By measuring data quality against six essential dimensions—completeness, accuracy, consistency, validity, uniqueness, and timeliness—businesses can implement tailored metrics that enhance data integrity and support informed decision-making. Each dimension plays a vital role: for instance, completeness ensures all necessary data is available, while accuracy verifies that the data is correct, and consistency guarantees that data remains uniform across different systems.
This proactive approach not only safeguards financial performance but also fortifies customer relationships, ultimately leading to sustainable success. Furthermore, unlike competitors such as HTQS, this company offers a high-touch service model with tailor-made teams that provide personalized support, ensuring that brands receive the attention and expertise they need to thrive.
Strategies for Addressing and Fixing QC Issues
To effectively tackle and resolve QC issues, consider implementing the following strategies:
- Implement Regular Audits: Conducting frequent audits is essential to assess QC processes and pinpoint areas in need of improvement. Movley’s supplier audits ensure good standing and long-term cooperation, which are essential in maintaining supplier standards and reliability.
The forthcoming AS 1000 standard, applicable for audits of financial statements for fiscal years starting on or after December 15, 2024, highlights the essential role of regular audits in upholding standards. This standard not only establishes benchmarks for financial accuracy but also emphasizes the need for ongoing evaluations to ensure compliance and excellence.
-
Enhance Training Programs: It is crucial to ensure that all staff involved in QC are thoroughly trained on best practices and emerging technologies. Training programs have been demonstrated to significantly influence QC issues, providing personnel with the skills essential to maintain standards and adapt to new regulations like AS 1000.
-
Utilize Root Cause Analysis: Investigating the underlying causes of performance issues is vital for developing effective long-term solutions. As one participant noted,
"If you normally feel you are not in a position to say something about a certain subject then the audit has the effect of empowering you to do something about it (…) The audit facilitates discussing issues that otherwise would not have occurred."
Grasping the differences between audits, improvement initiatives, and assurance—as emphasized in recent studies—can guide these strategies, ensuring that each process contributes to a cohesive management framework.
For example, Maurice Mann enhanced his Amazon star ratings from 3.5 to 4.7 and regained $1 million in revenue through efficient control methods supported by the company. Another client shared, "The thoroughness and accuracy of their inspections have been a game changer for my business." By adopting these strategies and utilizing inspection services, professionals can significantly enhance their QC outcomes and effectively manage QC issues to ensure a strong management framework.
Explore more customer stories to see how money has positively impacted brands like yours!
Leveraging Technology and Data for Improved Quality Control
To enhance qc issues, leveraging technology and data is essential. Here are three key approaches:
- Implement Management Systems (QMS): Embrace comprehensive software solutions that streamline control processes and deliver real-time data analysis, facilitating compliance with standards such as ISO 9001.
Training employees on these systems is crucial; as noted by Statista, the average investment in learning and development reached nearly $1300 per worker in 2021. This investment directly correlates with enhanced compliance and overall management outcomes, which reflect a commitment to continuous improvement while also addressing qc issues.
-
Tailored Standard Checklist Support: Collaborate with your assessment team to develop customized checklists that cater to the unique aspects of your products, ensuring that every evaluation is relevant and effective. Unlike one-size-fits-all methods, Movley’s customized support improves the accuracy of assurance efforts.
-
Adopt IoT Devices: Integrate Internet of Things (IoT) devices to monitor product standards in real-time during production. This technology allows prompt feedback and adjustments, significantly improving assurance efforts.
-
Achieve Operational Efficiency with On-site Inspections: Prevent returns by identifying issues early through Movley’s on-site inspections, which tackle the 60% of returns linked to avoidable problems. This proactive approach allows your team to focus on building the business rather than managing operational distractions, providing total peace of mind.
-
Analyze Data Trends: Utilize advanced data analytics to identify trends and anomalies, allowing for proactive adjustments to assurance processes. Forrester predicts that software testers harnessing generative AI could see productivity gains of up to 15 percent, underscoring the transformative potential of data-driven decision-making. Moreover, QA Tech is endorsing an early access initiative for new clients, highlighting the sector's shift towards innovative solutions in assurance.
By adopting these technologies and customized assistance, D2C brand owners can greatly enhance precision and effectiveness in assurance processes, ultimately improving product standards and addressing qc issues to boost customer contentment. Movley’s approach stands in contrast to traditional methods, reinforcing its commitment to superior quality control.
Conclusion
Effective quality control is not merely a regulatory requirement; it is a vital component of a successful business strategy. This article has explored the essential elements of QC, emphasizing the importance of:
- Identifying common pitfalls
- Leveraging advanced technologies
- Implementing data-driven strategies
By addressing these areas, organizations can significantly enhance product quality, foster customer satisfaction, and ultimately drive profitability.
The consequences of neglecting quality control practices can be severe, leading to:
- Increased costs
- Loss of customer trust
- Potential regulatory non-compliance
As demonstrated through real-world examples, such as Movley’s impact on businesses like The Mindful Collective and Maurice Mann, a tailored approach to quality inspections can yield substantial financial recoveries and improved customer experiences.
In today's competitive landscape, the integration of technology and data into quality control processes is essential for maintaining an edge. Utilizing quality management systems, customized checklists, and real-time monitoring through IoT devices enables organizations to proactively address quality issues before they escalate. By embracing these strategies, businesses not only safeguard their reputation but also position themselves for sustainable growth.
As the demand for high-quality products continues to rise, investing in robust quality control measures is paramount. Organizations must prioritize QC as a strategic initiative, ensuring that they are well-equipped to meet consumer expectations and thrive in an ever-evolving marketplace. The journey toward excellence in quality control is ongoing, and those who commit to continuous improvement will reap the rewards of enhanced operational efficiency and lasting customer loyalty.