Top 10 Digital Transformation Trends in Manufacturing for 2024
Explore the top digital transformation trends in manufacturing for 2024, from AI to IoT advancements.
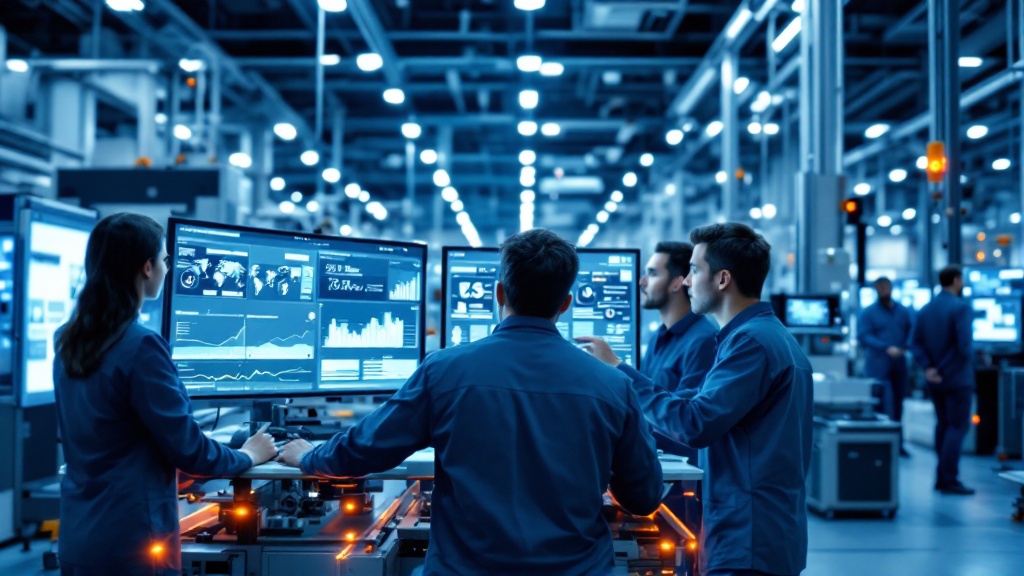
Introduction
The manufacturing sector is on the brink of a transformative era, driven by the integration of digital technologies that redefine operational paradigms. As organizations strive to enhance efficiency, reduce costs, and deliver exceptional value to customers, digital transformation emerges as a critical strategy for sustainable growth. This evolution encompasses a range of innovations, including:
- Artificial intelligence
- The Internet of Things
- Data-driven decision-making
- Quality assurance measures
However, the journey toward a fully digitalized operation is not without its challenges, including:
- Cultural resistance
- The need for skilled talent
As manufacturers navigate this complex landscape, understanding the emerging trends and technologies will be essential for maintaining a competitive edge in an increasingly demanding market.
Understanding Digital Transformation in Manufacturing
Digital transformation in manufacturing reflects one of the top digital transformation trends in manufacturing, showcasing a pivotal shift in how organizations integrate digital technology across their operations. This transition transcends the mere adoption of advanced tools; it fundamentally redefines producers' strategies for delivering value to customers. The scope of digital transformation trends in manufacturing spans:
- Automating production processes
- Leveraging data analytics for strategic decision-making
- Enhancing overall operational effectiveness
In an environment characterized by increasing efficiency demands and cost-reduction pressures, producers are compelled to embrace this transformation not only for survival but also for sustainable growth. However, the journey is fraught with challenges—14% of IT decision-makers cite resistant company culture as a significant hurdle. According to the case study titled 'Challenges in Digital Transformation,' organizations face significant hurdles such as:
- Complexities in existing systems
- A shortage of technical talent
- High implementation costs
Notably, PwC highlights that 55% of employers are concerned about the lack of essential skills in digital transformation initiatives. To navigate these challenges, proactive standards control is essential. With Movley's on-site inspections, manufacturers can achieve operational efficiency by preventing bad batches—60% of returns are due to avoidable issues—and minimizing returns, thereby protecting their brand reputation.
Furthermore, 94% of customers have refrained from making a purchase due to a negative review, highlighting the significance of upholding standards. As companies embrace the top digital transformation trends in manufacturing, they acquire the agility required to respond effectively to market dynamics, achieving total peace of mind and highlighting the critical importance of digital integration and quality assurance in today’s operational processes. Recent news indicates that adopting the top digital transformation trends in manufacturing has been shown to improve how companies operate and respond to market needs in a more agile manner, further emphasizing the necessity of this shift.
Key Digital Transformation Trends in Manufacturing for 2024
As we approach 2024, several pivotal digital transformation trends are set to shape the production sector significantly:
-
Artificial Intelligence (AI): AI technologies are poised to enhance operational efficiency and refine decision-making processes across manufacturing operations. The adoption of AI is expected to increase, with organizations leveraging advanced analytics to optimize production and reduce costs.
-
Internet of Things (IoT): The integration of IoT devices will enable manufacturers to achieve real-time monitoring and control over their processes, leading to improved productivity and reduced downtime. This technology enables seamless information flow, facilitating better inventory management and predictive maintenance.
-
Multi-Cloud Utilization: Manufacturers are increasingly recognizing the advantages of multi-cloud strategies, which enhance flexibility and enable better data management. This approach allows companies to utilize various cloud services tailored to different operational needs, fostering innovation and agility.
-
Robotic Process Automation (RPA): RPA will continue to streamline repetitive tasks, freeing human workers to concentrate on more complex and strategic activities. This shift is crucial in enhancing overall productivity and can lead to significant cost savings in the long run.
-
Sustainability Initiatives: Digital tools will be instrumental in tracking and enhancing sustainability efforts within production operations. Companies are increasingly focused on integrating sustainable practices, driven by consumer demand and regulatory pressures. By leveraging technology, manufacturers can monitor their environmental impact and implement changes that promote sustainability, reflecting the top digital transformation trends in manufacturing.
In light of these trends, industry experts emphasize the importance of adapting to the complexity of the current environment. As highlighted by TEKsystems, 'the complexity of the current environment, gaps in technical talent, and high costs are leading digital transformation challenges.' Addressing these challenges is essential, especially considering that 77% of small businesses utilize social media to enhance brand recognition, illustrating the broader need for effective digital strategies. Furthermore, the case study titled 'Challenges in Digital Transformation' outlines the significant hurdles organizations face in successfully implementing these initiatives. This evolving landscape presents both challenges and opportunities, making it essential for industry leaders to stay ahead of these trends to maintain competitive advantage.
Leveraging AI to Optimize Operational Efficiency
The top digital transformation trends in manufacturing include Artificial Intelligence, which is fundamentally transforming operational efficiency through advancements in predictive maintenance, performance control, and supply chain optimization. AI algorithms excel at analyzing real-time data from machinery, enabling manufacturers to forecast potential failures before they materialize. This proactive approach significantly minimizes downtime and repair costs, enhancing overall productivity.
In this landscape, Movley's detailed inspection services stand out.
By offering customized checklists that pose 15-20 questions regarding your business and product, and involving skilled inspectors, Movley surpasses conventional methods, where random inspectors might overlook critical issues. Their platform ensures stringent control standards, essential for preventing bad batches and minimizing returns—crucial for protecting brand reputation. Movley also stores product assets and connects businesses with the appropriate inspectors, further improving the inspection process.
Additionally, AI-driven control systems have become essential, as they can quickly detect defects during the manufacturing process, ensuring a superior output. For instance, Emmanuel Acquah, a noted industry expert, highlights the effectiveness of such technologies, stating:
Telefonica O2, a leading digital communications company, implemented RPA and now handles 400,000 to 500,000 transactions monthly using just 160 robots, yielding a three-year return on investment of over 650%.
This example demonstrates the substantial influence AI can exert on operational expenses and productivity, reinforcing the case for its integration in manufacturing.
With Movley's proactive on-site inspections, brands can identify issues early, preventing returns—60% of which are due to avoidable problems, according to Return Logic. As the trend of employing AI for performance monitoring accelerates, integrating Movley’s services can significantly enhance operational efficiency, positioning it among the top digital transformation trends in manufacturing.
The Rise of Data-Driven Strategies in Manufacturing
As the manufacturing landscape evolves, embracing the top digital transformation trends in manufacturing is becoming essential for companies aiming to enhance operational efficiency and product quality. Recent insights indicate that 83% of CEOs recognize the necessity of transforming their organizations into data-driven entities, underscoring the critical role of data-informed decision-making in today’s competitive environment. The Internet of Things (IoT), characterized as a network of interconnected devices equipped with sensors, software, and other technologies, is one of the top digital transformation trends in manufacturing as it plays a crucial role in facilitating real-time information collection and analysis.
In 2024, producers are set to substantially boost their investment in analytics tools, with expenditure in the Asia Pacific area expected to hit an impressive US$42.2 billion. This influx of resources will facilitate the gathering and analysis of information from diverse sources, including production lines and customer feedback, allowing producers to identify emerging trends and enhance their processes effectively. Notably, 54% of companies are already considering cloud computing as part of their data analytics strategies, reflecting a broader movement towards leveraging cloud solutions for enhanced flexibility and data management.
Additionally, incorporating Movley's on-site inspections can prevent bad batches and returns, further protecting brand reputation. This proactive control measure allows manufacturers to catch issues early, ensuring that 60% of returns, which are preventable, do not impact their bottom line. Moreover, given that 94% of customers have refrained from making a purchase because of a negative review, addressing concerns before products reach consumers is essential for preserving a positive brand reputation.
As we look forward, the focus on analytics and quality assurance will not only enhance production processes but also align with the top digital transformation trends in manufacturing, fostering innovation throughout the sector and ensuring that companies stay competitive and responsive to customer demands.
Harnessing IoT and 5G for Enhanced Connectivity
The convergence of Internet of Things (IoT) devices and 5G technology is poised to significantly enhance manufacturing connectivity in 2024. With the number of connected IoT devices expected to hit 18.8 billion worldwide by year-end, producers will gain from the capacity to gather real-time information from machinery and production lines. This capability will not only facilitate improved monitoring and control of operations but will also enable rapid adjustments in response to fluctuating production demands.
However, the ongoing chip shortage continues to hinder the IoT market recovery, presenting a challenge to manufacturers looking to fully leverage these technologies. High-speed 5G connectivity is critical in this equation, offering the necessary bandwidth for seamless data exchange and communication between devices. As highlighted by a previous IoT Product Lead at Microsoft, while IoT services themselves may face challenges in being profit-generating, their incorporation into production processes heralds a new era of efficiency.
Furthermore, in 2021, around 99,534 patents safeguarding IoT inventions were filed globally, underscoring the innovation driving this sector. Despite economic challenges, including cautious enterprise spending due to inflation and geopolitical conflicts, 51% of enterprise IoT adopters plan to increase their budgets in 2024, indicating continued investment in IoT technologies. The synergy of IoT and 5G is among the top digital transformation trends in manufacturing, as it stands to revolutionize operational capabilities and dramatically enhance overall efficiency.
Conclusion
The digital transformation of the manufacturing sector is not merely an evolution; it is a necessity for organizations seeking to thrive in a competitive landscape. As highlighted throughout the discussion, the integration of technologies such as artificial intelligence, the Internet of Things, and data-driven decision-making is reshaping operational frameworks, driving efficiency, and enhancing customer value. These advancements allow manufacturers to automate processes, harness real-time data, and improve quality control, ultimately leading to sustainable growth.
However, the path to successful digital transformation is fraught with challenges, including cultural resistance and a shortage of skilled talent. Addressing these hurdles is crucial for manufacturers to fully realize the benefits of digitalization. Proactive measures, such as implementing rigorous quality assurance protocols and embracing innovative technologies, can mitigate risks and enhance operational performance. The importance of maintaining product quality cannot be overstated, especially considering the significant impact of customer perception on brand reputation.
As the manufacturing landscape continues to evolve, staying informed about emerging trends and technologies will be essential for maintaining a competitive edge. The convergence of IoT and 5G, along with the rise of data-driven strategies, presents both opportunities and challenges that require strategic foresight. By embracing digital transformation, manufacturers can not only enhance their operational efficiency but also position themselves for long-term success in an increasingly dynamic market.