How to Solve Common Problems with Quality Control: A Step-by-Step Guide
Discover effective solutions for common problems with quality control in this comprehensive guide.
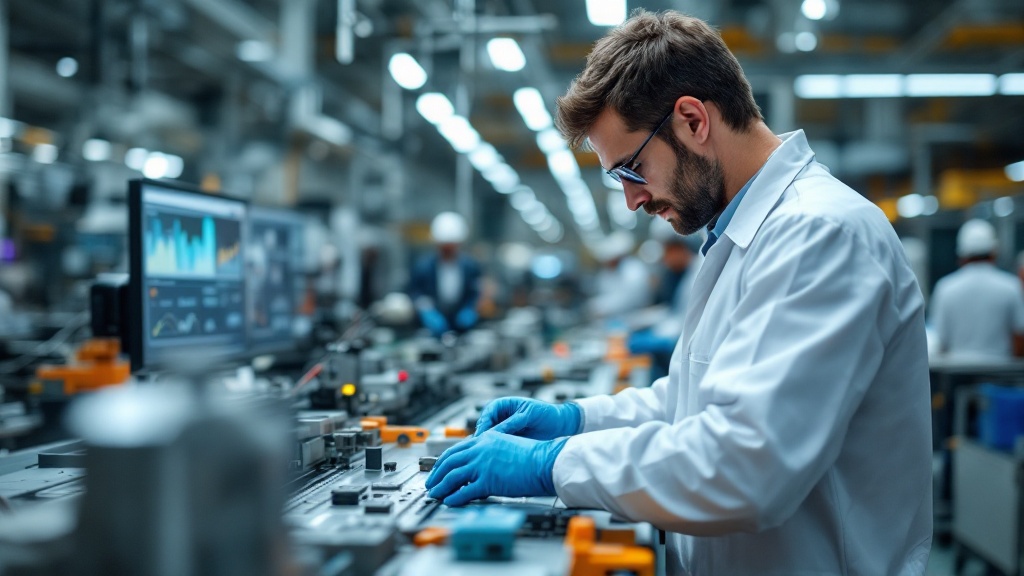
Key Highlights:
- Common quality control challenges include ineffective sampling plans, improper testing procedures, insufficient training, inadequate documentation, and quality of materials.
- Effective strategies to resolve quality control issues involve comprehensive training programs, detailed documentation, regular audits, utilizing technology, engaging with suppliers, and validating procedures.
- Implementing a Quality Management System (QMS) requires defining standard policies, setting measurable objectives, documenting processes, assigning responsibilities, monitoring performance, and fostering continuous improvement.
- Data analytics can enhance quality control by collecting quality information, analyzing trends, utilizing predictive analytics, benchmarking performance, and developing detailed reports for stakeholders.
- Engaging customers in quality assurance is crucial; strategies include soliciting feedback, forming client advisory boards, incorporating client insights into product development, communicating changes, and rewarding participation.
Introduction
In the competitive landscape of modern manufacturing, maintaining high-quality standards is not merely a goal but a necessity. Quality control challenges can arise from various sources, impacting both production efficiency and the integrity of the final product.
This article delves into the common pitfalls organizations face, including:
- Ineffective sampling plans
- Inadequate training
- Supplier quality issues
It also explores effective strategies for resolving these challenges, emphasizing the importance of:
- Comprehensive training
- Detailed documentation
- Integration of technology
Furthermore, implementing a robust Quality Management System (QMS) and leveraging data analytics can significantly enhance quality control processes. By engaging customers in quality assurance efforts, businesses can foster trust and loyalty, ensuring their products meet the highest standards.
This comprehensive guide offers valuable insights for organizations striving to elevate their quality control practices and safeguard their brand reputation.
Identifying Common Quality Control Challenges
Numerous factors can lead to problems with quality control, which frequently affect production efficiency and item standards. Here are some of the most common issues you may encounter:
- Ineffective Sampling Plans: A significant number of brands encounter challenges in choosing suitable samples for testing, resulting in misleading representations of item standards.
AQL (Acceptable Quality Level) numbers are specific values that indicate the standard of excellence acceptable for a product batch and guide the sampling process during inspections. A valid sampling plan, informed by AQL metrics, ensures that your testing accurately reflects the overall batch standard, thereby helping to avoid problems with quality control and protect your brand from negative reviews.
- Improper Testing Procedures: Adherence to standardized testing procedures is vital for obtaining consistent and reliable results.
Deviations can lead to problems with quality control, resulting in unreliable data that misguides critical decision-making. Employing AQL standards during testing can mitigate problems with quality control, thereby improving the reliability of outcomes and ensuring adherence to standards that protect your brand reputation.
- Insufficient Training: Insufficient training on control processes can lead to problems with quality control, causing mistakes and oversights among employees.
Conducting regular training sessions centered on AQL comprehension is vital to provide your team with the information required to maintain standards effectively, thereby avoiding negative customer experiences.
- Inadequate Documentation: Poor record-keeping practices can result in confusion and inconsistencies within assurance processes.
A robust documentation system that includes AQL metrics is necessary to accurately track control measures and to prevent problems with quality control, ensuring accountability. For instance, maintaining detailed logs of inspections and test results can significantly enhance transparency and traceability in management.
- Quality of Materials: The caliber of materials obtained from suppliers can lead to problems with quality control, significantly affecting the overall standard of your final product.
Establishing robust connections with suppliers and performing regular evaluations are crucial measures to guarantee adherence to your standards. OpsNinja's thorough evaluations demonstrate how efficient supplier management can improve standards, ultimately boosting revenue recovery and brand protection. For instance, their systematic method of examining incoming materials has assisted brands like Caddent Golf in guaranteeing that only top-notch components are utilized in production.
As mentioned in a recent press announcement from MachineMetrics,
Production scheduling is among the most essential tasks in contemporary manufacturing
this highlights the significance of tackling these standards management challenges proactively.
Ongoing observation and enhancement of production processes, including AQL evaluations, are essential for preventing problems with quality control and upholding high manufacturing standards. Considering that between 15% and 40% of manufacturing capacity is utilized on rework due to problems with quality control, implementing Statistical Process Control (SPC) and enhancing your management systems can serve as proactive measures to alleviate these challenges.
Effective Strategies for Resolving Quality Control Issues
To effectively resolve quality control issues and protect your brand's reputation, consider implementing the following strategies:
-
Implement Comprehensive Training Programs: Regular training sessions for employees involved in standards assurance are essential. These programs should highlight the significance of excellence standards, testing procedures, and documentation practices. A study by Yazdanifard et al. underscores that well-structured employee training significantly enhances productivity, making it a critical investment for your team. Furthermore, 94% of workers indicate that development opportunities would keep them in a role, highlighting the necessity of robust training programs.
-
Develop Detailed Documentation: Create an extensive manual for assurance that clearly outlines all procedures, standards, and responsibilities. This manual will serve as a vital reference for employees, ensuring consistency and clarity in practices. Effective documentation is crucial to address the problems with quality control, as highlighted by recent findings indicating that 90% of employers recognize the benefits of mobile-based training. However, many workers feel that current training fails to meet expectations. By highlighting the statistic that 90% of employers concur on the advantages of mobile training, you strengthen the necessity for effective training solutions that can improve assurance processes.
-
Conduct Regular Audits: Schedule periodic audits of your control processes to pinpoint areas for improvement. This proactive approach facilitates timely interventions, addressing potential problems with quality control before they escalate into more significant issues. The necessity for such audits is highlighted by a case study titled 'Understanding and Impact of Tools,' which revealed that many respondents faced problems with quality control in their comprehension of tools, particularly among non-experts. Addressing this gap is essential for improving management practices and highlights the significance of effective training. As emphasized by endorsements from more than 650 brands that rely on OpsNinja's assurance services, routine inspections can uncover problems with quality control and significant supplier inconsistencies, assisting brands in preserving their product integrity.
-
Utilize Technology for Standards Control: Implement digital tools to streamline your standards control processes. Software solutions can assist in tracking performance metrics, managing documentation, and automating reporting, thereby simplifying the identification of trends and issues. The integration of technology in training has been recognized as a pivotal advancement, with 94% of workers indicating that development opportunities would enhance their retention in a role. By utilizing OpsNinja's inspection services, brands can receive comprehensive reports, including photos and videos, which offer actionable insights to protect standards. As one testimonial mentions, "OpsNinja's detailed reports assisted us in recognizing and correcting supplier discrepancies swiftly, which greatly enhanced our goods."
-
Engage with Suppliers: Foster open communication channels with suppliers to ensure they are fully aware of your standards expectations. Regularly assess their performance and provide constructive feedback to support continuous improvement in their processes. Such engagement is essential for maintaining standards throughout the supply chain, especially in overcoming problems with quality control, as evidenced by customer testimonials highlighting how OpsNinja's services have improved supplier accountability and product excellence.
-
Validate Procedures: Frequently examine and confirm your assessment protocols to guarantee their continued efficiency and applicability. This includes reassessing sampling plans and testing procedures to align with established industry standards and best practices. The significance of documentation in standards management cannot be overstated; it serves as the backbone of successful management and ensures that your team is equipped with the knowledge required to uphold excellence.
Implementing a Quality Management System (QMS)
Implementing a Quality Management System (QMS) is essential for enhancing control within your organization, especially when leveraging tailored support like that offered by OpsNinja. Here’s a structured approach to achieve this:
-
Define Your Standard Policy: Establish a clear standard policy that articulates your commitment to excellence and customer satisfaction.
This policy must be effectively communicated to all employees, ensuring everyone understands its importance in the organization’s operations. -
Set Standards Objectives: Identify specific, measurable goals that are directly related to improvement.
These objectives should align with your overall business goals.
Regular review of these objectives is crucial to ensure they remain relevant and achievable. -
Document Processes: Create comprehensive documentation for all assurance procedures, including detailed methods for testing, inspection, and corrective actions.
The availability of this documentation is essential; it should be easily accessible to all employees engaged in management. -
Assign Responsibilities: Clearly delineate roles and responsibilities for control within your organization.
Ensuring that every team member understands their specific contributions to upholding standards fosters accountability and ownership. -
Monitor and Measure Performance: Regularly track key metrics to assess the effectiveness of your QMS.
Using this data enables you to pinpoint areas for enhancement and make informed choices that positively influence product standards and client satisfaction.
OpsNinja’s dedicated support team exemplifies how personalized assistance can enhance these efforts, ensuring checks are tailored to the unique needs of your product. -
Continuous Improvement: Foster a culture of ongoing enhancement by promoting feedback from employees and clients alike.
Regularly revisiting and updating your QMS ensures that it remains adaptive to changing needs and regulations.
As Rahat Ahmed, Resource Management Growth Leader, emphasizes,Our specialist software streamlines all aspects of resource management,
illustrating the importance of integrating technology to enhance management processes.
Moreover, a Management System is crucial in helping organizations adapt to customer demands, as evidenced by the finding that 38% of organizations believe ERP enhances their ability to respond to these changing demands.
This adaptability is vital for maintaining competitive advantage in today's dynamic market, and it is also important to acknowledge the problems with quality control involved in QMS implementation, as highlighted by the study's mention of survivorship bias, where only successful implementations are reported, potentially skewing the understanding of QMS effectiveness.
Moreover, grasping the eight elements detailed in Model 5 can provide greater insights into the problems with quality control and other factors that organizations encounter when establishing a QMS.
When contrasting OpsNinja with rivals such as V-Trust, OpsNinja distinguishes itself with its tailored assessments that are specifically crafted for D2C brands, ensuring that the distinct characteristics of each item are considered.
This tailored approach contrasts with the more generic solutions often provided by competitors.
Investing in effective management practices, like those provided by OpsNinja, can yield significant benefits.
Their tailored inspections have proven to enhance product standards and reliability, as evidenced by the transformation of The Mindful Collective into a 7-figure business on Amazon.
Information from ASQ shows that firms concentrated on excellence encounter a 40% decrease in client complaints.
This underscores the critical role that a robust QMS plays in minimizing defects and enhancing overall customer satisfaction.
Leveraging Data Analytics for Quality Control
Utilizing data analytics can significantly enhance your control initiatives. Here’s how to utilize data effectively:
-
Collect Quality Information: Establish robust systems to gather comprehensive data on item standards throughout the supply chain.
This involves tracking defect rates, performing comprehensive inspections, and gathering customer feedback to obtain a complete perspective of performance. Attention should also be given to capturing data related to product design, construction, and shipping processes to ensure that all aspects of standards are addressed. -
Analyze Trends: Employ advanced analytical tools to scrutinize trends in your performance data.
Identifying patterns—such as recurring defects or inconsistencies from suppliers—can illuminate underlying issues that require attention. For example, brands such as Hash Stash have employed OpsNinja's specialized inspections to effectively assess and tackle issues, resulting in streamlined operations and enhanced client satisfaction. -
Predictive Analytics: Utilize predictive analytics to foresee possible issues before they emerge.
This proactive stance allows you to correct issues in advance, reducing risks before they affect customer satisfaction, as shown by Maurice Mann, who recovered $1 million in revenue after enhancing his product standards. -
Benchmarking: Regularly compare your performance metrics against industry standards or competitors.
This benchmarking process can uncover opportunities for improvement, empowering you to set ambitious yet attainable standards that enhance your competitive positioning. -
Reporting: Develop detailed reports that encapsulate performance metrics for stakeholders.
These reports should act not only as a summary but also as a basis for discussions around enhancement initiatives and monitoring progress over time. OpsNinja offers extensive reporting that assists brands in comprehending their performance and making data-driven decisions.
You can download sample reports by entering your email in the form provided on our website, allowing you to see firsthand the level of detail and insights available.
To set up OpsNinja's inspection services, simply connect with our team to discuss your specific needs.
We will assist you in creating a customized inspection strategy that fits your budget and excellence goals, guaranteeing that you consistently achieve high standards.
A relevant example of effective oversight through data analytics can be observed in the study titled 'Charts for Evaluation of Standards of Low-Dose-Rate Brachytherapy for Prostate Cancer.'
This case examination employed monitoring charts to assess treatment standards, illustrating how data analysis can result in enhanced outcomes.
As W. Edwards Deming wisely remarked, the unselective application of statistical inference can result in misleading conclusions unless you're sampling from a stable system.
Thus, continuous monitoring of key metrics is essential to ensuring that improvements are maintained and that defects do not recur.
Considering that subpar standards cost U.S. businesses an astounding $3.1 trillion annually, investing in a rigorous data-driven control strategy is not just beneficial—it’s essential.
Engaging Customers in Quality Assurance
Involving clients in quality assurance is pivotal for enhancing product quality and safeguarding your brand's reputation. Here are several effective strategies to implement:
- Solicit Feedback: Actively seek client input through surveys, reviews, and direct communication.
Research indicates that 81% of clients are motivated to make further purchases after a satisfactory service experience, underscoring the significance of understanding client sentiments. Significantly, service representatives only inquire about a client's name 21% of the time, emphasizing the necessity for greater personal involvement in gathering feedback. Each piece of feedback is a valuable resource; as Şeyma Beyazçiçek, a content writer at forms.app, states,
As long as you know how to listen to them, each piece of feedback carries importance since they all have personalized experiences.
-
Form a Client Advisory Board: Set up a committed group of loyal patrons who can offer insights and suggestions concerning item standards and possible enhancements. This initiative not only cultivates a sense of community but also enhances your brand's connection with its clients, aligns with OpsNinja's dedication to quality assurance, and helps D2C brands address problems with quality control to reduce negative experiences.
-
Incorporate Client Insights into Product Development: Utilize client feedback to guide product design and enhancements. This approach ensures that your offerings align with client expectations and adhere to high-quality standards. Moreover, with fewer than one-third of businesses offering self-service solutions, although 69% of clients try to resolve issues on their own, it’s essential to adjust feedback mechanisms to align with client preferences.
-
Communicate Changes: Regularly inform clients about adjustments made in response to their feedback. Openness in this process fosters trust and highlights your dedication to enhancement, a principle that OpsNinja exemplifies in their operations to prevent negative feedback and client dissatisfaction.
-
Reward Participation: Implement incentive programs for clients who share valuable feedback. Acknowledging their contributions promotes ongoing involvement and strengthens a culture of excellence. Investing in client service can result in substantial revenue growth; firms can possibly earn $700 million more after improving client experience.
By implementing these strategies, businesses can utilize client insights to drive considerable enhancements in product standards, ultimately resulting in increased satisfaction and loyalty. Discover how OpsNinja has positively impacted hundreds of brands by helping them scale and avoid negative customer reviews with our platform. See OpsNinja in Action and Contact Sales to learn more about our solutions.
Additionally, read our case studies on brands like Hash Stash and The Mindful Collective to see how OpsNinja has addressed their problems with quality control processes.
Conclusion
In navigating the complexities of quality control in manufacturing, organizations must confront a range of challenges that can undermine product integrity and operational efficiency. Key issues such as:
- Ineffective sampling plans
- Inadequate training
- Supplier quality problems
can lead to significant setbacks. However, by implementing:
- Comprehensive training programs
- Developing detailed documentation
- Leveraging technology
companies can establish a robust framework for quality assurance.
The integration of a Quality Management System (QMS) is pivotal for fostering a culture of continuous improvement. By:
- Defining clear quality policies
- Setting measurable objectives
- Regularly monitoring performance
organizations can ensure that their quality control processes remain effective and adaptive to changing demands. Furthermore, harnessing data analytics provides valuable insights into quality trends, enabling proactive interventions that mitigate risks and enhance product quality.
Engaging customers in the quality assurance process is equally vital. By soliciting feedback and incorporating customer insights into product development, businesses can strengthen their brand reputation and foster loyalty. The strategies outlined in this article demonstrate that prioritizing quality control not only safeguards a company’s reputation but also drives long-term success.
Ultimately, investing in quality management practices is not just about compliance; it is about building trust with customers and ensuring that products consistently meet the highest standards. By addressing quality control challenges head-on and embracing a proactive approach, organizations can position themselves for sustainable growth in an increasingly competitive market.