How to Determine AQL Chart Sample Size: A Step-by-Step Guide
Learn to determine AQL chart sample size for effective quality control and customer satisfaction.
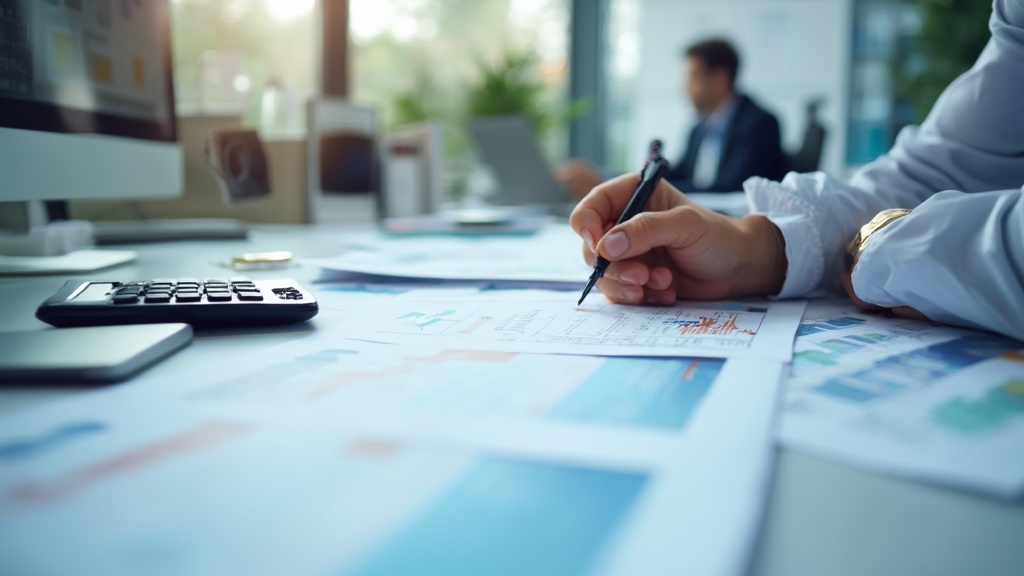
Introduction
In the realm of quality control, the Acceptable Quality Level (AQL) stands as a critical benchmark that shapes the standards of product excellence across various industries. This essential metric defines the maximum number of defects permissible within a batch, guiding manufacturers and quality inspectors in their quest for superior quality. As organizations strive to meet customer expectations and maintain a competitive edge, understanding AQL's nuances becomes paramount.
The implications of AQL extend beyond mere compliance; they encompass: - Enhanced customer satisfaction - Reduced costs associated with returns - The overall integrity of a brand's reputation
By exploring the intricacies of AQL, companies can adopt tailored strategies that not only mitigate risks but also drive significant improvements in their quality control processes.
Understanding Acceptable Quality Level (AQL) in Quality Control
The Acceptable Level of Excellence (AQL) is a pivotal component in control, defining the maximum allowable number of defective items within a sample batch. This benchmark serves as a crucial guideline for manufacturers and inspectors, determining whether a production lot complies with established standards. Importantly, AQL is not a one-size-fits-all metric; it varies by item and industry, determined by agreements between buyers and producers.
Movley's customized checklist assistance exemplifies this approach, as their excellence team collaborates closely with brands to suggest inspections specifically designed for unique items, enhancing the overall assurance process.
AQL is typically expressed as a percentage in an AQL chart sample size; for instance, an AQL of 2.5 indicates that out of a sample of 4000 items, no more than 10 defects are permissible. This understanding is especially crucial for D2C brands, as effectively managing AQL can significantly reduce defects, enhance customer satisfaction, and maintain a competitive advantage in a crowded marketplace. The success narratives of Amazon sellers, like Maurice Mann, who regained $1 million in revenue and enhanced his star rating from 3.5 to 4.7 through thorough inspections, highlight the practical significance of AQL and assurance measures.
Moreover, by following AQL standards, brands can witness a decrease in expenses related to product returns and rework, emphasizing the necessity of assurance practices. Recent advancements in standards for 2024 suggest a growing emphasis on tailored AQL levels, further highlighting the need for brands to stay informed on industry best practices and expert recommendations. Movley’s exceptional oversight system and skilled staff guarantee that brands can handle various suppliers efficiently and expand their operations.
They offer detailed inspection checklists for every component of an item, guaranteeing extensive standard management at all phases. Experts at QIMA provide valuable guidance on choosing appropriate inspection levels and AQL values for product inspections, ensuring that brands are equipped with the knowledge necessary to make informed decisions. For example, in a case study involving the inspection of 4000 face masks, the client selected a normal inspection level II and an AQL of 2.5, using a sampling calculation tool to determine the appropriate AQL chart sample size along with the acceptance number.
This practical use highlights the significance of AQL in real-world assurance situations. Additional case studies, including those related to Hash Stash and The Mindful Collective, further demonstrate how Money has revolutionized assurance processes and aided in substantial growth in their operations.
Step-by-Step Guide to Determining AQL Chart Sample Size
Establishing the AQL chart sample size is a crucial step in ensuring control. With Movley’s dedicated customer service team, you can follow this structured approach to establish an effective sampling process:
- Identify the Lot Size: Start by determining the total quantity of items in your production lot. This foundational step is vital, as it directly impacts the required AQL chart sample size for inspection.
- Select AQL Level: Choose your acceptable performance level (AQL) based on the nature of your product and industry standards. Common AQL levels include 0.65%, 1.0%, and 2.5%. It's essential to align your choice with customer expectations to maintain satisfaction and compliance. Remember, for AQL 2.5, no more than 10 units can fail the inspection, emphasizing the importance of adhering to this standard.
- Refer to AQL Tables: Utilize AQL sampling tables, which provide a clear reference for sample sizes corresponding to your lot size and selected AQL level. By locating the appropriate table, you’ll find the necessary sample size for both your lot size and the chosen AQL chart sample size.
- Calculate Sample Size: If your lot size is positioned between two values in the AQL chart sample size, round up to the nearest whole number. This ensures that your sampling is sufficient for a dependable assessment.
- Conduct Sampling: With your sample size determined, proceed to randomly select that number of items from your lot for inspection. An unbiased selection process is crucial to maintain the integrity of your assessment.
- Evaluate Results: After inspecting the selected items, assess the number of defects found against your AQL standard. If the defects surpass your acceptable level, this could require rejecting or reworking the entire lot to meet standards. It’s essential to recognize that grasping minor flaws—usually defined by an AQL standard of 4%—emphasizes the equilibrium between oversight and practical manufacturing circumstances. This approach enables importers to effectively manage standards while considering the implications of minor defects in their acceptance criteria.
- Peace of Mind with Money: By following these steps and utilizing Money’s top-tier inspections, you can create a strong assurance process that not only guarantees your products meet customer expectations but also safeguards your brand from unfavorable reviews and improves the overall customer experience. Remember, 60% of returns are due to avoidable problems, and 94% of customers steer clear of making a purchase because of a negative review. With Money, you can attain peace of mind knowing that your assurance measures are set up to prevent these issues.
Factors Influencing AQL Sample Size Determination
The determination of AQL sample size is influenced by several critical factors that brands must consider to ensure effective oversight:
-
Item Type: The complexity and risk associated with defects vary significantly across item categories. For instance, electronic components often necessitate a stricter AQL compared to textiles due to their intricate nature and potential impact on functionality. Movley's tailored checklist support ensures that your assessment team recommends specific checks based on the unique characteristics of your product, minimizing the risk of manufacturing defects.
-
Production Process: The reliability and stability of the production process are pivotal. A consistently well-controlled manufacturing environment may permit a higher AQL, as the likelihood of defects is mitigated by robust process controls. As Avijit Hazra, MD at the Institute of Postgraduate Medical Education & Research, notes,
The margin of error depends on the aql chart sample size and variability of the sample,
underscoring that a stable process can yield more predictable outcomes. Movley’s on-site inspections are intended to identify issues early, preventing them from impacting customer experience. -
Customer Expectations: Understanding customer standards is essential in shaping AQL decisions. Luxury brands, for instance, frequently follow lower AQL levels to match their dedication to exceptional standards and customer satisfaction. By utilizing Movley’s top-tier inspections, brands can safeguard themselves from unfavorable reviews that arise from standard issues.
-
Regulatory Requirements: In specific sectors, strict regulations oversee assurance standards, which can determine acceptable AQL levels. Adhering to these regulations is essential for brands to evade legal consequences and uphold market credibility.
-
Historical Data: Utilizing historical defect rates allows brands to establish realistic and attainable performance targets. For example, it is theorized that approximately 1.03751% or 109 bars out of 10,500 may fall within the out of spec category, illustrating the importance of accurate data in determining AQL levels. Through examining previous performance, organizations can make knowledgeable modifications to their AQL strategies, thus improving their oversight measures. Integrating these elements into AQL strategies enables brands to customize their methods to meet market needs efficiently while ensuring customer satisfaction. The case study titled 'Estimating Sample Size for Defective Product' emphasizes the complexity of determining aql chart sample size and the necessity of collaboration with a statistician or academic expert for customized guidance. Additionally, referencing the article 'Level of Quality for Minimum Cost of Manufacture of a Specification' highlights the broader implications of AQL in manufacturing processes. By incorporating on-site inspections and utilizing historical information, brands can further improve their standards management efforts.
Common Mistakes to Avoid When Determining AQL Sample Size
When determining the AQL sample size, it’s crucial to be aware of these prevalent mistakes that can undermine your control efforts:
- Ignoring Lot Size Variability: Overlooking variations in lot size can result in inadequate sampling, ultimately compromising the precision of assessments. Recognizing this variability is essential for effective management of standards. With Movley's tailored assessments, your sampling reflects the true diversity within your lots, ensuring confidence in evaluations.
- Choosing an Inappropriate AQL Level: Setting an AQL level that is either too lenient or overly strict can lead to significant issues or inflate costs unnecessarily. It’s vital to tailor the AQL level to the specific characteristics of your item, ensuring that it aligns with industry standards and customer expectations. Movley's assurance team collaborates with you to set suitable AQL levels that genuinely represent your item's requirements.
- Neglecting Random Sampling Methods: Relying on biased sampling techniques can distort results and misrepresent the standard of the entire lot. Implementing robust random sampling methods is essential for obtaining a true representation of product excellence. With Movley’s best-in-class inspections, you can trust that assessments are based on sound methodologies.
- Overlooking Documentation: Failing to properly document your AQL processes and results can create inconsistencies and complicate audits. Thorough documentation is essential for upholding transparency and responsibility in assurance practices. Movley emphasizes thorough documentation to support your assurance efforts.
- Not Reviewing Historical Data: Ignoring historical defect data can lead to unrealistic AQL settings that don’t reflect actual performance levels. Historical analysis is critical in establishing informed and effective thresholds for the AQL chart sample size. For example, by establishing job failure notifications, as outlined in the case study on maintenance, D2C brands can boost responsiveness and enhance overall standards of oversight processes.
By tackling these frequent errors, D2C brands can improve their oversight protocols, reduce risks, and strengthen a commitment to excellence in item standards—ensuring that their items consistently meet customer expectations and safeguard their brand reputation. Remember, according to Return Logic, 60% of returns are due to avoidable issues, making it essential to catch these early with Movley’s tailored checklist support and on-site inspections.
Implementing AQL in Your Quality Control Process
Successfully applying Acceptable Quality Level (AQL) in your assurance process is crucial for guaranteeing item excellence and customer contentment. Here are key steps to consider:
-
Train Your Team: It is essential that your quality control team fully comprehends AQL concepts and their role in upholding high standards.
Proper training can significantly enhance the team's effectiveness in identifying defects, which is vital in preventing potential bad batches from reaching customers. -
Integrate AQL into Your Management System: Update your management processes to incorporate AQL standards. This will guarantee uniformity across all offerings, aligning operational methods with standards.
Utilizing Movley's tailored teams and high-touch service can further enhance this integration. -
Regularly Review AQL Levels: Periodically assess your AQL levels and the AQL chart sample size to effectively respond to changes in production processes, customer feedback, and market demands. For example, common AQL levels in the garment industry are set at:
- 2.5% for general apparel
- 1.5% for critical items
- 1.0% for high-end or safety-critical items
Regular reviews can help you adapt to evolving standards, thus maintaining product integrity and minimizing returns that could arise from defects: - 20% due to damaged products
- 22% from items looking different than expected
-
23% from receiving the wrong item
-
Conduct Regular Audits: Implementing regular evaluations of your assurance processes is vital for ensuring compliance with AQL standards, including the determination of the AQL chart sample size.
These audits will help identify areas for improvement and reinforce a culture of continuous enhancement.
They also serve to ensure excellence and reliability of your suppliers, reducing risk significantly. -
Utilize Technology: Leverage the latest technology in management systems to streamline your assurance process.
Digital tools can facilitate tracking of defects and sampling results, thereby enhancing efficiency and accuracy in inspections.
Movley's contemporary control platform can assist in this regard, providing top-tier inspections to prevent manufacturing problems before they impact your customers.
By incorporating AQL into your control procedures, you not only enhance item standards but also decrease defects, contributing to better customer satisfaction.
As a quality management expert noted, after completing the AQL inspection, the inspection agency will issue a shipment inspection certificate, underscoring the importance of adhering to established quality standards.
A case study titled 'Acceptable Quality Level (AQL) in the Garment Industry' illustrates the effective application of AQL and its outcomes, reinforcing its significance in maintaining customer satisfaction and protecting your brand reputation against negative reviews.
Moreover, utilizing Movley's inspections can prevent up to 60% of returns, ensuring that your customers receive only the best products.
Conclusion
Implementing an effective Acceptable Quality Level (AQL) strategy is vital for organizations striving to enhance their quality control processes and meet customer expectations. By understanding the nuances of AQL, brands can determine the appropriate levels that resonate with their specific product types, production processes, and customer demands. This tailored approach not only minimizes defects but also fosters heightened customer satisfaction and loyalty.
Moreover, the insights shared throughout the article underscore the importance of avoiding common pitfalls in AQL determination. By recognizing the impact of lot size variability, selecting appropriate AQL levels, and employing random sampling methods, companies can safeguard their quality assurance efforts. Regular audits and the integration of advanced technology further reinforce a culture of continuous improvement, essential for maintaining a competitive edge in today’s fast-paced market.
Ultimately, the commitment to quality through AQL practices not only protects a brand's reputation but also reduces costs associated with returns and rework. As organizations continue to adopt and refine these strategies, they will not only meet but exceed customer expectations, ensuring long-term success and sustainability in their respective industries.