Best Practices for Quality Assurance in Manufacturing: Proven Strategies for Success
Explore best practices for quality assurance manufacturing and proven strategies for success.
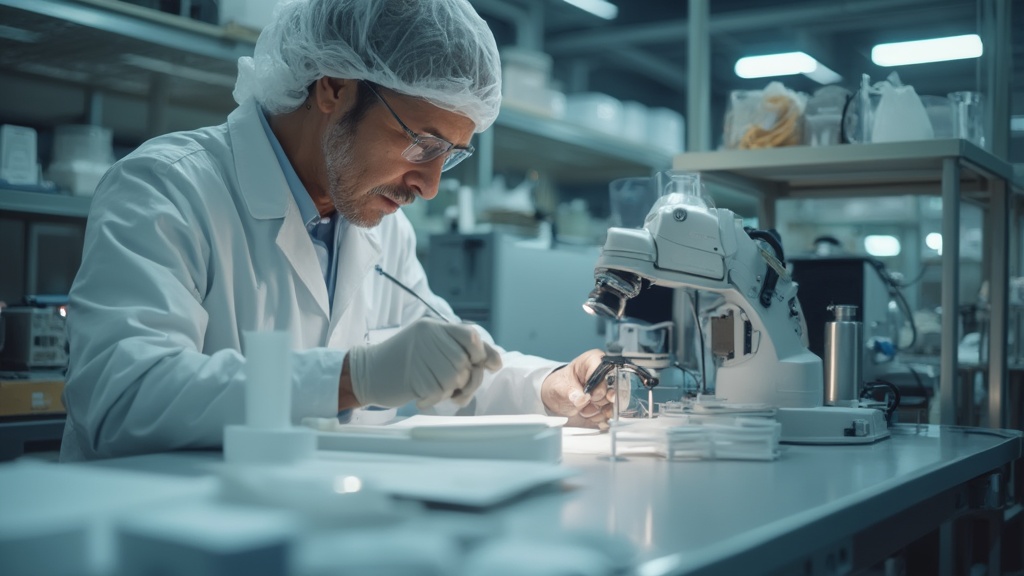
Key Highlights:
- Quality assurance manufacturing ensures products meet quality standards before reaching consumers, enhancing customer satisfaction.
- Key components of QA include monitoring production processes, inspecting raw materials, and testing finished products.
- A robust QA framework prevents defects and reduces variability, which is crucial for operational efficiency and brand reputation.
- Effective QA practices can lead to significant cost savings by preventing recalls and ensuring compliance with industry regulations.
- Strategies for implementing QA include establishing clear standards, integrating quality control into production, and utilizing technology for standards management.
- Training employees on quality practices and conducting regular audits are essential for maintaining high standards.
- Continuous improvement methodologies like Lean and Six Sigma help manufacturers enhance processes and product quality.
- Data analytics, including real-time and predictive analytics, plays a critical role in optimizing quality assurance and supply chain management.
- Engaging employees in QA initiatives fosters a culture of excellence and improves operational performance.
- Supplier quality management is vital for ensuring materials meet standards, involving clear communication, audits, and collaborative relationships.
Introduction
In the competitive landscape of manufacturing, quality assurance (QA) stands as a pivotal element that can make or break a brand's reputation. As consumer expectations shift towards higher-quality and sustainable products, manufacturers are called to adopt robust QA practices that not only ensure compliance with industry standards but also enhance customer satisfaction.
OpsNinja is leading the charge in transforming QA for direct-to-consumer brands, showcasing how strategic oversight and innovative solutions can drive operational efficiency and mitigate risks.
By exploring the intricacies of QA—from establishing clear standards to leveraging data analytics—this article delves into proven strategies that empower manufacturers to maintain excellence in their production processes. The focus on continuous improvement and employee engagement further underscores the importance of a holistic approach to quality management, ensuring that organizations are well-equipped to thrive in an ever-evolving market.
Understanding Quality Assurance in Manufacturing
Quality assurance manufacturing is an essential systematic approach designed to ensure that products meet established quality standards before they reach consumers. The company is at the forefront of revolutionizing QA for direct-to-consumer (D2C) brands, recognizing the shifting consumer demand towards higher-quality and sustainable products. This multifaceted process includes:
- Monitoring production processes
- Inspecting raw materials
- Rigorously testing finished products
The primary objective of QA is to prevent defects, minimize variability, and enhance overall operational efficiency. For manufacturers, a robust quality assurance manufacturing framework is not merely a regulatory requirement; it is a strategic imperative that significantly enhances customer satisfaction by ensuring reliable products and preventing negative customer reviews. The innovative solutions from the company, including comprehensive inspections and audits, have assisted brands like The Mindful Collective scale on Amazon and facilitated Amazon seller Maurice Mann in recovering $1 million in revenue by boosting product ratings from 3.5 to 4.7 stars.
Furthermore, by preventing costly recalls and rework, effective QA practices contribute to substantial cost savings. Compliance with industry standards and regulations, such as ISO certifications, is also vital, profoundly influencing a brand's reputation and competitive edge in the market. As noted in the 2024 Fortune/Deloitte CEO survey, regulations and taxes are among the top factors that could impact businesses, underscoring the importance of QA amidst potential trade policy changes.
Additionally, investment in clean technology manufacturing has continued to decline since 2023, highlighting the necessity of maintaining high standards of quality assurance manufacturing in a shifting market. Looking ahead to 2025, as outlined in the case study titled 'Future Outlook for US Manufacturing,' manufacturers will navigate a challenging business climate influenced by higher costs and economic uncertainties, further emphasizing the critical role of quality assurance manufacturing in sustaining market viability and customer trust. OpsNinja's comprehensive oversight of inspections for a brand group's entire portfolio ensures that management is consistently upheld across all products, reinforcing the significance of assurance in today’s retail economy.
Proven Strategies for Effective Quality Assurance Implementation
Implementing quality assurance manufacturing requires a strategic approach. Here are several proven strategies to consider:
-
Establish Clear Standards for Excellence: Defining excellence for your products is essential. Establish measurable standards that reflect customer expectations and comply with regulatory requirements. Involving stakeholders in this initiative promotes alignment and dedication, guaranteeing that everyone shares a common understanding of objectives.
-
Integrate Quality Control into the Production Process: Quality control should be embedded throughout the production cycle rather than treated as an endpoint. Utilizing real-time monitoring and testing allows manufacturers to identify defects early. For example, statistical control (SPC) can assist in identifying variations before they develop into major problems, thus improving overall product excellence.
-
Utilize Technology for Standards Management: The adoption of digital tools and software can significantly streamline standards management processes. Advanced platforms equipped with real-time data analytics enable manufacturers to monitor performance metrics effectively, facilitating informed decision-making that aligns with best practices. Blockchain technology, for instance, offers an immutable, decentralized ledger for transactions, ensuring transparency and security across various supply chain operations. This improves management by providing traceability and accountability in the supply chain. As Satarupa Chatterjee, Senior Director of Product Marketing, stated, "Meet the First Contact Center LLM and Observe.AI’s New Generative AI Suite," emphasizing the significance of AI technologies in improving management. A significant trend is the growing dependence on AI technologies, as shown by the 41% of contact centers adopting assurance automation to improve their processes.
-
Train Employees on Quality Practices: Investing in comprehensive training programs is crucial. By educating employees on standards of excellence, inspection methods, and their essential roles in sustaining standards, companies can cultivate a knowledgeable workforce. This not only enhances adherence to standards but also nurtures a culture of accountability within the organization.
-
Conduct Regular Audits and Reviews: Consistent evaluations and audits of assurance processes are fundamental for continuous improvement. These evaluations assist in recognizing areas for improvement and enable the execution of corrective measures based on audit findings, ensuring that management practices develop in line with industry standards. The comprehensive inspection reports from the service play a critical role here, providing detailed insights, including photos and videos, so brands can act on the results and protect themselves from negative reviews.
-
Engage with Suppliers: Quality assurance manufacturing extends beyond just the manufacturing facility itself. Working together with suppliers is essential to guarantee that incoming materials meet set standards. By establishing robust connections with suppliers and using OpsNinja's inspection services, manufacturers can improve the overall standard and dependability of their production methods. Companies that actively engage in these practices are well-positioned to reduce customer complaints significantly—reportedly by 40%—leading to higher customer satisfaction and retention. Additionally, numerous contact centers are embracing AI technologies to improve their management systems, with a substantial need for leaders to incorporate or substitute these technologies to enhance QM systems.
The Role of Continuous Improvement in Quality Assurance
Ongoing enhancement in quality assurance manufacturing is vital for manufacturers seeking to refine their methods and improve product quality systematically. By employing structured methodologies like Lean and Six Sigma, organizations can implement effective continuous improvement initiatives, as demonstrated by successful D2C brands using OpsNinja's services.
-
Lean Manufacturing: This methodology minimizes waste while maximizing productivity across manufacturing systems. It encourages identifying non-value-adding activities, streamlining processes to achieve greater efficiency. Remarkably, brands that have embraced Lean principles report considerable enhancements in their operations, as evidenced by The Mindful Collective, which transformed its control approach and experienced substantial growth on Amazon.
-
Six Sigma: This data-driven approach minimizes defects and enhances overall excellence through statistical methods. Organizations that apply Six Sigma principles frequently observe significant improvements in their control processes. For instance, Maurice Mann, an Amazon seller, utilized OpsNinja's inspections to boost his ratings from 3.5 to 4.7 stars, recovering $1 million in revenue as a direct result.
-
Feedback Loops: Actively seeking feedback from employees, customers, and suppliers is essential in identifying issues and opportunities for improvement. Constructive feedback can lead to actionable insights, driving significant enhancements. Blair Epstein highlights that 'feedback is the cornerstone of effective change,' a principle that Hash Stash adopted to enhance its control measures.
-
Celebrate Successes: Recognizing and celebrating enhancements in standards can significantly motivate teams and reinforce the importance of assurance within the organization. Acknowledging accomplishments promotes a culture of ongoing enhancement, as shown by the successes shared by different OpsNinja clients, including Neil Ayton, who has effectively managed diverse suppliers and established control processes for his portfolio of e-commerce brands.
-
Case Study Reference: The examination of participation programs emphasizes how structured feedback mechanisms—such as individual suggestion systems and semi-autonomous groups—can improve assurance. The findings from this study reveal that effective implementation of participation programs contributes to economic performance and strengthens employee commitment and well-being.
By incorporating continuous improvement practices into their quality assurance manufacturing processes, manufacturers can adapt to evolving market demands, enhance product standards, and maintain a competitive edge, as demonstrated by the transformative effects of OpsNinja's inspections across various D2C brands, which consistently experience higher growth and lower returns.
Utilizing Data Analytics for Quality Assurance Insights
In today's manufacturing environment, utilizing eCommerce analytics has become an essential part of quality assurance manufacturing and optimizing supply chain management for D2C brands. By harnessing the power of data analytics, manufacturers can unlock insights that lead to superior outcomes in quality assurance manufacturing and improved customer satisfaction. Here are several key strategies for effectively utilizing data analytics in manufacturing:
- Real-Time Monitoring: The integration of sensors and IoT devices enables manufacturers to collect real-time data during the production phase. By utilizing eCommerce analytics, brands can identify trends in customer behavior and product performance, facilitating swift corrective actions. Moreover, edge computing plays a vital role in this process by processing data close to the equipment, thereby reducing latency issues associated with traditional cloud systems.
Research indicates that 57% of businesses have reported increased effectiveness in decision-making through such real-time analytics.
- Predictive Analytics: By utilizing historical data and incorporating comprehensive reports from inspection services like OpsNinja, manufacturers can anticipate potential problems before they occur. These detailed reports provide actionable insights that can help brands proactively address areas of concern, thereby protecting their reputation and minimizing negative reviews.
Predictive analytics not only aids in anticipating equipment failures but also supports proactive maintenance strategies, significantly minimizing downtime. A noteworthy case study involving SPD Technology illustrates these benefits, where the company sought to automate paperwork and invoice processing using machine learning. This initiative resulted in a dramatic reduction in data aggregation time from weeks to mere hours and fully automated invoice processing, aligning closely with the company’s operational objectives and enhancing overall efficiency.
-
Trend Analysis: Examining data trends over time, particularly via eCommerce analytics, assists manufacturers in assessing the effectiveness of their quality assurance manufacturing initiatives. By understanding these trends, organizations can refine their strategies, ensuring continuous improvement in product standards and protecting their brand from negative reviews. Recent insights from industry leaders like IBM and Microsoft indicate that 54% of companies are contemplating the adoption of cloud and business intelligence (BI) tools for improved data analytics, illustrating a wider trend towards integrating advanced technologies in management.
-
Performance Dashboards: Creating intuitive dashboards that visualize essential metrics can drive immediate insights into performance. These dashboards, improved by comprehensive reporting from inspection activities, enable teams to make rapid, data-informed decisions, positioning quality assurance manufacturing as a dynamic element of the manufacturing workflow. Specific features of eCommerce analytics, such as automated reporting and real-time alerts, can significantly aid in this process, ensuring that teams are always informed and ready to act.
With the advent of AI reshaping the manufacturing sector by automating tasks and optimizing production, the role of data analytics becomes increasingly vital.
By shifting from a reactive to a proactive management approach, manufacturers can significantly improve product standards and boost customer satisfaction, ensuring that every inspection aligns with customized recommendations from the operations team.
Engaging Employees in Quality Assurance Initiatives
Involving staff in assurance initiatives is vital for developing a strong culture of excellence within an organization. Here are several strategies to effectively engage staff while utilizing OpsNinja's dedicated support team, recognized for its excellent customer assistance:
-
Create a High-Standard Team: Establish cross-functional teams dedicated to addressing excellence issues and initiatives. This method not only promotes teamwork but also enables staff by providing them a stake in the effective results. With OpsNinja's dedicated support team readily available for expert guidance and assistance, organizations can effectively tackle challenges related to standards. A Harvard Business Review study highlights that 71% of executives recognize staff engagement as vital for organizational success, indicating that when individuals are involved, the outcomes are often superior.
-
Solicit Ideas and Feedback: Actively encourage staff to offer their suggestions for improving standards. Implementing suggestion programs that reward innovative contributions can lead to measurable improvements in quality. The presence of OpsNinja's dedicated support team can facilitate this process by providing resources, feedback mechanisms, and direct assistance in implementing staff suggestions. According to Gallup, organizations that score in the top 20% for engagement experience up to 59% less turnover, suggesting that engaged staff are more likely to share valuable insights.
-
Provide Training and Resources: Equip your workforce with the necessary tools and knowledge to prioritize excellence. Providing thorough training on standards, inspection methods, and problem-solving abilities, backed by OpsNinja's expert assistance, improves staff capabilities and strengthens their dedication to improvement initiatives. The dedicated support team can also provide ongoing assistance and resources to ensure that individuals feel confident in their roles.
-
Acknowledge Efforts: Honoring staff contributions in sustaining and enhancing standards is essential. Acknowledgment acts as a strong motivator, cultivating an environment where assurance is appreciated and prioritized. High levels of staff engagement correlate with better customer service and effective communication, further contributing to organizational success. OpsNinja's dedicated support team can help highlight and promote these contributions, ensuring that employees feel appreciated.
-
Consider Patient Demographics: When executing enhancement initiatives, it is important to consider the demographics of the patient population served. Tailoring effective strategies to meet the diverse needs of patients can enhance the effectiveness of these initiatives and ensure better outcomes. The support team can provide insights and data to help organizations understand these demographics better.
-
Flexible Work Arrangements: Implementing flexible work arrangements can significantly enhance satisfaction and engagement among staff. By permitting customized work schedules and locations, organizations can foster an environment that promotes individuals' work-life balance, further strengthening their dedication to excellence assurance. OpsNinja's dedicated support team can assist in developing these arrangements to ensure they align with objectives.
By actively involving employees in quality assurance manufacturing initiatives, supported by OpsNinja's dedicated team and their amazing customer support, manufacturers can establish a solid foundation for sustained improvements. This not only enhances operational performance but also cultivates a culture that prioritizes excellence, ultimately benefiting the organization as a whole.
The Importance of Supplier Quality Management
Efficient supplier standard management is essential for ensuring that all materials meet set criteria before entering the manufacturing stage. Here are several best practices designed to optimize supplier quality:
-
Establish Clear Standards: Clearly communicate performance standards and expectations to suppliers. This not only ensures they understand the requirements for materials and components but also sets the foundation for accountability. For instance, the collaboration between The Mindful Collective and the team transformed their initial doubts regarding inspections into a strong control process that notably boosted their Amazon growth, highlighting the beneficial influence the team has had across various brands.
-
Conduct Comprehensive Supplier Audits: Regular supplier audits are essential for assessing compliance with management practices. OpsNinja's thorough audits have assisted brands such as Caddent Golf in identifying areas for enhancement while ensuring adherence to established standards. Gartner research emphasizes that leveraging in-depth proprietary studies and best practices in supplier audits enables organizations to drive stronger, sustainable business performance. Moreover, monitoring the cost of poor supplier performance helps prevent expensive mistakes, underscoring the financial implications of inadequate supplier management.
-
Foster Collaborative Relationships: Developing robust, collaborative relationships with suppliers is vital. Consistent communication and constructive feedback and the prompt and effective resolution of issues ultimately enhance product reliability. Entrepreneur Neil Ayton underscores how overseeing varied suppliers resulted in enhanced control procedures throughout his portfolio, including Karma Heart and Luminate Press, stressing the significance of cooperation in attaining excellence.
-
Implement Rigorous Incoming Standards Control: Establish thorough processes for inspecting and testing incoming materials to verify compliance with standards before they are utilized in production. This step is critical in preventing defects that could compromise the final product's integrity. OpsNinja's on-site inspections have been crucial in assisting sellers like Maurice Mann regain $1 million in revenue by enhancing product ratings from 3.5 to 4.7 stars, showcasing the significance of thorough incoming standards.
Furthermore, the evolving landscape of supply chain management highlights a growing focus on transparency and sustainability, influenced by both customer and regulatory demands. A case study titled 'The Evolving Landscape of Supply Chain Management' illustrates how supplier performance metrics are expanding to include sustainability indicators and ethical sourcing practices. Moreover, using digital tools enables manufacturers to merge supplier data, visualize performance trends, create reports, and work with suppliers to enhance standards.
By prioritizing supplier quality management, manufacturers not only enhance their overall quality assurance manufacturing efforts but also strengthen their product reliability in a competitive market, reflecting the strategies employed by OpsNinja across various brands.
Conclusion
In the realm of manufacturing, quality assurance is not just a regulatory checkbox; it is a strategic cornerstone that shapes brand reputation and customer loyalty. The insights provided throughout this article emphasize the necessity of implementing robust QA practices, particularly in light of evolving consumer expectations for higher-quality and sustainable products. OpsNinja exemplifies how comprehensive quality management—from establishing clear standards to leveraging advanced data analytics—can drive operational excellence and mitigate risks.
The proven strategies outlined, including:
- Integrating quality control into the production process
- Engaging employees in quality initiatives
highlight the importance of a holistic approach. Continuous improvement methodologies, such as Lean and Six Sigma, further illustrate how manufacturers can adapt to changing market dynamics while enhancing product quality. By fostering collaboration with suppliers and investing in technology, organizations can ensure that quality is maintained throughout the supply chain, thus safeguarding their reputation and bottom line.
Ultimately, as the manufacturing landscape continues to evolve, embracing a culture of quality assurance becomes imperative for sustained success. By prioritizing quality management practices, manufacturers not only enhance customer satisfaction but also position themselves competitively in an ever-changing market. The commitment to excellence in quality assurance will undoubtedly yield long-term benefits, reinforcing the critical role it plays in today's retail economy.