Best Practices for Effective Factory Monitoring: Tips from Industry Experts
Discover essential strategies for effective factory monitoring to enhance productivity and quality.
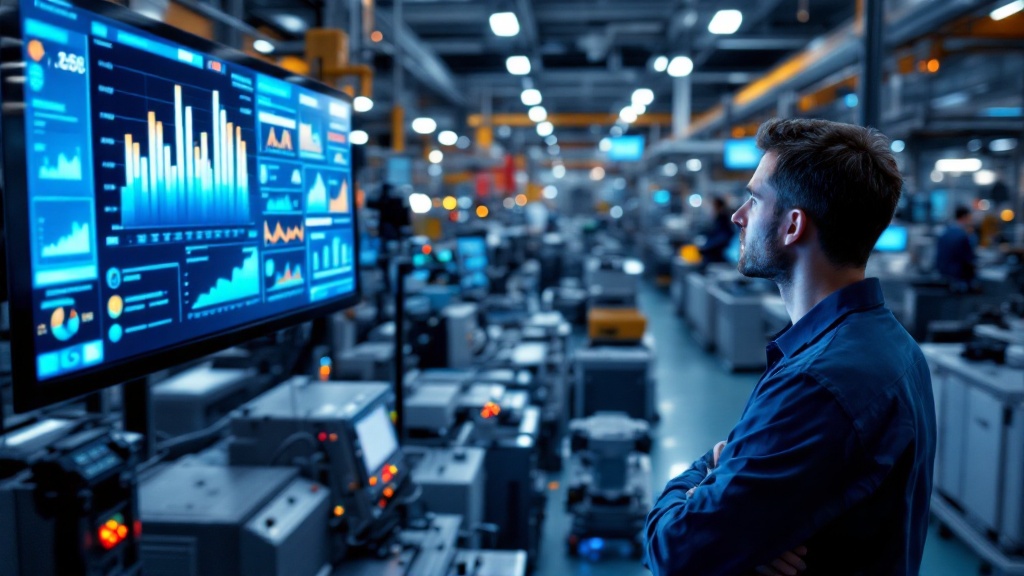
Introduction
In the rapidly evolving landscape of manufacturing, the integration of Artificial Intelligence (AI) and real-time data analytics is transforming how factories operate, paving the way for enhanced sustainability and efficiency. As organizations grapple with increasing demands for quality and performance, AI emerges as a vital ally, enabling proactive monitoring and predictive maintenance that not only minimizes downtime but also significantly reduces the risk of quality-related returns.
With a staggering 60% of product returns attributed to preventable quality issues, the need for robust monitoring systems has never been more critical. This article delves into the essential components of effective factory monitoring, highlighting practical strategies and technological advancements that empower manufacturers to optimize operations, safeguard their reputations, and thrive in an increasingly competitive market.
As the industry embraces these innovations, understanding the nuances of effective monitoring practices will be key to unlocking the full potential of modern manufacturing.
Leveraging AI for Sustainable Factory Monitoring
Artificial Intelligence (AI) is revolutionizing the landscape of factory monitoring, serving as a critical tool for enhancing sustainable operational efficiency. With the capability to process and analyze extensive datasets in real time, AI algorithms identify inefficiencies and problems proactively, preventing them from escalating. Complementing this technology, the on-site inspections play a pivotal role in ensuring standards by preventing bad batches and minimizing returns.
According to Return Logic, 60% of returns are caused by avoidable issues, which the company helps identify early through these inspections. Predictive maintenance, an application of AI, exemplifies this by forecasting equipment failures, allowing manufacturers to perform timely repairs and significantly minimize downtime. A notable example is Siemens, which has integrated AI systems resulting in not only improved operational efficiency but also a remarkable reduction in energy consumption through optimized machinery performance.
As we look toward 2024, the latest data indicates that global AI chip revenue is projected to reach $83.25 billion by 2027, underscoring the growing investment in AI technologies. Furthermore, the White House's Executive Order released in October 2023 sets new benchmarks for AI safety and security, in harmony with the company's dedication to assurance and responsible technology adoption. For brands seeking to improve their sustainability initiatives, implementing proactive control measures alongside factory monitoring solutions driven by AI is essential.
This integration fosters smarter decision-making and reinforces sustainable practices, positioning companies to thrive in an increasingly competitive market where:
- 94% of customers have avoided making a purchase due to a bad review
- 83% of workers report that AI has made their work more enjoyable
The Importance of Real-Time Data in Factory Operations
In the current landscape of manufacturing, factory monitoring for accessing real-time data is essential. This prompt insight enables managers to efficiently oversee production lines and maintain strict control standards through factory monitoring and inventory level control. Leveraging the integrated platform, which directly connects to your storefront, can significantly enhance inspection tracking, alerting users to quantity discrepancies and ensuring operational efficiency.
Smart manufacturing is emerging as a transformative approach in the industrial landscape, utilizing advanced technologies like IoT sensors to optimize these processes. For instance, organizations implementing IoT sensors are equipped to receive instant alerts regarding machine performance anomalies, enabling swift corrective measures that avert costly production delays. As the sensors market continues its robust growth—projected to rise from $251.29 billion in 2022 to $360.61 billion by 2027—it’s clear that the demand for such technologies is on the rise.
According to Deloitte's 2025 Manufacturing Industry Outlook, key trends such as AI investments and supply chain agility are shaping the future of manufacturing, emphasizing the importance of real-time data in adapting to an uncertain business environment. Moreover, with Movley’s on-site inspections, brands can prevent up to 60% of returns related to quality issues, as 60% of returns are due to preventable quality issues, and protect their reputation, as 94% of customers avoid purchases due to bad reviews. To capitalize on real-time data effectively, it’s crucial to invest in factory monitoring systems that offer integrated observation with comprehensive dashboards displaying key performance metrics and alerts.
This ensures decision-makers are always informed, positioning their operations to adapt swiftly within the evolving manufacturing environment. As noted by industry expert Diane Harvey,
Data-driven decisions are faster and more effective,
underscoring the imperative for manufacturers to embrace these advancements to enhance operational efficiency and productivity.
Quick Wins for Enhancing Factory Monitoring
Improving factory monitoring does not necessitate a complete overhaul of existing systems; instead, several quick wins can lead to remarkable enhancements in performance. Begin with a straightforward audit of your current monitoring practices to pinpoint any gaps that may exist. Following this, equipping all machinery with basic sensors designed to track key performance indicators (KPIs) is essential.
These sensors are crucial for factory monitoring, as they gather real-time data that informs decision-making. Conducting on-site inspections, as suggested by Movley, can prevent up to 60% of returns caused by defects, thereby safeguarding your brand reputation and improving customer satisfaction. In fact, 94% of customers have avoided making a purchase due to a bad review, highlighting the importance of maintaining high quality standards.
Furthermore, 27% of predictive maintenance adopters reported amortization in under a year, highlighting the financial advantages of such practices. Establishing a routine for factory monitoring meetings allows team members to collaboratively analyze performance insights and identify areas for improvement. Furthermore, small changes—such as optimizing workflow layouts and enhancing communication channels between teams—can deliver immediate benefits in operational efficiency.
These foundational steps set the stage for a more robust manufacturing strategy, accelerating your transition into Industry 4.0. As PwC estimates, the potential contribution of automation and AI to the global economy is a massive $15.7 trillion by 2030, underscoring the importance of adopting advanced oversight practices. A real-world example can be seen in Arundo's Marathon, which features prescriptive actions that suggest optimal responses to potential failures, providing workflows and instructions to resolve equipment problems according to corporate standards.
Such improvements not only enhance factory monitoring but also drive effective resolutions of equipment issues, further ensuring a seamless operation. With Movley, your team can focus on building the business rather than dealing with operational complaints, ultimately leading to greater peace of mind.
Essential Features of Effective Factory Monitoring Systems
When evaluating factory monitoring systems, several key features should be at the forefront of your selection process. Prioritize systems that facilitate real-time data analytics and factory monitoring, as this capability provides immediate insights into production performance, enabling timely decision-making and minimizing preventable quality problems that could lead to returns. A user-friendly interface and customizable dashboards are equally important, ensuring that operators can interact with the system efficiently and tailor the display of information to meet specific needs.
Integration capabilities play a crucial role in establishing seamless data flow across departments and tools, fostering collaboration and enhancing operational visibility, which is essential for factory monitoring and protecting your brand reputation. Furthermore, systems that alert users to deviations from established norms are invaluable for proactive factory monitoring and management of potential issues. This approach aligns with the insights from MachineMetrics, which emphasizes that real-time condition assessment is also an excellent way to move from preventive to condition-based or predictive maintenance strategies, further reducing waste and costs. Such features are essential to Manufacturing Execution Systems (MES), which have developed considerably, with recent advancements in factory monitoring making them crucial tools for comprehensive production insights and control, thereby preventing poor batches and returns, and ensuring customer satisfaction.
Notably, the on-premises segment accounted for over 71% of revenue share in 2023, highlighting the demand for strong oversight systems. The transformative impact of effective quality control is exemplified by Movley's partnership with The Mindful Collective, which helped them grow to a 7-figure business on Amazon by enhancing their quality assurance processes. Recent innovations, such as Henkel AG & Co. KGaA's introduction of smart pipes and tanks leak detection, highlight the importance of factory monitoring and the adoption of cutting-edge technologies in manufacturing.
As highlighted in a case study on infrastructure oversight, the wired segment dominated the market in 2023 due to its reliability, while the wireless segment is the fastest-growing, offering flexibility and real-time tracking capabilities. This evolution in observation technologies illustrates the practical applications and benefits of factory monitoring, which can enhance asset performance and reduce downtime in manufacturing settings. According to Deloitte’s 2025 Manufacturing Industry Outlook, the emphasis on talent management and AI investments underscores the necessity of leveraging these technologies to maintain competitive advantage.
Furthermore, it is essential to acknowledge that 94% of customers have refrained from making a purchase because of a negative review, emphasizing the necessity for effective control measures. As the manufacturing landscape continues to evolve, the importance of adopting effective oversight systems for factory monitoring that incorporate these essential features cannot be overstated. Furthermore, on-site inspections are essential in identifying preventable issues early, offering peace of mind and ensuring that your brand reputation stays intact.
Maximizing Productivity Through Effective Monitoring Practices
Enhancing productivity in a factory environment is fundamentally linked to the application of effective oversight practices through factory monitoring and proactive quality control measures. Organizations that utilize comprehensive oversight methods in conjunction with factory monitoring and on-site inspections frequently witness significant improvements in output, fueled by better resource distribution and reduced machine downtime. In fact, engaged employees—those who feel supported rather than surveilled—can boost profits by as much as 21%.
This correlation underscores the necessity of balancing oversight with employee well-being, especially in light of recent findings that indicate:
- 56% of monitored employees report feeling tense or stressed, compared to 40% of their non-monitored counterparts.
- 80% of US employees are stressed due to ineffective company communication.
Furthermore, factory monitoring practices can enhance not only productivity but also communication within teams. By adopting proactive control with Movley’s inspections, brands can prevent returns caused by issues and catch missing units, thus safeguarding their reputation.
Notably, 94% of customers have avoided making a purchase due to a bad review, highlighting the critical need for quality assurance. To sustain and enhance these productivity gains, it is essential to regularly evaluate and improve factory monitoring practices, adapting them to emerging technologies and methodologies. As highlighted by GoRemotely, 82% of remote employee managers voice worries regarding diminished productivity, stressing the significance of supportive oversight instead of micromanagement, which can result in burnout and disengagement.
Aligning factory monitoring goals with overarching business objectives not only fosters operational efficiency but also cultivates a more positive work environment, ultimately leading to sustained success.
Conclusion
In the evolving landscape of manufacturing, the integration of Artificial Intelligence and real-time data analytics is proving essential for optimizing factory operations. By leveraging AI, manufacturers can proactively monitor production processes and implement predictive maintenance strategies that significantly reduce downtime and enhance overall efficiency. The staggering statistic that 60% of product returns stem from preventable quality issues underscores the need for robust monitoring systems, which can safeguard both product quality and brand reputation.
Real-time data is pivotal in this transformation, allowing manufacturers to make informed decisions swiftly. With tools like Movley’s integrated platform, organizations can track inspections and respond to anomalies instantly, thus averting costly production delays. The rise of smart manufacturing technologies, including IoT sensors, further emphasizes the importance of real-time insights in navigating the complexities of modern manufacturing environments.
Moreover, the article highlights that improving factory monitoring does not require a complete overhaul of existing systems. Simple measures such as:
- Conducting audits
- Equipping machinery with sensors
- Establishing routine data reviews
can lead to significant enhancements in performance. By focusing on essential features like real-time analytics and user-friendly interfaces, manufacturers can create effective monitoring systems that drive productivity while maintaining high quality standards.
Ultimately, the successful integration of AI-driven monitoring solutions and proactive quality control measures is paramount for manufacturers aiming to thrive in a competitive market. As organizations adapt to these advancements, they position themselves not only to improve operational efficiency but also to cultivate a sustainable future in manufacturing. Embracing these innovations ensures that companies can meet customer expectations and mitigate risks associated with quality failures, fostering long-term success and resilience in a rapidly changing industry.