10 Real-World Non Conformance Examples You Should Know About
Explore key non conformance examples and their impact on quality management and business success.
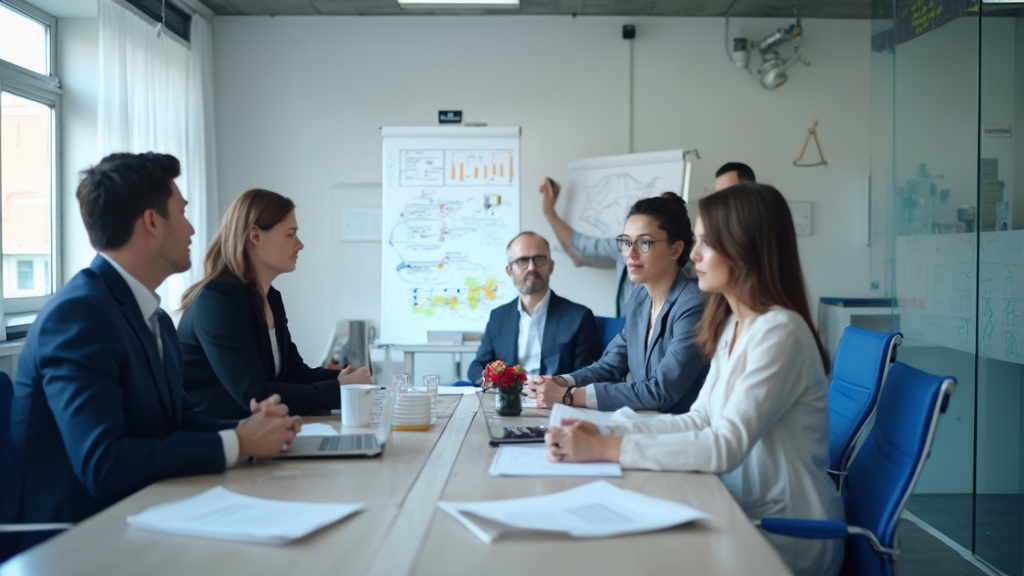
Introduction
In an increasingly competitive landscape, organizations must prioritize quality management to navigate the complexities of non-conformance effectively. Defined as the failure to meet established requirements or standards, non-conformance can have far-reaching consequences, including financial losses, reputational damage, and regulatory penalties.
As recent statistics reveal, a significant portion of product returns stems from preventable quality issues, underscoring the urgency for brands to adopt proactive measures. By understanding the various types of non-conformance and their implications, companies can implement robust strategies to mitigate risks and enhance operational integrity.
This article delves into the critical aspects of non-conformance, offering insights into its definition, types, consequences, and practical strategies for management, with a focus on leveraging innovative solutions to ensure compliance and foster continuous improvement.
Understanding Non-Conformance: Definition and Importance
Non conformance examples are defined as the failure to meet established requirements, standards, or regulations in a product or process. Within the domain of management, identifying and tackling deviations is crucial for organizations seeking to guarantee product reliability and improve customer satisfaction. Overlooking deviations can lead to serious consequences, such as substantial financial losses, reputational damage, and compliance challenges.
Recent findings indicate that 60% of returns are due to preventable quality issues, which Movley addresses through proactive on-site inspections. Moreover, with 94% of customers avoiding purchases based on negative reviews, protecting your brand reputation is paramount. As highlighted by a survey, 67% of global executives find navigating ESG regulations overly complex, emphasizing the growing need for clarity and guidance on compliance matters.
This complexity highlights the risks related to non-compliance, as organizations may struggle to align with evolving regulations. Organizations that proactively manage non conformance examples not only mitigate risks but also enhance operational efficiency, positioning themselves advantageously in competitive markets. The integrated platform enables direct-to-consumer brand owners to monitor inspections directly associated with their storefronts, ensuring that control processes are seamless and effective.
By leveraging such innovative technologies, including real-time tracking and reporting features, you can safeguard your financial performance and maintain a robust standing in your industry. Sleep easy knowing that with Money, you are taking proactive steps to prevent bad batches and protect your brand.
Exploring Different Types of Non-Conformances
Non-conformances can be categorized into several distinct types, each with significant implications for organizations striving for excellence in management of standards:
- Non conformance examples occur when a product fails to adhere to the specifications or performance standards established by the manufacturer. Such deviations can lead to costly recalls and damage to brand reputation. The platform plays a crucial role in helping brands like The Mindful Collective and Hash Stash mitigate these risks through effective quality control processes. For instance, Caddent Golf utilized insights to ensure their products consistently met market standards, enhancing their reputation and customer trust.
Non conformance examples arise when a process strays from established procedures or protocols, which can result in inefficiencies and increased operational costs. A recent analysis highlighted that in 2024, data breaches exposed over 7 billion records, underscoring the critical importance of adhering to secure processes. The company assists brands in optimizing their operations to guarantee compliance and operational integrity, as illustrated by Neil Ayton's method in overseeing various suppliers within his e-commerce portfolio.
Documentation non-conformance examples include incomplete or inaccurate documentation that does not meet regulatory requirements. Effective documentation is essential for compliance, and lapses can lead to severe legal repercussions. Comprehensive reports provided by Movley, including photos and videos, help brands maintain accurate documentation and protect against negative customer experiences. Brands utilize these reports to tackle compliance issues proactively, ensuring they meet all regulatory standards.
Supplier non conformance examples highlight situations where a supplier fails to provide materials or components that meet agreed-upon quality standards. Considering that 32% of all documented data breaches from 2015 to 2022 occurred in the healthcare sector, the consequences of such non-compliance can be especially serious in areas where adherence is essential. The case study of 'Voice Cloning Bank Fraud 2020' illustrates how a failure to adhere to secure processes can result in significant financial losses. Movley's supervision of inspections guarantees that suppliers adhere to the required standards, improving overall brand integrity.
Understanding these kinds of deviations provides businesses with the insight to pinpoint particular problems and apply effective solutions, ultimately boosting operational integrity and customer satisfaction. As pointed out by Cybint,
Over 77 percent of entities lack an incident response plan,
emphasizing the necessity for proactive actions in management to reduce the risks linked to non-compliance.
Consequences of Non-Conformance: Real-World Implications
The implications of non-conformance examples can be profound and multifaceted, impacting various aspects of a company. The company's dedication to control services is especially pertinent here, as we aim to improve retail standards and sustainability in today's changing market. Here are some key consequences:
-
Financial Loss: Non-conformance examples often lead to substantial financial repercussions, including product recalls, legal fees, and lost sales. Recent statistics indicate that organizations can incur millions in costs due to these issues, severely affecting their bottom line. This company helps mitigate these risks by providing tailored quality control solutions that align with sustainable practices.
-
Reputational Damage: A brand's reputation is invaluable, and when customers encounter subpar products, trust and loyalty can erode quickly. In 2024, reputational damage due to non-conformance examples has become a critical concern, with companies experiencing a drop in customer satisfaction and brand loyalty as a direct result. As cybersecurity expert Jeff Crume emphasizes, understanding the lessons learned from these incidents is crucial for mitigating reputational risks.
-
Regulatory Penalties: Non-conformance examples of non-compliance with industry regulations can lead to hefty fines and sanctions, straining resources and diverting attention from core business operations. Organizations must remain vigilant to avoid these costly repercussions. The contemporary control platform from our company is designed to assist brands in managing these complexities efficiently, distinguishing us from rivals such as HTQS and QIMA, who may not provide the same degree of customized assistance.
-
Operational Disruptions: Non-conformance examples can lead to significant disruptions in supply chains and production processes, resulting in inefficiencies and delays that further exacerbate financial losses. Implementing Statistical Process Control (SPC) techniques can assist entities in detecting process variations and non-conformance examples in real time, allowing for quicker corrective actions. The tailor-made teams are equipped to offer practical support in identifying and addressing these issues swiftly, unlike HTQS and QIMA, who may lack the same level of personalized service.
To reduce these risks, entities should prioritize management and compliance initiatives. Recommended approaches involve cultivating a culture of excellence, investing in employee training, and utilizing data analytics. By recognizing these potential consequences and adopting effective strategies, including partnering with movie, entities can position themselves for long-term success.
Mitigating Non-Conformance: Practical Strategies
To effectively mitigate non-conformance, organizations can adopt several key strategies that promote a culture of quality and accountability:
-
Regular Quality Audits: Frequent audits are essential for identifying potential non-conformance examples early, which allows organizations to address them proactively. The importance of these audits is underscored by research highlighting their role in enhancing financial reporting oversight, as noted by Paul Munter, Acting Chief Accountant:
Audit committees play a vital role in the financial reporting systems of public companies through their oversight of financial reporting, including internal controls over financial reporting, and over the external, independent audit process.
Movley's supplier audits exemplify this approach, reducing risks and ensuring reliability in vendor partnerships. Customers have praised these audits, noting, "Great recommendations" and "I know I can trust my inspection results." -
Clear Communication: Establishing clear communication around excellence standards and procedures is crucial. When all team members are well-informed, the risk of errors diminishes significantly, fostering a more cohesive working environment.
-
Supplier Evaluation: Regularly assessing suppliers for adherence to standards is vital to preventing non-conformance examples related to external partnerships. This proactive strategy guarantees that all elements of the supply chain fulfill set standards, as demonstrated by Movley's effective assessments that improve overall product excellence and customer satisfaction. As one customer mentioned, "Movley changed our strategy for oversight, assisting us in expanding on Amazon."
-
Training Programs: Ongoing employee training enhances understanding of management practices and instills a sense of accountability. Studies show that effective training can result in a decrease in compliance issues, fostering a workforce that is more capable of meeting standards. Notably, organizations with robust training programs see significantly lower rates of non-conformance examples, reinforcing the value of investment in employee development.
-
Utilizing Technology: Leveraging digital tools for standards control streamlines processes and enhances accuracy in monitoring compliance. Movley's digital inspections play a critical role in this, facilitating real-time tracking of performance metrics and ensuring consistent adherence to standards, thus preventing up to 60% of returns and protecting brand reputation against negative reviews that deter 94% of potential customers. Customers have expressed their satisfaction, stating, "The thoroughness and accuracy of their inspections have been a game changer."
In the context of audit standards, factors such as auditor independence and experience are critical. Recent research conducted in Vietnam found that these factors positively influence audit standards, highlighting the importance of having well-trained and independent auditors.
Implementing these strategies not only aids in reducing the risk of non-compliance but also establishes a strong framework for continuous improvement. For instance, the case study on the effectiveness of internal audits within Sierra Leone's National Social Security Insurance Trust illustrates how a strong internal audit framework can lead to enhanced organizational performance, further validating the importance of quality audits in preventing deviations. Movley's impact is evident in case studies, such as how they helped Maurice Mann recover $1 million in revenue by improving his Amazon ratings from 5 stars to 4.7, showcasing the tangible benefits of their services.
Managing Non-Conformance: Insights from ISO 9001
ISO 9001 provides a strong structure for efficiently handling deviations, and entities should adopt several key insights:
- Establishing a Non-Conformance Procedure: It is essential for organizations to develop precise procedures that guide the identification, documentation, and resolution of non conformance examples. This clarity ensures that all stakeholders understand their roles in addressing concerns related to standards. The company enhances this process with a dedicated platform and trained personnel focused on rigorous quality control, ensuring that critical issues are caught early, especially in the Electrical & Electronic industry, where mislabeling and poor supplier performance can lead to significant returns and revenue loss. For instance, the platform includes automated alerts for mislabeled units, allowing for immediate corrective measures before products reach consumers.
- Root Cause Analysis: Conducting comprehensive investigations to uncover the root causes of deviations is critical. Such analyses not only help in resolving current issues but also play a pivotal role in preventing future occurrences. The trained operations staff supports configurable review processes, enabling teams to customize investigations based on specific non conformance examples. This includes utilizing data analytics tools within the platform to identify patterns in defects, thus enhancing the investigation process.
- Corrective Actions: Based on the insights gained from non conformance examples, implementing effective corrective actions is vital. This step guarantees that issues are resolved thoroughly, minimizing the likelihood of recurrence and enhancing overall compliance. Movley’s platform facilitates this by providing a comprehensive dashboard that tracks corrective actions, ensuring accountability and follow-through. The software's audit trails provide traceability for all corrective actions taken, further improving compliance with industry standards.
- Ongoing Development: ISO 9001 promotes a culture of ongoing development, encouraging entities to regularly evaluate and enhance their management processes. This ongoing assessment results in sustained improvement of standards and operational efficiency. Movley’s real-time data reporting feature enables organizations to monitor their improvement efforts continuously, offering insights into trends that may indicate potential quality issues. By leveraging tools like Movley's quality control platform alongside the standards set forth by ISO 9001, D2C brand owners can systematically manage deviations, thereby improving their overall quality management practices and ultimately reducing the impact of poor suppliers and mislabeled units on their operations. According to recent statistics, effective non-conformance management is critical for maintaining compliance and operational excellence in 2024, making it more important than ever for D2C brand owners to implement these strategies.
Conclusion
Addressing non-conformance is critical for organizations aiming to uphold quality management standards and ensure operational integrity. Understanding the definition of non-conformance and its various types—product, process, documentation, and supplier—enables companies to identify and tackle specific issues before they escalate. The consequences of non-conformance can be severe, leading to financial losses, reputational damage, regulatory penalties, and operational disruptions. Therefore, proactive management is essential.
Implementing practical strategies, such as:
- Regular quality audits
- Clear communication
- Thorough supplier evaluations
- Ongoing employee training
- Leveraging technology
can significantly mitigate the risks associated with non-conformance. These measures foster a culture of quality and accountability, ultimately enhancing customer satisfaction and brand loyalty.
Moreover, insights from ISO 9001 highlight the importance of:
- Establishing robust procedures
- Conducting root cause analyses
- Committing to continuous improvement
By integrating these practices, organizations can systematically manage non-conformance, ensuring compliance and operational excellence. In an increasingly competitive landscape, prioritizing quality management is not just beneficial; it is essential for long-term success and resilience in the market.