What Is the Difference Between Quality Inspection and Quality Assurance? A Comprehensive Overview
Discover what is the difference between quality inspection and quality assurance in this comprehensive overview.
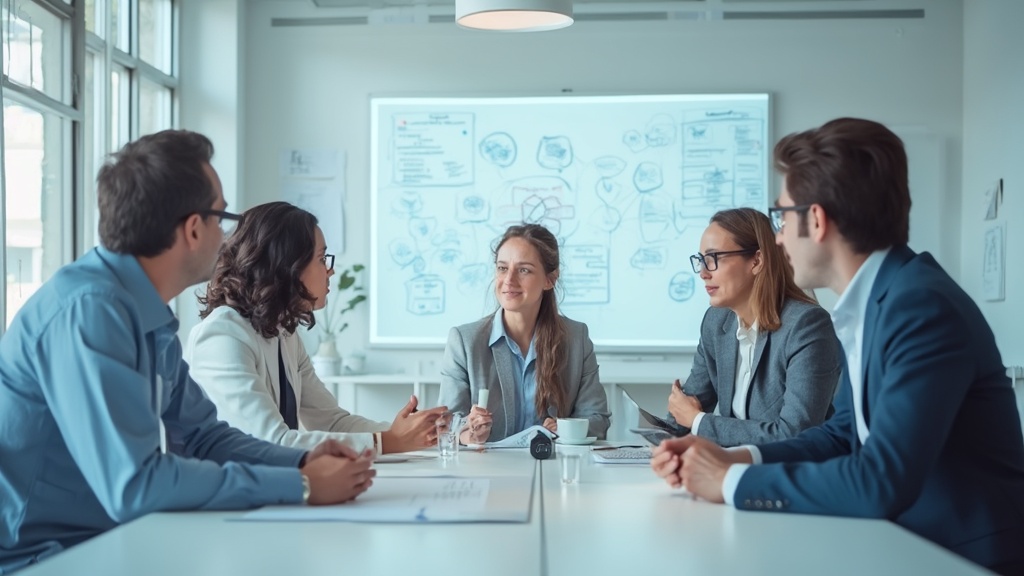
Introduction
In the competitive landscape of modern commerce, the significance of Quality Assurance (QA) and Quality Control (QC) cannot be overstated. As brands strive to meet and exceed consumer expectations, understanding the nuances between these two critical components becomes essential.
- QA focuses on the overarching processes that prevent defects before they occur,
- while QC zeroes in on identifying issues in finished products through rigorous inspections.
This article delves into the evolution of QA and QC, highlighting their integration into business strategies and the pivotal role of quality inspections.
By examining industry best practices and the challenges organizations face, it offers valuable insights into how companies can enhance product quality, optimize operations, and ultimately foster customer loyalty in an ever-demanding market.
Defining Quality Assurance and Quality Control
Quality Assurance (QA) refers to the systematic processes implemented to ensure that a good or service meets specified requirements and standards before it reaches the consumer. It encompasses the entire production process, focusing on preventing defects through planned and systematic activities. In contrast, Quality Control (QC) is a subset of QA that involves the operational techniques and activities used to fulfill standards, primarily concerned with identifying flaws in completed items through inspection and testing.
While QA is proactive, focusing on process design and improvement, QC is reactive, concentrating on detecting and correcting defects after production. To improve operational efficiency and reduce returns, companies can utilize Movley's integrated platform, which effortlessly connects with storefronts to monitor inspections and apply custom checks designed for specific items. This proactive approach can prevent up to 60% of returns due to manufacturing issues, ultimately safeguarding reputation against the negative reviews that influence 94% of purchasing decisions.
Grasping what is the difference between quality inspection and quality assurance? is crucial for brands that aim to improve their offerings and enhance customer satisfaction.
The Evolution of Quality Assurance and Quality Control
The concepts of Quality Assurance and Quality Control have evolved significantly since their inception, prompting the question of what is the difference between quality inspection and quality assurance? At first, standards procedures focused on basic inspection techniques, where completed items were examined for flaws. However, as industries expanded and consumer demands rose, the need for more robust management systems emerged.
The implementation of Total Quality Management (TQM) in the late 20th century redirected the emphasis from simply examining items to enhancing processes and cultivating a culture of excellence within organizations. This evolution has led to the adoption of various methodologies, such as Six Sigma and Lean Manufacturing, which emphasize continuous improvement and waste reduction. Today, QA and QC are integral to the supply chain, influencing everything from product design to customer feedback loops, which leads to the question: what is the difference between quality inspection and quality assurance, in ensuring that brands can consistently deliver high-quality products that meet consumer expectations?
Significantly, this platform exemplifies this evolution, assisting Amazon sellers like Maurice Mann regain $1 million in revenue and enhance star ratings from 3.5 to 4.7 through efficient inspections. Furthermore, The Mindful Collective changed their standards management method with support from another source, resulting in substantial growth on Amazon. Hash Stash's COO, Clara Mae Silvestre, also shared how their company optimized their control processes, enabling them to scale operations effectively.
By selecting Movley instead of rivals such as HTQS and QIMA, brands gain from a modern control platform that provides customized teams and attentive service, which are essential for enabling them to expand operations and improve overall performance.
The Importance of Quality Inspection in Quality Control
Quality assessment is an essential element of control, acting as the checkpoint where items are evaluated against established standards and specifications. This process involves examining items at various stages of production, from raw materials to finished goods. Effective inspection practices, such as those provided by Movley, assist in identifying defects early, minimizing waste and stopping flawed products from reaching consumers.
For instance, in the apparel industry, inspectors may evaluate:
- Fabric standard
- Stitching precision
- Sizing
before garments are shipped. Once you approve a tailored inspection plan, our service team will coordinate the requirements with our inspectors to ensure thorough evaluations. Companies can then obtain comprehensive reports that include multimedia elements like photos and videos, enhancing protection against negative reviews and poor customer experiences.
This proactive approach to management not only enhances brand reputation and fosters customer loyalty but also directly addresses industry challenges like sizing errors and material discrepancies through Movley’s specialized solutions, ultimately driving sales and ensuring consumers receive products that meet their expectations.
Integrating Quality Assurance and Quality Control in Business Strategy
Incorporating Assurance (QA) and Control (QC) into a business strategy necessitates a comprehensive approach that aligns objectives with organizational goals, which raises the question of what is the difference between quality inspection and quality assurance? Creating a strong supplier assessment process is vital for lasting collaboration, as it assists in evaluating potential and current partners to guarantee their dependability and standards. Companies should also perform regular audits to reduce risks and uphold supplier standards, which is crucial for decreasing returns and improving seller ratings, particularly for labels selling on platforms like Amazon.
For instance, an electronics company may implement automated testing during production (QC) while simultaneously conducting comprehensive audits of their manufacturing processes (QA), prompting the inquiry of what is the difference between quality inspection and quality assurance? As one customer noted, "The thoroughness and accuracy of their inspections have been a game changer for our business." By aligning these efforts and employing assurance solutions, companies can enhance item standards, optimize operational efficiency, and greatly boost customer satisfaction.
As another client stated, "I know I can trust my inspection results and not risk my entire business on every order." This strategic alignment not only fosters product excellence but also establishes the company as a leader in standards within its industry. To learn how our company has positively influenced other labels, read more customer stories highlighting our effect on control standards and business growth.
Challenges and Best Practices in Quality Management
Implementing effective Quality Assurance (QA) and Quality Control (QC) practices can pose several challenges for organizations, including:
- Resistance to change from employees
- Lack of resources
- Insufficient training
To overcome these hurdles, companies should prioritize fostering a culture of excellence that emphasizes the significance of QA and QC at all levels of the organization. Dedicated to transforming standards in the consumer retail sector, this company offers a variety of services aimed at assisting brands in boosting customer confidence and satisfaction through sustainable practices.
Optimal methods involve:
- Investing in employee training
- Utilizing technology for data collection and analysis
- Frequently reviewing and updating standards
The FAST Schedule, Inspect, & Ship System ensures cargo inspections are timely, with 48-72 hour turnaround times, and provides additional resources like personalized 'Pass/Fail' scoring systems and inspection budgeting guides. For instance, brands in the home and garden sector can benefit from using customer feedback loops to refine their quality processes continuously.
Testimonials from pleased clients emphasize the effectiveness of the company's services in enhancing reliability and customer satisfaction. Additionally, the company provides cost-effective strategies that make inspections affordable while maximizing ROI. By adopting these best practices and leveraging Movley's comprehensive quality assurance tools, organizations can enhance their quality management systems, leading to improved product reliability and customer satisfaction.
Conclusion
In today's competitive marketplace, understanding the differences between Quality Assurance (QA) and Quality Control (QC) is crucial for delivering high-quality products. QA focuses on preventing defects through proactive processes, while QC identifies issues in finished products. This integration is essential for brands aiming to enhance customer satisfaction and optimize operations.
The evolution of quality practices has shifted from simple inspections to comprehensive management systems emphasizing continuous improvement. Methodologies like Total Quality Management and Lean Manufacturing foster a culture of quality that impacts all operations, improving product reliability and enhancing brand reputation.
Quality inspection is a key aspect of effective QC, ensuring products meet established standards throughout production. By implementing strategic inspection practices, brands can detect potential defects early, safeguarding their reputation and building consumer trust. Aligning QA and QC within a cohesive business strategy enhances operational efficiency and reduces returns.
While challenges in implementing quality management practices exist, fostering a culture that prioritizes quality is vital. Investing in employee training and leveraging technology can streamline processes and improve reliability. By following best practices and utilizing comprehensive quality assurance solutions, brands can position themselves as leaders in quality.
In conclusion, integrating QA and QC is essential for brands seeking to thrive in a competitive market. Prioritizing quality at every stage not only boosts customer satisfaction but also drives sales and strengthens brand reputation in an ever-demanding landscape.