What is a Quality Checklist Format? Understanding Its Importance and Components
Discover the significance and key elements of an effective quality checklist format.
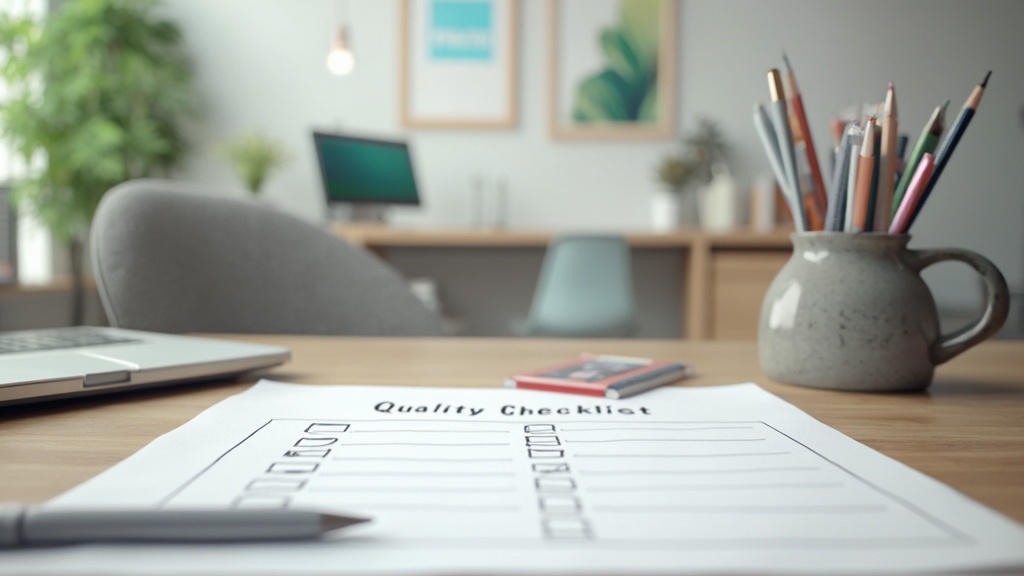
Introduction
In the realm of quality assurance, the importance of meticulously crafted checklists cannot be overstated. These systematic tools serve as the backbone of operational excellence across various industries, particularly in manufacturing and healthcare, where adherence to quality standards is critical. As organizations strive to enhance efficiency and minimize errors, tailored quality checklists emerge as indispensable assets. They not only streamline processes but also significantly bolster customer satisfaction by ensuring that products meet stringent quality criteria before reaching the market.
This article delves into the multifaceted role of quality checklists, exploring their key components, the challenges faced in their implementation, and best practices for creating effective checklists that drive success in today’s competitive landscape.
Defining Quality Checklist Formats: An Overview
A reliable quality checklist format serves as a systematic instrument designed to ensure that items, services, or processes comply with established standards of excellence. These lists find use across a multitude of industries, notably in manufacturing and healthcare, where consistency and reliability are paramount. Movley advances this by offering customized assessment support, collaborating closely with clients to create personalized lists that address the distinct characteristics of their offerings.
By outlining specific criteria and procedural steps, these detailed inspection checklists in a quality checklist format allow teams to systematically confirm adherence to all essential standards before completion. This structured approach not only streamlines operational efficiency but also markedly mitigates the risk of errors, which is crucial in fostering enhanced customer satisfaction and loyalty. For instance, Movley's role in inspecting 10,000 units monthly for Hash Stash significantly improved their operational efficiency and helped maintain high item ratings.
Likewise, The Mindful Collective shifted from initial doubt regarding inspections to attaining 7-figure success through improved control measures. In contrast to conventional inspection techniques, which often depend on generic lists and lack personalized insights, Movley’s approach includes:
- Asking 15 to 20 specific questions about the business and product
- Storing product assets
- Providing tailored recommendations
Firms in high-risk sectors must adhere to Conformité Européenne Mark (CE Mark) standards to operate in Europe, highlighting the regulatory conformity that assessment lists facilitate.
According to the 2019 Quality Progress Salary Survey, organizations that implement a quality checklist format for thorough assessments have shown notable increases in performance, demonstrating the tangible benefits of adhering to standards. As emphasized by industry professionals, 'Verification of follow-up actions may be part of a subsequent audit,' reinforcing the importance of evaluation tools in promoting ongoing enhancement and value-added assessments. Additionally, acquiring auditing certification is associated with enhanced earning potential, as certified auditors typically receive considerably higher salaries than non-certified individuals, illustrating the financial advantages of applying effective evaluation procedures.
Key Components of an Effective Quality Checklist
A strong set of criteria is vital for maintaining uniform standards in manufacturing and construction. Key components include:
-
Clear Objectives: Each list should articulate a specific purpose, detailing the quality aspects under scrutiny.
This focus fosters alignment and clarity in evaluation. -
Specific Criteria: The list must enumerate precise criteria or benchmarks that must be met, enhancing transparency and facilitating a straightforward assessment process.
-
Organized Layout: An organized and logical layout in a quality checklist format is vital, enabling users to navigate and complete the task with ease.
-
Space for Comments: Incorporating areas for notes or remarks allows for the inclusion of observations that may not be captured by standard criteria, providing a richer context for evaluations.
-
Review and Approval Sections: These segments are crucial for establishing accountability and ensuring traceability within the assurance framework.
Additionally, it is important to approve the inspection plan to coordinate requirements effectively before the inspection begins.
As highlighted in recent conversations, such as those led by Sameera Daniels, there is a pressing need for clarity in statistical methods and evaluation processes, particularly in light of the p-value of 0.09 reported in recent studies. This aligns with the findings from the case study on the necessity of comprehensive lists in clinical trials, underscoring that both statistical and non-statistical factors, including ancillary analyses like missing imputed case analysis and alternative multivariable models, must be formalized to uphold the integrity and reproducibility of results.
Furthermore, the comprehensive report you will receive will include multimedia elements such as photos and videos, ensuring a thorough understanding of the inspection results. By incorporating these components and utilizing customized assurance checks from a dedicated evaluation team, D2C companies can effectively prevent defective batches, reduce returns, and safeguard their reputation, ultimately improving customer experience. For next steps, consider discussing your specific requirements with our team to create a tailored quality checklist format.
The Importance of Quality Checklists in D2C Brands
In the direct-to-consumer (D2C) environment, where companies engage directly with consumers, maintaining high standards is not simply advantageous—it's crucial. As noted, 'The more locations your items can be found, the greater chances you have of making sales as consumers leverage multiple channels to make their decision.' To navigate this competitive environment, the use of a quality checklist format emerges as an essential tool that ensures each item aligns with the company's strict performance standards before reaching the consumer.
This is especially vital in sectors like apparel and electronics, where defects can lead to significant returns and erode customer trust. Companies like Eve Sleep, recognized for its innovative hybrid mattresses, stress control measures to improve customer satisfaction and product appeal. Movley, acknowledged as the top trusted ally for expanding companies, supports this mission by offering:
- Thorough assurance
- Automatic scheduling for inspections
- A tailored 'Pass/Fail' scoring system that guarantees reliability in product standards
With over 1.07 million retail establishments in the U.S., D2C companies face intense competition, making the implementation of a quality checklist format a strategic necessity. By adopting these tools in a quality checklist format, companies can significantly enhance operational efficiency, minimize waste, and improve customer satisfaction. Morley's FAST Schedule, Inspect, & Ship System streamlines cargo inspections, with 48-72 hour turnaround times and budget-friendly strategies, including inspection budgeting and ROI guides that illustrate how effective control can be both economical and efficient.
Moreover, labels such as VETTA, which designs five-piece capsule collections for adaptable outfits, illustrate how standards can be utilized to guarantee product uniformity and attractiveness. Such measures are indispensable for achieving long-term success in today's dynamic market, where consumer expectations are continually evolving. Movley has positively influenced hundreds of brands by assisting them in scaling and preventing negative customer feedback, reinforcing the significance of control in establishing trust and satisfaction.
Common Challenges in Implementing Quality Checklists
Implementing a quality checklist format for assessments is crucial for achieving operational success but often presents significant challenges. Employees frequently resist the introduction of these lists, viewing them as additional burdens—especially in high-pressure environments where time is of the essence. This resistance is further compounded by inadequate training on the quality checklist format and the common tendency to overlook items during peak operational periods.
To counteract this, organizations can leverage Movley's modern inspection platform, which offers customizable inspection plans tailored to specific needs, allowing for personalized testing instructions and control. Movley’s customized teams offer a high-touch service that sets it apart from other inspection firms, ensuring a more responsive and effective control process. By integrating supplier self-checks for kitting, brands can ensure compliance with 3PL work order standards, thus enhancing accountability and quality assurance.
As noted by A.K.D., 'Although the developed lists provide comprehensive evidence-based statistical approaches for commonly used research designs, these lists exclude synthesis of advanced statistical approaches and designs.' This emphasizes the limitations of current lists that can contribute to employee skepticism. Movley addresses these limitations by providing a flexible and supportive approach to control.
To alleviate these problems, organizations should foster a culture that values excellence, highlighting the essential role of a quality checklist format in attaining operational superiority. Comprehensive training programs presented in a quality checklist format that not only instruct on utilization but also illustrate their benefits can significantly enhance acceptance. Moreover, by utilizing Movley’s services, brands can avoid up to 60% of returns caused by defects, safeguarding their reputation against negative feedback, which influences 94% of buying choices.
Consistently reviewing and updating task items ensures they remain relevant and practical. Proactively addressing these challenges not only enhances adherence to assurance measures but also unlocks the full potential of control initiatives, allowing teams to focus on growing the business rather than managing issues.
Best Practices for Creating Quality Checklists
To create efficient assessment lists, D2C brands should follow several best practices that improve assurance processes and promote collaboration and engagement among stakeholders, ideally using a quality checklist format. Here are key recommendations:
- Involve Stakeholders: Engage team members from different departments—such as production, assurance of standards, and compliance—to gather varied viewpoints on essential items.
This collaborative method can result in a more thorough and effective quality checklist format. For instance, the success stories of brands like Hash Stash and The Mindful Collective illustrate how collaborating with Movley can transform quality control processes and drive growth on platforms like Amazon.
-
Keep It Simple: Clarity is paramount. Avoid complex language or criteria; instead, aim for straightforward guidelines that all users can understand and apply effectively.
-
Regular Updates: Quality evaluation tools should be dynamic instruments. Frequent evaluations and adjustments in a quality checklist format are essential to incorporate updates in processes, offerings, or industry standards, ensuring ongoing relevance and effectiveness. Movley's customized lists are created to meet the distinct requirements of each product, preventing up to 60% of returns by identifying quality issues early.
-
Pilot Testing: Before broad application, carry out pilot tests of the list in controlled environments. This approach assists in recognizing potential areas for enhancement and ensures that the list meets user needs.
-
Feedback Mechanism: Establish a robust feedback system that allows users to comment on the tool's effectiveness. Continuous feedback is essential for ongoing improvement and adaptation of the tool to real-world applications.
As R_cubed notes, to be a principled critic of a study requires the assertion of measurable variables that are adequately accounted for in the model. This principle should direct the creation of lists. By following these best practices, companies can develop effective lists in a quality checklist format that greatly improve their assurance frameworks, ultimately resulting in better public health results and stakeholder contentment.
Moreover, guaranteeing that these lists are utilized efficiently can safeguard company reputation, as 94% of consumers refrain from buying because of negative feedback. Discussing these issues publicly can further reinforce the connection between quality checklists and better health outcomes. To learn more about how Movley has helped brands like yours, read more customer stories like this.
Conclusion
Quality checklists play an indispensable role in ensuring operational excellence across various industries, particularly in manufacturing and healthcare. By establishing clear objectives, specific criteria, and a structured format, these checklists facilitate adherence to quality standards while enhancing transparency and accountability. Tailored approaches, such as those offered by Movley, not only streamline processes but also mitigate the risks of errors, ultimately contributing to elevated customer satisfaction and brand loyalty.
Despite their clear benefits, the implementation of quality checklists may encounter challenges, including employee resistance and inadequate training. Overcoming these hurdles requires a cultural shift within organizations, emphasizing the importance of quality and fostering collaboration among stakeholders. By integrating best practices such as:
- Stakeholder involvement
- Simplicity
- Regular updates
- Feedback mechanisms
companies can create effective checklists that adapt to evolving needs and industry standards.
In the competitive landscape of direct-to-consumer brands, the strategic use of quality checklists is not merely advantageous; it is essential for sustaining customer trust and preventing costly returns. As demonstrated by successful case studies, organizations that prioritize quality control through structured checklist implementation can significantly enhance their operational efficiency and market performance. Embracing these tools will not only safeguard brand reputation but also ensure long-term success in today’s dynamic market.