What Is a QC Inspection Checklist? Understanding Its Importance and Components
Discover the significance of a QC inspection checklist for ensuring product quality and consistency.
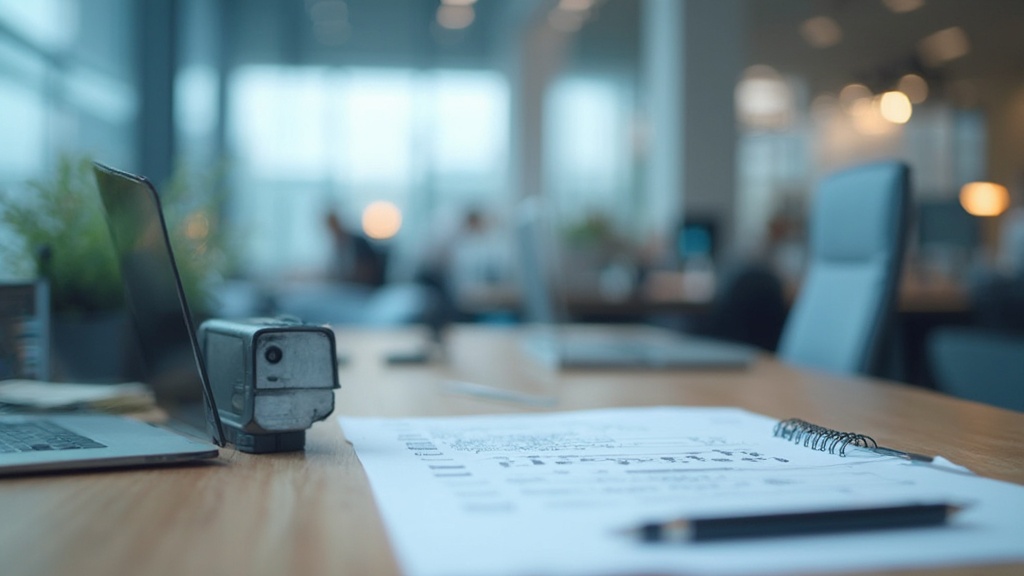
Introduction
In the competitive landscape of direct-to-consumer (D2C) brands, maintaining high product quality is not just a goal—it's a necessity. Quality Control (QC) inspection checklists serve as essential tools in this endeavor, ensuring that products meet stringent standards before reaching customers. By standardizing the inspection process, these checklists help reduce errors and enhance consistency, ultimately safeguarding brand reputation and customer satisfaction.
This article delves into the critical components of effective QC inspection checklists, the systematic approach to creating them, common implementation challenges, and the transformative role of technology in streamlining quality control processes. For brands striving to minimize returns and foster loyalty, understanding and implementing robust QC practices is paramount.
Defining QC Inspection Checklists: Purpose and Significance
A Quality Control (QC) evaluation list is a structured instrument utilized to guarantee that items satisfy particular standards before they reach consumers. It functions as a reference for inspectors to assess different characteristics of an item, such as dimensions, functionality, and aesthetic appeal. The importance of a QC evaluation list resides in its capacity to standardize the assessment process, minimize mistakes, and guarantee uniformity across batches.
For D2C brands, where customer satisfaction is crucial, using a QC inspection checklist can prevent up to 60% of returns caused by defects and enhance brand reputation by ensuring that only top-notch products are delivered to customers. Moreover, on-site evaluations can identify absent units, notifying your team of discrepancies before they affect your operations. With Movley’s tailored quality checks, you gain peace of mind, allowing your team to focus on operational efficiency while safeguarding against negative reviews that affect 94% of purchasing decisions.
Key Components of an Effective QC Inspection Checklist
An effective qc inspection checklist typically includes the following key components:
-
Item Specifications: Clear definitions of the item’s required dimensions, materials, and features.
-
Inspection Criteria: Specific standards against which the item will be evaluated, such as acceptable tolerances and performance metrics.
-
Visual Inspection Guidelines: Criteria for assessing the item's appearance, including color, finish, and packaging integrity.
-
Functional Testing Procedures: Steps to verify that the product operates as intended, which is particularly important for electronics and appliances.
-
Documentation and Reporting: Space for inspectors to document their findings, including any deviations from the list, facilitating accountability and traceability. Furthermore, integrating a comprehensive report that contains multimedia elements like photos and videos, along with detailed assessment instructions such as testing protocols and evaluation methods, can significantly enhance brand protection against negative reviews and customer experiences. Additionally, Movley provides customized assessment lists created through close cooperation with our assurance team, guaranteeing a personalized method to ensure that addresses specific unique item requirements.
By adopting the QC inspection checklist along with these thorough QC evaluation guides, D2C brands can not only enhance product standards but also simplify their assessment procedures, resulting in improved customer satisfaction.
The Process of Creating a QC Inspection Checklist
Creating a standards assurance (QA) evaluation guide necessitates a systematic method to guarantee that it satisfies the particular requirements of D2C brands. Here are the essential steps to create an effective QC evaluation checklist:
-
Identify Item Requirements:
Collaborate with development teams to collect detailed specifications and standards, ensuring that all item requirements are well understood. Movley’s on-site quality evaluations can enhance this step by providing firsthand insights from suppliers. -
Define Inspection Criteria:
Establish precise and measurable criteria for each aspect of the item that will be inspected. Clear definitions minimize ambiguity and enhance the reliability of inspections. Leveraging Movley’s tailored teams ensures that these criteria are aligned with industry standards. -
Consult Industry Standards:
Investigate relevant industry standards and regulations applicable to the product. This ensures compliance and helps maintain the quality expected in the market. Movley’s expertise in supplier evaluation can assist in vetting compliance issues. -
Draft the Checklist:
Organize the gathered information into a user-friendly format. A well-organized list enables inspectors to adhere to it with ease, improving the effectiveness of the evaluation process. Movley's innovative platform facilitates the development of tailored lists designed for different types of items. -
Pilot Testing:
Conduct a trial evaluation using the draft list. This practice helps identify gaps or areas needing improvement, providing valuable insights before finalization. For example, customer success stories highlight how Movley's thorough inspection processes have revealed crucial insights during this testing phase, significantly improving product quality and customer satisfaction. -
Review and Revise:
Gather feedback from inspectors who utilized the assessment during pilot testing. Use this input to make necessary adjustments, ensuring the list is both effective and practical. Movley’s high-touch service guarantees that clients obtain customized assistance during this process.
By following these steps, D2C brands can create personalized QC inspection checklists that aid their assurance goals. It is vital to re-inspire a struggling team during this process, as sustaining team performance and satisfaction directly affects the standard of the final outcome. As Doug Smith wisely noted,
Teams share the burden and divide the grief;
therefore, promoting a collaborative atmosphere during task development can greatly improve team performance and satisfaction, ultimately resulting in enhanced product excellence.
Furthermore, think about using the 20 teamwork quotes at your disposal to motivate and invigorate your group, and keep in mind Patanjali's perspective that a talented team merges selfless trust with courage and diligence, traits that are essential for effective project development. Additionally, to gain deeper insights into Movley’s impact, explore our customer testimonials and case studies, which showcase how brands have successfully enhanced their control processes.
Common Challenges in Implementing QC Inspection Checklists
Implementing QC inspection checklists can present various challenges, including:
- Resistance to Change: Employees may resist new processes or tools. Engaging them early in the development process can foster buy-in and collaboration, especially when supported by Movley's dedicated quality customer service team who are available for guidance.
- Insufficient Training: Inspectors may not be adequately trained to utilize the assessment tool effectively. Movley's commitment to providing comprehensive training ensures that inspectors are confident and skilled in executing their tasks.
- Checklist Overload: A list of tasks that is too lengthy or complex can lead to confusion and errors. It’s essential to strike a balance between thoroughness and usability, which Movley promotes through its personalized evaluation planning.
- Inconsistent Application: Different inspectors may interpret the checklist differently, leading to inconsistent results. Regular calibration sessions, supported by Movley's real-time monitoring, can help ensure consistency in evaluations.
By anticipating these challenges and implementing strategies to address them, D2C brands can significantly enhance the effectiveness of their QC inspection checklist, ultimately preventing manufacturing issues and improving customer experiences. As mentioned by pleased clients, "Movley's comprehensive evaluations and detailed reports have been a transformative factor for our assurance procedures," emphasizing the significance of their top-tier assessments. Furthermore, with 60% of returns linked to avoidable quality problems, implementing QC evaluation forms becomes essential in decreasing returns and improving customer satisfaction.
The Role of Technology in QC Inspection Checklists
Technology plays a crucial part in improving the qc inspection checklist, especially when tailored to meet the specific requirements of D2C brands. Movie emphasizes this personalization through several key advancements:
-
Digital Checklists: Utilizing software or mobile applications allows for real-time data collection and easier tracking of results, ensuring that each product receives a checklist specifically designed for its unique components.
-
Automated Reporting: Automation tools can produce detailed reports based on assessment data, saving time and minimizing the risk of human error, while delivering comprehensive insights into every aspect of control standards.
-
Data Analytics: Analyzing evaluation data can uncover valuable insights into recurring issues, helping brands identify trends and implement corrective actions effectively.
-
Integration with Supply Chain Management: Connecting QC assessment checklists with supply chain management systems promotes smoother operations and improved communication between teams, enhancing overall assurance.
-
Competitive Edge: Unlike HTQS and QIMA, Movley provides a customized approach with detailed control reports and a high-touch service model, ensuring that D2C brands receive personalized support throughout the assurance process. By adopting technology and utilizing Movley's efficient, detailed inspection services, D2C brands can establish a more effective qc inspection checklist process, ultimately resulting in improved product standards and greater customer satisfaction.
Get Started Talk to Sales to learn more about how Movley can enhance your quality control processes.
Conclusion
Ensuring product quality through effective QC inspection checklists is indispensable for D2C brands navigating today’s competitive market. These checklists not only standardize inspection processes but also significantly reduce errors and enhance consistency, which is crucial for maintaining customer satisfaction and protecting brand reputation. By understanding the key components of a robust checklist, such as:
- Clear product specifications
- Specific inspection criteria
- Functional testing procedures
brands can streamline their quality assurance processes and minimize returns.
Creating a QC inspection checklist involves a systematic approach, beginning with identifying product requirements and defining precise inspection criteria. Engaging with industry standards and conducting pilot testing further refine the checklist, ensuring it meets the unique needs of each product. Addressing common implementation challenges, such as:
- Resistance to change
- Inconsistent application
is essential for fostering a culture of quality within organizations.
Leveraging technology plays a transformative role in enhancing QC inspection processes. Digital tools facilitate:
- Real-time data collection
- Automated reporting
- Data analytics
providing brands with insights that lead to continuous improvement. By integrating these technological advancements with tailored inspection services, D2C brands can achieve higher product quality and greater customer satisfaction, ultimately reinforcing their competitive edge in the market. Investing in comprehensive QC practices not only safeguards product integrity but also paves the way for lasting customer loyalty and brand success.