What Are Examples of Defect? Understanding Their Impact and Importance
Discover various examples of defects and their significant impact on quality and efficiency.
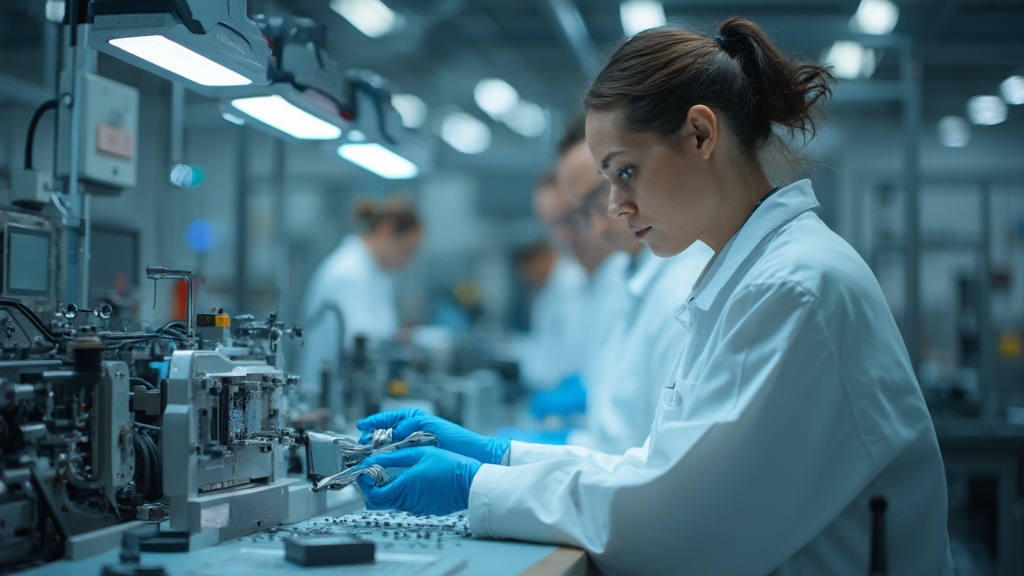
Introduction
In the competitive landscape of modern manufacturing and software development, the presence of defects can spell disaster for businesses striving for excellence. Defects, whether they manifest as physical flaws in products or as bugs in software, not only compromise quality but also threaten customer satisfaction and brand integrity.
As organizations increasingly recognize the critical need for robust quality control measures, innovative inspection techniques and comprehensive strategies are emerging as essential tools for mitigating these risks. By delving into the various types of defects and their implications, this article explores effective methodologies and real-world case studies that underscore the importance of proactive defect management.
Through a detailed examination of successful practices, businesses can better understand how to enhance their operational efficiency and maintain a competitive edge in a rapidly evolving market.
Defining Defects: What They Are and Where They Occur
An example of defect includes any flaws or imperfections in a product or service that diverge from established requirements or standards. In particular, the manufacturing sector often sees these imperfections manifesting as physical anomalies, which serve as an example of defect, such as misaligned components or incorrect dimensions. For example, a company assisted Maurice Mann in regaining $1 million in revenue by enhancing his Amazon account star rating from 3.5 to 4.7 through thorough assessments.
Likewise, The Mindful Collective shifted from doubt regarding inspections to evolving into a 7-figure enterprise by enhancing their control strategies with a customized method. Movley's tailored checklist support ensures that quality checks are specifically designed for each product, addressing unique challenges and enhancing overall product quality. In software development, issues are commonly referred to as bugs, and can result in system failures or diminished performance.
Manufacturing issues are widespread across different industries; for instance, the automotive sector encounters substantial challenges, which serve as an example of defect, especially concerning design flaws that undermine safety and functionality. Industry reports suggest that around 15% of produced items display some type of flaw, highlighting the necessity for effective control measures. The company tackles this requirement by offering detailed evaluation checklists customized for specific products, highlighting individualized assurance of standards.
Additionally, they inspect 10,000 units monthly for Hash Stash, showcasing their role in enhancing operational efficiency. Unlike traditional inspection methods that often rely on generic checklists, Movley’s approach involves asking 15-20 detailed questions about the business and product, ensuring a thorough understanding of the specific requirements. Understanding the different categories of defects is crucial for implementing effective measures, with an example of defect being manufacturing, design, and performance.
According to Todd Hockenberry, failing to innovate in control measures can lead to being outpaced by competitors. Hermann Tietz aptly noted, 'Excellence is when the customer returns, not the product,' highlighting the importance of thorough assurance processes. Robust testing frameworks, like those used by Movie, not only improve product standards but also significantly reduce time and expenses for developers, fostering a culture of continuous enhancement and ultimately leading to greater customer satisfaction and competitive advantage.
The Impact of Defects on Quality and Efficiency
Defects in products can be seen as an example of defect that profoundly impacts overall quality, often leading to high customer dissatisfaction rates and increased return rates. This situation can significantly tarnish a brand's reputation, especially in a landscape where over 70 percent of global consumers support brands that align with their purpose and values. For instance, one client mentioned, 'Movley is the best evaluation company out there,' highlighting the significance of thorough assessments in establishing trust.
Clients have reported exceptional satisfaction with the thoroughness of inspections, highlighting how detailed reporting and effective communication help them trust the results and mitigate risks. In the manufacturing sector, an example of defect can cause disruptions in production lines, leading to extensive downtime and substantial financial losses. Companies encountering an example of defect in their control measures can incur losses exceeding millions annually, not only facing immediate financial setbacks but also long-term damage to their market position.
With this service, brands can prevent up to 60% of returns due to quality issues, which serves as an example of defect prevention that protects their reputation against negative reviews impacting 94% of purchasing decisions. One satisfied customer noted, 'The thoroughness and accuracy of their inspections have been a game changer,' showcasing how Movley’s services specifically address issues like catching missing units and preventing returns. In software development, product issues, which are an example of defect, can manifest as system crashes or security vulnerabilities, further eroding user trust and satisfaction.
Drew Davis aptly points out that, 'Branded content and a content brand are different,' highlighting that organizations must prioritize creating valuable content that resonates with consumers. This approach can help reduce the consequences from issues, as effective communication can enhance customer satisfaction despite challenges. Richard Branson's dedication to branding principles illustrates how a commitment to continuous improvement and creativity can lead to successful outcomes, even in the face of manufacturing challenges.
By tackling product issues proactively through the company's control services, brands can protect their reputation and uphold consumer trust, providing an example of defect management that ultimately strengthens their market position.
Innovative Techniques for Defect Detection
Recent advancements in defect detection provide an example of defect detection being significantly influenced by innovative techniques such as image recognition software, machine learning algorithms, and data analytics. However, companies like this take this a step further by providing on-location evaluations that help D2C brands identify avoidable issues early, which can be considered an example of defect, ultimately decreasing returns and improving customer retention. For example of defect, Return Logic states that 60% of returns arise from avoidable quality problems, which can be efficiently resolved through comprehensive evaluation services.
The company offers a customized checklist and an extensive control report, guaranteeing that evaluations are detailed and specifically tailored to each brand's requirements. By asking targeted questions during the inspection process, the company assists brands such as The Mindful Collective in transforming their operations, achieving remarkable success on platforms like Amazon. Unlike conventional approaches that frequently depend on basic reports and generic checklists, Movley's proactive strategies provide an example of defect prevention, enabling companies to not only avert issues before products reach consumers but also to uphold high standards of product integrity in a rapidly evolving market.
This cultural shift towards comprehensive assurance underscores the importance of adapting to new technologies and methodologies to enhance customer experience and brand reputation.
Strategies for Effective Defect Reduction
To effectively minimize errors in manufacturing, organizations can implement several robust methodologies, including:
- Six Sigma
- Lean Manufacturing
- Total Quality Management (TQM)
Six Sigma is crucial in this environment as it aims at process variation and improves standards by systematically identifying and removing the root causes of issues. By adopting Six Sigma principles, organizations can achieve measurable improvements across all operational levels, demonstrating its efficacy as a risk-reduction initiative aimed at boosting customer satisfaction.
In 2024, it's reported that Six Sigma methods have achieved success rates surpassing 90% in error reduction efforts.
A pertinent case study titled 'Six Sigma Risk and Fault Abatement' emphasizes that Six Sigma is increasingly acknowledged not just as a quality program centered on minimizing errors, but as a business initiative aimed at reducing risk and enhancing customer satisfaction. This framework enables organizations to manage capabilities efficiently and attain measurable enhancements across all levels, highlighting the significance of minimizing errors and faults.
Lean Manufacturing enhances this by concentrating on waste reduction and process efficiency, resulting in fewer errors through streamlined operations. By minimizing non-value-added activities, Lean practices not only enhance productivity but also provide an example of defect reduction. Implementing Lean strategies has demonstrated a correlation with enhanced results, fostering a culture of continuous improvement.
Moreover, the role of supplier evaluations and audits cannot be overstated. The organization’s evaluation services, which encompass thorough product reviews and standards assessments, guarantee that D2C brands can rest assured knowing they will never receive a subpar batch, whether it's the first or the fiftieth order. These evaluations assist in identifying quality problems promptly, providing an example of defect that helps avoid returns and safeguard brand reputation.
As one pleased client remarked, "Movley’s comprehensive evaluations spared us from a possible disaster by detecting issues before shipment." Automation also plays a critical role in flaw reduction by limiting human error in production processes. As organizations adopt advanced automation technologies along with thorough inspections, they can further reduce the risk of errors, achieving higher precision and consistency in their outputs.
Together, these approaches promote a culture of excellence within organizations, emphasizing flaw prevention and creating a basis for operational superiority.
Case Studies: Successful Defect Management in Action
Numerous companies, including Movley, have set benchmarks in flaw management, which serve as an example of defect through the implementation of robust strategies that act as valuable case studies. The Toyota Production System (TPS) illustrates this, with its core principle of ongoing improvement and fault prevention, resulting in substantial advancements in vehicle standards and increased customer satisfaction levels. Statistics indicate that TPS has led to a reduction in error rates by over 30% in certain product lines, demonstrating its effectiveness in enhancing operational efficiency and promoting customer loyalty.
Similarly, Movley's best-in-class inspections utilize advanced methodologies and thorough evaluations to prevent up to 60% of returns by catching issues early, thus safeguarding your brand from negative reviews, with 94% of customers avoiding purchases influenced by them. The method of inquiring 'why' five times, as promoted by Taiichi Ohno, is an example of defect analysis that is essential in revealing root causes of problems, enabling organizations to apply effective solutions that avert future shortcomings. This methodology has been recognized for its effectiveness, with principles widely adopted across various industries.
Apple also distinguishes itself for its stringent control measures and thorough testing protocols, ensuring that its products consistently meet high standards and significantly reduce flaws. The strategies employed by both Toyota and Apple complement Movley's proactive quality control measures, illustrating that a strategic focus on quality not only mitigates risks but also enhances overall brand reputation. By effectively managing and reducing defects, such as an example of defect, through these best-in-class inspection processes, organizations can achieve substantial operational efficiency and foster customer loyalty.
Conclusion
Defects in manufacturing and software development present significant challenges that, if left unaddressed, can undermine quality, efficiency, and ultimately, customer trust. This article has explored the various types of defects, from manufacturing flaws to software bugs, and highlighted the profound impact they can have on a brand's reputation and financial stability. With case studies illustrating the success of companies like Movley and the Toyota Production System, it is evident that proactive defect management is not merely beneficial but essential in today’s competitive landscape.
Implementing robust strategies such as:
- Six Sigma
- Lean Manufacturing
- Comprehensive inspection techniques
can significantly reduce defect rates and foster a culture of continuous improvement. These methodologies not only enhance operational efficiency but also safeguard customer satisfaction, which is paramount in a market where consumer loyalty is increasingly tied to quality assurance. As organizations adopt innovative technologies and tailored inspection processes, they position themselves to preemptively address quality issues, thereby transforming potential challenges into opportunities for growth.
In conclusion, the path to excellence in manufacturing and software development lies in prioritizing quality control and defect management. By understanding the nature of defects and employing effective strategies to mitigate them, businesses can not only protect their reputations but also enhance their competitive edge in an ever-evolving market. The commitment to quality is a commitment to customer satisfaction, and it is through these diligent efforts that organizations can ensure lasting success.