Understanding the Structure and Benefits of the 8D Report Process
Effective problem-solving with the 8D report process enhances quality and operational efficiency.
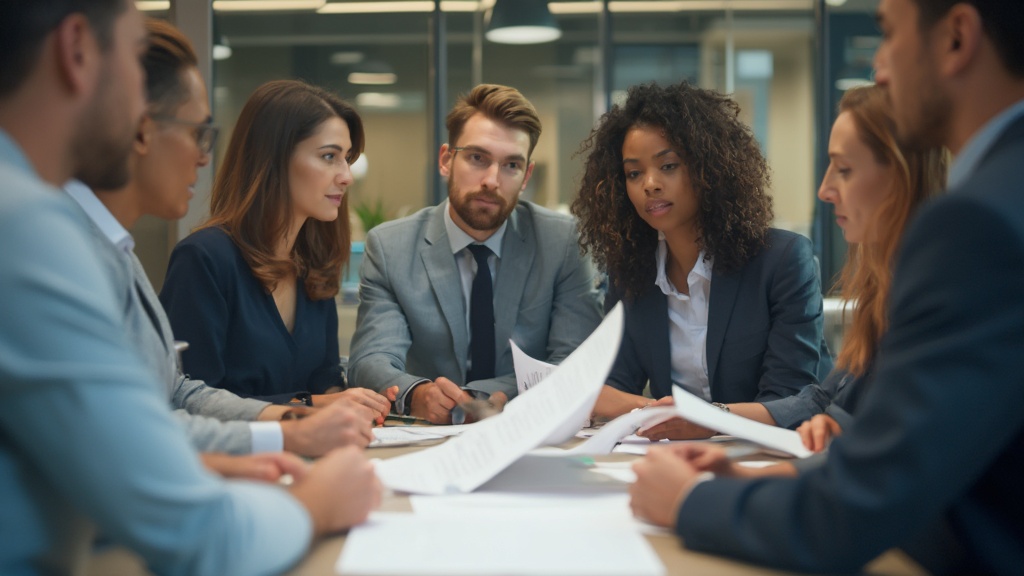
Introduction
Developed by Ford Motor Company in the 1980s, the 8D (Eight Disciplines) methodology has become a cornerstone in quality management, renowned for its systematic approach to problem-solving and process improvement. Initially created to address quality issues within the automotive industry, the 8D methodology's effectiveness quickly led to its adoption across various sectors. This comprehensive method involves eight critical disciplines, guiding teams through structured problem resolution to enhance product and process quality.
The widespread use of the 8D methodology underscores its versatility and robustness in tackling complex quality challenges, making it an indispensable tool for organizations striving for operational excellence and continuous improvement.
History and Development of the 8D Method
The 8D (Eight Disciplines) methodology, created by Ford Motor Company in the 1980s, was an innovative attempt to address performance challenges and improve efficiency within the automotive sector. This structured problem-solving approach quickly gained recognition for its effectiveness and was subsequently adopted across various sectors. Today, 8D is a cornerstone in quality management, recognized for systematically identifying, analyzing, and resolving issues to enhance product and operational standards. Its widespread use underscores the methodology's versatility and robustness in addressing complex quality challenges.
The 8 Disciplines of the 8D Report Process
The 8D report approach is a thorough methodology encompassing eight essential disciplines that lead groups through effective problem resolution. This organized method guarantees that each field tackles a particular facet of the problem, from assembling the appropriate group to acknowledging individual efforts, thus promoting cooperation and comprehensive examination. According to PwC findings, significant moves driving business model change are linked to improved profitability, highlighting the importance of a well-defined method like 8D in achieving operational excellence.
A practical example of a robust operating system can be seen in the Toyota Production System, which embeds an ethos of continuous improvement and cross-functional collaboration. This system illustrates how groups can generate value, reach established objectives, and uphold a culture of positive behavior. As outlined by specialists, efficient operating systems differ significantly but possess shared characteristics: directing group behavior, managing work activities, and nurturing a mindset of ongoing enhancement.
In a real-world scenario, a Latin American bank faced challenges in its digital strategy transformation due to unclear responsibilities and expectations among members. By restructuring and clarifying roles, the bank could harness the collective expertise of digital architects, designers, and experts, leading to more effective collaboration and better outcomes.
This organized format of the 8D methodology is not just confined to one team or department but is adaptable enough to adjust to evolving circumstances and priorities, ensuring reliable guidance and assistance throughout the organization. The hands-on world of auto manufacturing and beyond reveals that such systems are essential for maintaining high performance and achieving long-term success.
Benefits of the 8D Report Process
The 8D report method offers numerous benefits, including enhanced problem-solving capabilities, improved product quality, and increased customer satisfaction. By systematically tackling challenges, organizations can reduce the recurrence of problems and establish a culture of continuous improvement. The organized method also aids in improving communication and documentation throughout the procedure. This comprehensive approach not only addresses existing problems but also prevents future occurrences by implementing long-term solutions, which is essential for maintaining high standards and consistency. Furthermore, the 8D methodology aligns with the principles of digital transformation, where technology is leveraged to enhance data capture, analysis, and dissemination, ultimately contributing to better decision-making and operational efficiency.
Common Tools Used in the 8D Method
Enhancing the effectiveness of the 8D methodology involves leveraging various tools that aid in root cause analysis and problem prioritization. Methods such as the Fishbone diagram and the 5 Whys are vital for pinpointing fundamental problems, making them critical for any quality management process. These tools are particularly valuable in scenarios such as a sudden decline in shopping cart conversion rates on an e-commerce website. By applying these methods, a Product Manager can systematically uncover the root causes of the decline, whether they stem from technical glitches, user experience challenges, or external factors.
Additionally, Pareto charts and control charts are indispensable for prioritizing problems and monitoring improvements. These charts assist teams in concentrating on the most important challenges first, ensuring resources are allocated effectively. For instance, a Pareto chart can highlight that a small number of factors are causing the majority of the problems, allowing for targeted interventions. Control charts, on the other hand, provide a visual representation of data over time, making it easier to detect trends and measure the impact of implemented solutions.
Essentially, incorporating these tools into the 8D methodology not only simplifies problem resolution but also improves the overall quality management structure, guaranteeing a comprehensive and efficient approach to tackling challenges.
Challenges and Limitations of the 8D Method
While the 8D method is a powerful tool for problem resolution, it does come with its set of challenges. One significant concern is the potential for team fatigue during lengthy investigations, which can lead to decreased productivity and motivation. Maintaining focus on identifying and addressing root causes can also be difficult, particularly in complex scenarios where multiple factors are at play.
Irregular execution of the procedure can lead to unfinished solutions and repeated problems, weakening the efficiency of the 8D method. As highlighted by findings from a major PwC survey, organizational agility and structured approaches are essential for driving business model changes and improving profitability. Therefore, it's crucial for organizations to embed an ethos of continuous improvement and maintain vigilant commitment to the methodology. This commitment ensures that the 8D process is executed thoroughly and consistently across all levels, ultimately leading to more sustainable and effective problem resolution.
Conclusion
The 8D methodology, developed by Ford Motor Company, has established itself as a vital framework in quality management, transcending its automotive origins to serve diverse industries. Its structured approach to problem-solving, consisting of eight critical disciplines, enables organizations to effectively identify, analyze, and resolve complex quality issues. This systematic process not only improves product and process quality but also fosters a culture of collaboration and continuous improvement.
Utilizing tools such as the Fishbone diagram, 5 Whys, Pareto charts, and control charts further enhances the effectiveness of the 8D methodology. These tools play a crucial role in root cause analysis and problem prioritization, allowing teams to focus their efforts on the most significant issues first. By integrating these techniques, organizations can streamline their problem-solving processes and ensure a comprehensive approach to quality management.
Despite its numerous benefits, the 8D method is not without challenges. Issues such as team fatigue and inconsistent implementation can hinder its effectiveness. Therefore, it is essential for organizations to cultivate a commitment to continuous improvement and ensure that the 8D process is consistently applied across all levels.
By doing so, organizations can achieve sustainable solutions and maintain high standards of quality, ultimately driving operational excellence.