Understanding the Process of Inspection: An In-Depth Tutorial for Beginners
Explore the essential steps and elements in the process of inspection for quality assurance.
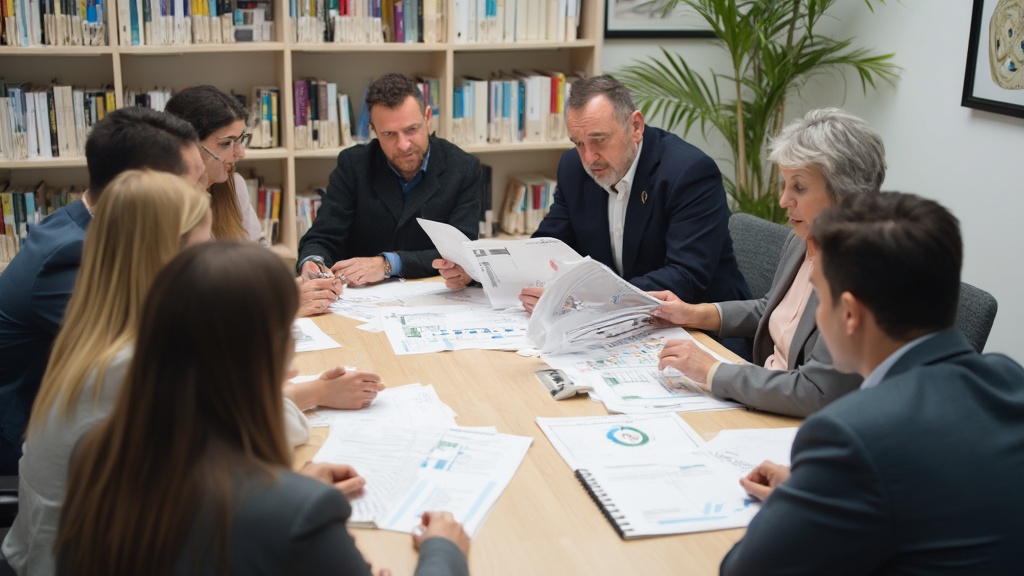
Introduction
In the competitive landscape of direct-to-consumer (D2C) brands, maintaining high-quality standards is not just a goal—it's a necessity. Inspections and audits serve as essential tools for ensuring that products meet rigorous industry standards and consumer expectations. These systematic evaluations, while differing in scope and focus, play a pivotal role in safeguarding brand reputation and enhancing customer satisfaction.
With alarming statistics indicating that a significant percentage of returns stem from preventable quality issues, the importance of effective inspection processes cannot be overstated. By integrating comprehensive inspection strategies, D2C brand owners can not only mitigate risks but also foster operational excellence, paving the way for sustained growth and success. This article delves into the fundamental aspects of inspections and audits, providing valuable insights for brand owners seeking to navigate the complexities of quality control in today's dynamic market.
Understanding Inspections and Audits: A Beginner's Overview
The inspections and audits serve as essential systematic assessments in the process of inspection, intended to evaluate products, processes, and systems to ensure compliance with established criteria and regulations. While evaluations concentrate on particular items or processes, the process of inspection through audits provides a wider appraisal of an organization’s overall practices and compliance. Mastery of the process of inspection is vital for any D2C brand owner intent on upholding high-quality standards and mitigating risks.
Movley’s integrated platform improves tracking of evaluations and operational efficiency, enabling brands to prevent bad batches, reduce returns, and safeguard their reputation. Their key purposes include:
- Guaranteeing product reliability
- Pinpointing areas for improvement
- Ultimately enhancing customer satisfaction
Indeed, as stated by Return Logic, the process of inspection shows that 60% of returns result from avoidable issues, and 94% of consumers have refrained from making a purchase because of a negative review, highlighting the significance of thorough evaluation practices.
In industries such as home and garden, apparel, and electronics, the process of inspection is indispensable for preserving brand reputation and driving operational efficiency. As demonstrated by Maurice Mann, an Amazon seller who regained $1 million in revenue by enhancing his evaluation procedures and raising his star ratings from 3.5 to 4.7, the effect of efficient oversight cannot be overstated. Additionally, as the environment of smaller reporting companies keeps changing, with a significant 9% drop in registrants, the variety of audit firms in this area—where the leading six firms represent merely 30% of the market—emphasizes the competitive aspect of compliance requirements and the necessity of the process of inspection in sustaining operational integrity.
With Movley, brand owners can experience tranquility, concentrating on growth instead of operational difficulties, aware that they are safeguarded from the risks linked to substandard standards and compliance.
Key Elements Inspectors Evaluate During Inspections
During inspections, several critical elements are meticulously assessed to ensure item integrity and adherence to industry guidelines, particularly in the Electrical & Electronic sectors where issues can lead to significant financial losses. Inspectors focus on the following key areas:
-
Item Quality: Inspectors rigorously verify that items align with defined quality standards.
This involves checking for defects, inconsistencies, and strict adherence to specifications, ensuring that only high-quality items reach the consumer. -
First Article Inspections (FAI): Conducting FAI before mass production is essential for verifying product design and ensuring visual, production setup, and performance accuracy.
This step is crucial in preventing costly errors and ensuring compliance with the original design specifications. -
Documentation: The significance of accurate records cannot be overstated.
Comprehensive documentation fosters transparency and traceability throughout the process of inspection.
In the process of inspection, inspectors meticulously review these documents to confirm that proper procedures have been followed, safeguarding against potential liabilities. -
Safety Compliance: In sectors such as electronics, adhering to safety standards is critical.
Inspectors assess whether items comply with established safety regulations, mitigating hazards and ensuring consumer safety.
Recent case studies indicate that neglecting safety compliance can result in serious issues with the items, such as a brand discarding 50,000 units due to overlooked pre-shipment inspections. -
Production Process Efficiency: Evaluating the efficiency of the production process is another vital component of the process of inspection.
Inspectors pinpoint bottlenecks and areas for enhancement, which can greatly improve overall item excellence and operational efficiency. -
Supplier Standards: In a direct-to-consumer (D2C) context, evaluating the reliability and performance of suppliers is essential, as it directly affects the final product delivered to consumers.
Robust supplier quality assessments help mitigate risks associated with preventable returns due to poor quality, thereby enhancing customer retention. -
Comprehensive Reporting: Following assessments, brands receive detailed reports including multimedia elements such as photos and videos.
This comprehensive documentation not only shields the brand from negative feedback but also enables D2C brand owners to act decisively on evaluation results.
Movley’s detailed control report further enhances the process of inspection by providing actionable insights that go beyond basic assessment reports. -
Present Guidelines for 2024: Staying updated on the latest criteria for merchandise evaluations in 2024 is essential for D2C brand proprietors.
Adhering to these criteria not only guarantees product safety and excellence but also improves brand reputation.
By grasping these aspects, D2C brand owners can more effectively manage the challenges of evaluations, applying best practices that not only meet current requirements but also strengthen their operational superiority.
Movley’s customized evaluation services, featuring detailed checklists and an emphasis on excellence, offer a considerable benefit over conventional techniques, guaranteeing that each component meets the utmost excellence criteria.
As Mukut Chakraborty aptly stated,To ensure that each component satisfies the highest quality standards, part evaluation remains an integral part of modern manufacturing.
The Importance of Preparation for Inspections
Thorough preparation for the process of inspection is essential for ensuring compliance and can greatly affect the results. Research indicates that organizations with a structured process of inspection experience a 30% rise in successful evaluation outcomes. Significantly, as per Return Logic, 60% of returns result from avoidable concerns, highlighting the importance of comprehensive evaluations.
Here are several strategic steps to consider:
-
Leverage an Integrated Platform: Utilizing an integrated platform like Movley allows for seamless tracking of evaluations directly within your storefront. This integration not only improves operational efficiency but also ensures that standards checks are systematically documented and monitored.
-
Conduct Internal Reviews: Before an evaluation, carrying out comprehensive internal reviews is crucial to uncover possible problems. This proactive approach, supported by Movley's customized assessments, facilitates the process of inspection to mitigate risks and ensures that all operational standards are met, setting the stage for success.
-
Train Your Team: Comprehensive training for all relevant staff is imperative. Team members should be well-versed in the assessment process and fully understand the criteria that evaluators will consider. Ian White, a former MHRA inspector in the UK, emphasizes the importance of fostering a culture of preparation:
It is important to foster a culture of preparation and ensure that SMEs have the necessary knowledge and support to represent your organization effectively during an inspection.
-
Organize Documentation: Compiling all necessary documentation—including quality control records, compliance certificates, and production logs—is vital. Well-organized documents facilitate a streamlined review process of inspection, allowing inspectors to navigate through your records with ease.
-
Implement Corrective Actions: If your internal reviews uncover deficiencies, take corrective measures to address these issues before the evaluation occurs. This step not only shows dedication to excellence but also reduces the chances of non-compliance findings.
-
Communicate with Inspectors: If relevant, establishing communication with the assessment team ahead of time can be beneficial. Comprehending their individual needs and expectations can aid in establishing rapport and clarifying any uncertainties that may emerge during the evaluation. For example, NSF's recent celebration of Non-GMO Month with certified items illustrates the significance of upholding high standards that conform to regulatory expectations.
By diligently adhering to these preparatory steps and utilizing Movley's top-tier evaluations, businesses can create a more favorable atmosphere for the process of inspection, ultimately leading to improved results and enhanced customer experiences. Movley's tailored inspections play a crucial role in this process, ensuring that businesses can effectively address the issues that lead to returns.
Common Types of Inspections and Their Purposes
A range of typical assessments play vital roles in upholding product standards and compliance across industries:
- Incoming Quality Control (IQC): This evaluation is conducted on materials or components prior to their entry into the production process, ensuring they meet set benchmarks. Implementing IQC can significantly reduce the risk of defects during the process of inspection of the final products.
- In-Process Review (IPR): Carried out during the manufacturing process, this evaluation enables prompt adjustments and enhancements, ensuring uniform standards throughout production. It serves as a proactive measure in the process of inspection to identify issues before they escalate.
- Final Inspection (FI): Prior to items departing the facility, a concluding examination is carried out to ensure that they fulfill all specifications and criteria. This step is critical for customer satisfaction and product reliability, highlighting the importance of the process of inspection, as evidenced by the fact that 94% of customers avoid making a purchase due to a bad review.
- Supplier Audit: Assessing a supplier’s processes and control measures is essential for aligning with company standards. As mentioned by Conor Stewart, a research specialist in health and pharmaceuticals, effective supplier audits can improve your overall assurance. Movley’s digital evaluations and supplier assessments guarantee item standards, offering D2C brands reassurance. By implementing a process of inspection through comprehensive audits, companies can ensure that their suppliers comply with the same quality criteria, ultimately protecting their product integrity. These audits not only verify compliance but also foster trust between brands and suppliers in the process of inspection.
- Compliance Review: Frequently required by regulatory agencies, these evaluations ensure conformity to industry guidelines and legal obligations. The FDA has carried out thorough evaluations of medical device establishments from 2009 to 2024, reaching a high of 2,759 assessments in 2013. This statistic emphasizes the significance of compliance evaluations in preserving item integrity and showcases the trends over time, as demonstrated in the case study titled 'FDA Evaluations of Medical Device Establishments (2009-2024)', which illustrates how these evaluations differ and the essential role they play in assurance of standards.
By comprehending and applying these evaluation types effectively within the process of inspection, businesses can greatly improve item excellence and ensure adherence to relevant standards, ultimately positioning themselves for success in a competitive market. Movley’s dedication to control services is assisting brands like Hash Stash in scaling operations by inspecting over 10,000 units monthly, preventing up to 60% of returns, and fostering customer trust through exceptional communication and detailed reporting. Movley's thorough process of inspection for evaluations not only protects item standards but also provides D2C brands with the reassurance needed to focus on expansion and creativity.
Post-Inspection Actions and Continuous Improvement
After a review, taking decisive actions is crucial for translating findings into tangible improvements that enhance quality control. However, D2C brand owners often face barriers such as a lack of knowledge, cultural differences, and communication issues that can hinder the effective implementation of these actions. Here are key steps to consider:
-
Review Findings: Conduct a thorough analysis of the results, including compliance-related product labeling and lot codes, as part of the process of inspection to identify both strengths and weaknesses within your processes. Understanding these elements is essential for informed decision-making, especially in light of the challenges posed by insufficient statistical knowledge.
-
Implement Corrective Actions: Promptly address any deficiencies identified during the process of inspection, such as sizing errors and mislabeled units, which are critical for softlines brands to reduce return rates and enhance customer satisfaction.
This may involve refining workflows, providing additional training for staff, or enhancing your overall control measures. Overcoming cultural differences in understanding quality standards can be vital to prevent future occurrences of the same issues. -
Communicate Findings: Transparency is vital; sharing the outcomes of the evaluation with all relevant teams fosters a culture of accountability.
Effective communication can help bridge gaps caused by differing interpretations of evaluation results, ensuring that all stakeholders are engaged in the improvement process. Testimonials from pleased clients, including those commending Movley's detailed evaluations and significant suggestions, act as social proof of the efficacy of these actions. -
Monitor Progress: Establish clear metrics to track the effectiveness of the implemented corrective actions over time.
Regular monitoring helps ensure that improvements are not only made but also sustained, facilitating ongoing enhancement. Addressing communication issues during this phase can further enhance the effectiveness of tracking and reporting. For instance, case studies from clients like Hash Stash and The Mindful Collective, which showcase significant improvements in operational efficiency and growth metrics, highlight the success of this approach. -
Plan for Future Inspections: Utilize insights from the current process of inspection to refine your approach for future assessments.
Adjusting strategies based on past experiences, while being mindful of the barriers to statistical thinking, will bolster your readiness and improve outcomes. Firms such as Hash Stash and The Mindful Collective have shown the success of such proactive strategies, resulting in considerable operational efficiency and growth.
By instilling a mindset of continuous improvement and recognizing the obstacles to effective control, businesses can greatly enhance their processes. This proactive approach not only results in superior offerings but also enhances customer satisfaction, ultimately driving long-term success. Recent findings suggest that organizations that emphasize these post-inspection actions tend to surpass their peers in attaining consistent standards and operational excellence, despite the challenges they encounter.
Furthermore, centralized documentation management plays a pivotal role in ensuring that compliance-related product labeling and lot codes are easily accessible, thereby supporting these quality control efforts.
Conclusion
In the rapidly evolving realm of direct-to-consumer brands, the significance of rigorous inspections and audits cannot be overstated. These systematic evaluations are essential for maintaining high-quality standards, ensuring compliance, and safeguarding brand reputation. By implementing effective inspection processes, D2C brands can significantly reduce the risk of preventable quality issues, which, as highlighted, account for a staggering 60% of product returns.
This proactive approach not only enhances customer satisfaction but also fosters operational excellence.
The article has emphasized the critical components of inspections, including product quality, safety compliance, and supplier quality, all of which play a vital role in delivering reliable products. Moreover, the importance of thorough preparation and strategic post-inspection actions has been underscored as pivotal for continuous improvement. By leveraging integrated platforms like Movley, brands can streamline their inspection processes and ensure that they are equipped to meet the challenges of today’s market.
Ultimately, the integration of comprehensive inspection strategies is not merely a regulatory requirement; it is a strategic imperative that can drive growth and success for D2C brands. By committing to quality control and continuous improvement, brands can not only prevent costly returns but also build lasting trust with their customers, positioning themselves favorably in an increasingly competitive landscape. As the market continues to evolve, prioritizing quality through meticulous inspections and audits will be essential for sustainable growth and brand loyalty.