How to Successfully Complete Level 2 PPAP Submissions: A Step-by-Step Guide
Master the essentials of level 2 PPAP submissions with our comprehensive step-by-step guide.
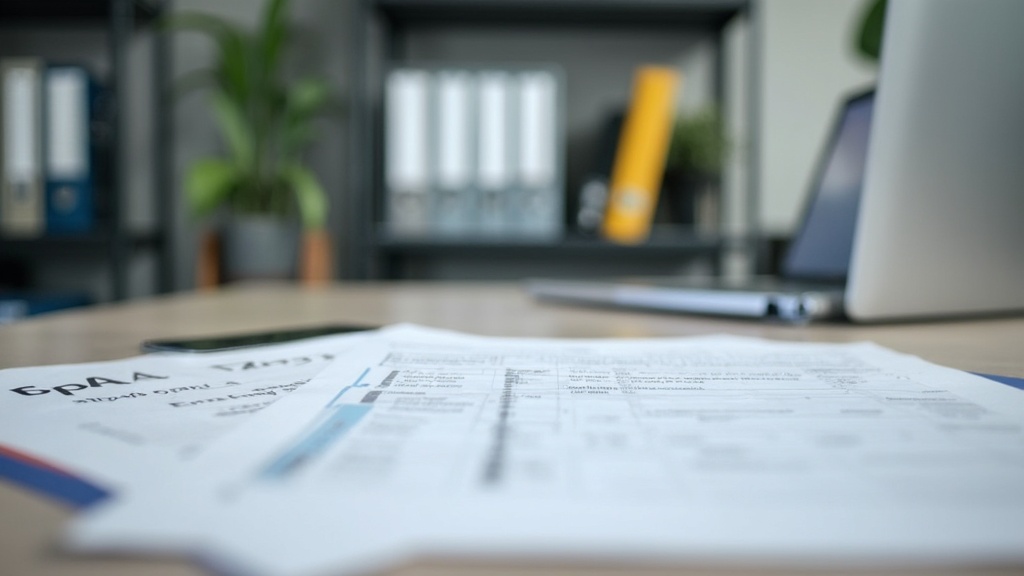
Introduction
In the highly regulated automotive industry, maintaining quality standards is paramount for suppliers aiming to secure their place in a competitive market. The Production Part Approval Process (PPAP) serves as a vital mechanism to ensure that all manufacturing processes and components meet the rigorous specifications set forth by customers.
With Level 2 PPAP submissions requiring meticulous documentation and thorough evaluations, suppliers must navigate a complex landscape to achieve approval. This article delves into the intricacies of the PPAP process, outlining essential steps for preparing submissions, common challenges faced, and best practices that can enhance compliance and operational efficiency.
By understanding these elements, suppliers can better position themselves for success, ultimately contributing to improved product quality and customer satisfaction.
Understanding the PPAP Process and Its Importance
The Production Part Approval Process serves as a critical framework within the automotive sector, ensuring that suppliers meet stringent quality standards prior to initiating mass production. At level 2 ppap, submissions necessitate a thorough assessment of both the manufacturing method and the components being produced. Key documentation for the level 2 ppap includes:
- Design Records
- Engineering Change Documents
- Process Flow Diagrams
These documents are essential, not only in demonstrating the supplier's ability to produce parts in accordance with client specifications but also in establishing a robust quality assurance framework. Proper documentation mitigates potential errors that could lead to costly production setbacks. Companies like Micron exemplify the benefits of adhering to high calibration standards, providing rapid turnaround times for calibration services and personalized service.
As a woman-owned and minority-owned small business, MicronPA's commitment to high standards is enhanced by ongoing team training, underscoring the significance of effective PPAP procedures in maintaining quality and reliability in production.
Similarly, Movley offers custom quality checks tailored to unique products, ensuring that every aspect of quality assurance is addressed. Their on-site inspections help prevent bad batches and minimize returns, ultimately protecting brand reputation. According to Return Logic:
- 60% of returns are due to preventable quality issues
- 94% of customers have avoided making a purchase due to a bad review
With Movley's efficient and detailed inspection services, D2C brand owners can achieve operational efficiency while safeguarding the integrity of their products. Movley provides peace of mind, allowing your team to focus on building the business rather than dealing with operational challenges. Additionally, their customized checklist support guarantees that quality checks are specifically created for your product, enhancing the overall quality assurance.
Step-by-Step Guide to Preparing and Submitting Level 2 PPAP Packages
Successfully preparing and submitting a level 2 PPAP package requires a structured approach. Follow these essential steps to ensure compliance and enhance your manufacturing methods:
-
Gather Required Documentation: Assemble all necessary documents, including Design Records, Process Flow Diagrams, and the Process Failure Mode and Effects Analysis (PFMEA). Each document must be current and accurately represent the production methods to avoid discrepancies.
-
Conduct a Capability Study: Carry out a capability analysis to demonstrate that your manufacturing methods can reliably produce parts that meet specifications. Utilize statistical analysis and sampling techniques to validate your findings, as this is crucial for establishing reliability. As a standardized process, this approach assists suppliers in consistently producing components that satisfy client specifications.
-
Complete the Dimensional Results Report: Accurately measure the critical dimensions of the produced parts and document the results meticulously. This report should clearly indicate how these measurements align with the design specifications, providing evidence of compliance.
-
Review and Validate Documentation: Engage a quality assurance team member to review all documentation before sending. Ensuring accuracy and completeness at this stage is vital for preventing delays caused by missing or incorrect information, which can impede approval.
-
Submit the Level 2 PPAP: With all documents validated, submit your complete level 2 PPAP to your client for approval. Follow closely any particular guidelines for delivery provided by the client to reduce potential problems. The Part Submission Warrant (PSW) form outlines the complete part approval process and is necessary for each part number, including the rationale for filing and the category of documents provided, guaranteeing clarity in your filing.
-
Follow Up: After sending, keep open lines of communication with the customer to address any questions or concerns that may arise regarding your entry. Prompt replies can greatly aid in creating a more efficient and quicker approval process.
By following these steps, you can guarantee that your level 2 PPAP documentation is thorough and meets essential criteria, ultimately paving the way for successful production results. Significantly, by automating the production part approval system with tools like MBDVidia, organizations such as GE Appliances have decreased report generation errors by 77%, emphasizing the effect of efficient methods on quality assurance.
Common Challenges in Level 2 PPAP Submissions
When preparing Level 2 documentation, suppliers frequently encounter several critical challenges that can impede their approval process:
-
Incomplete Documentation: A primary issue is the provision of incomplete or outdated documentation. Ensuring that all necessary documents are current and thoroughly completed is essential, as studies have shown that documentation completeness significantly influences level 2 PPAP approval rates, with statistics indicating that entries with complete documentation have a 30% higher approval rate. Movley’s tailored checklist support ensures that suppliers have the right documentation in place, addressing this challenge directly.
-
Miscommunication with Customers: Misunderstandings regarding entry requirements can lead to rejection. It is essential to keep open channels of communication with customers to clarify any uncertainties prior to sending. As Thomas J. Bossard from Production Control & Logistics advises,
Please contact Tom Bossard if you have any questions,
reinforcing the need for proactive engagement. The recent Nexteer Global Supplier Conference emphasized that effective communication aligns suppliers with strategic goals, highlighting the importance of clarity in the level 2 PPAP process. -
Inadequate Manufacturing Capability: Submissions may fail if the production method does not meet the necessary capability standards. Providers should perform thorough capability assessments to recognize and address any deficiencies before presenting. Here, Movley’s dedicated quality team plays a pivotal role in ensuring compliance with evolving requirements through level 2 PPAP by providing personalized inspection planning and real-time monitoring to help manufacturers meet these standards.
-
Tight Deadlines: Suppliers often face stringent due dates for proposals. To alleviate the stress of last-minute requests, planning ahead and starting the documentation effort early can be highly effective. Engaging a quality partner like Movley allows brands to focus on their core operations while ensuring that quality inspections—up to 10,000 units per month—are conducted efficiently, thereby minimizing the risk of returns. For instance, Hash Stash has effectively expanded its operations with Movley’s assistance, illustrating how efficient quality control can result in operational effectiveness.
By acknowledging these challenges and incorporating the changing needs and communication tactics, suppliers can proactively adopt strategies to tackle them, facilitating a more streamlined process while utilizing top-tier inspections to avert manufacturing problems and improve client experience.
Best Practices for Successful Level 2 PPAP Submissions
To enhance the likelihood of successful Level 2 PPAP entries, consider implementing the following best practices:
-
Engage Early with Customers: Establishing open lines of communication with customers at the outset is crucial. This interaction helps clarify expectations and requirements, ensuring alignment from the beginning.
-
Utilize Checklists and Self-Check Wizards: Develop comprehensive checklists alongside Movley’s supplier self-check wizards to guarantee that all required documentation is gathered and completed prior to submission. This proactive measure reduces the risk of missing critical items that could cause delays, while also streamlining product development and production inspections.
-
Verify Compliance: Ensure that compliance-related product labeling and lot codes are verified and managed centrally. This organization keeps all documentation in one place, enhancing traceability and compliance assurance.
-
Regular Training: Invest in ongoing training for your team focused on PPAP requirements and quality assurance methods. Keeping your team well-informed about the latest standards enhances the overall quality of contributions. The most current NCCN Guidelines, which are publicly available, should be a key resource in this training.
-
Implement Continuous Improvement: After each entry, carry out a comprehensive evaluation of the procedure to pinpoint areas for enhancement. Learning from past experiences is vital for streamlining future entries and achieving greater success. The NCCN Harmonized Guidelines™ initiative demonstrates how adapting guidelines can improve processes and outcomes in resource-constrained settings.
-
Leverage Digital Tools and Dedicated Quality Teams: Utilize digital platforms and tools to manage documentation and monitor progress effectively. Movley’s dedicated quality service team can assist in building your inspection plan, recommending checks, and monitoring inspections in real-time. This not only improves organization but also increases efficiency throughout the entire process.
-
Emphasize Preventative Inspections: Recognize that 60% of returns are due to preventable quality issues. By conducting on-site inspections, you can catch these issues early, significantly reducing the likelihood of returns and enhancing customer satisfaction.
By adopting these best practices, suppliers can significantly improve their chances of successful Level 2 PPAP submissions while fostering stronger relationships with their customers and preventing manufacturing issues that could harm customer experience. Furthermore, think about employing visual elements such as sample inspections and compliance documentation to better elucidate these procedures.
Post-Submission: What to Expect and Next Steps
Upon submitting your Level 2 PPAP package, you can anticipate the following stages in the process, including the crucial approval of the inspection plan:
-
Review Period: The client will commence an evaluation of your submission, which may differ in length from several days to weeks, dependent on their internal procedures and workload.
-
Approval of Inspection Plan: Once you approve our inspection plan, our service team will coordinate the requirements with our inspectors and get to work. This step is essential for ensuring that all necessary inspections align with customer expectations.
-
Feedback or Requests for Additional Information: It’s essential to be prepared for potential feedback or requests for supplementary documentation. Timely responses to these inquiries are crucial for maintaining momentum in the approval process.
-
Approval or Rejection Notification: After the review, you will receive a notification regarding the status of your submission. In the event of a rejection, the client will provide specific reasons for the decision, enabling you to make necessary adjustments.
-
Implementing Changes: Should modifications be necessary, work closely with the client to fully understand their feedback. This collaboration is key to ensuring that your processes or documentation are adjusted accordingly.
-
Final Approval and Production Kick-off: Once you receive final approval, you can confidently proceed with production, assured that your parts comply with the outlined specifications.
It's noteworthy that a Production Part Approval Process, specifically level 2 ppap, typically requires a Part Submission Warrant (PSW) for each part number, ensuring that all customer requirements are fulfilled. As Mari Luke states, "A Level 3 Production Part Approval Process requires that you submit all the documentation of a Production Part Approval Process except elements 15 and 16, which are the master sample and checking aids." This highlights the importance of understanding documentation expectations.
Additionally, the clarity on documentation requirements, as illustrated in the case study on Default Submission Level for PPAP, aids manufacturers in preparing accurate submissions for PPAP.
Understanding these expectations post-submission equips suppliers to effectively manage their production timelines and foster strong relationships with their customers.
Conclusion
Navigating the Production Part Approval Process (PPAP) is essential for suppliers in the automotive industry striving to meet rigorous quality standards. This article provided a comprehensive overview of the PPAP process, highlighting the importance of meticulous documentation and adherence to best practices for Level 2 submissions. Key steps such as:
- Gathering necessary documents
- Conducting process capability studies
- Maintaining open communication with customers
were emphasized as critical components for achieving successful approval.
The challenges faced during the submission process, including:
- Incomplete documentation
- Miscommunication
can significantly hinder approval rates. By addressing these issues proactively and implementing best practices such as:
- Utilizing checklists
- Engaging dedicated quality teams
suppliers can enhance their chances of success. Continuous improvement and training further contribute to a culture of quality that is vital in today’s competitive market.
Ultimately, a well-executed PPAP not only streamlines production but also strengthens supplier-customer relationships, fostering trust and reliability. By understanding and effectively managing each stage of the PPAP process, suppliers can position themselves for success, contributing to higher product quality and increased customer satisfaction. As the automotive landscape continues to evolve, embracing these practices will be crucial for suppliers aiming to thrive in a demanding industry.