How to Identify and Fix Defeitos in Your Manufacturing Process: A Step-by-Step Guide
Learn how to identify and fix manufacturing defects for improved quality and customer satisfaction.
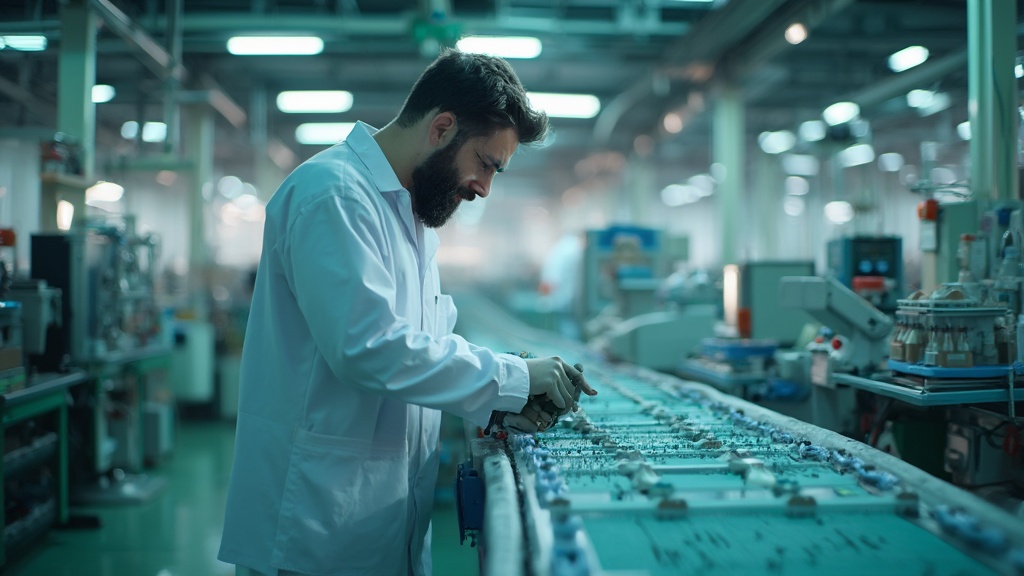
Introduction
In the competitive landscape of manufacturing, maintaining product quality is paramount to safeguarding brand reputation and ensuring customer satisfaction. Common manufacturing defects, ranging from dimensional errors to functional flaws, can have significant repercussions if not addressed proactively.
By integrating robust quality control systems and leveraging advanced technologies, manufacturers can not only detect and rectify these defects but also foster a culture of continuous improvement.
This article delves into the various types of manufacturing defects, effective strategies for their identification and resolution, and the critical role that employee engagement and data-driven approaches play in enhancing overall quality performance.
Through a comprehensive understanding of these elements, organizations can position themselves for success in an increasingly demanding market.
Understanding Common Manufacturing Defects
Defeitos na produção podem impactar significativamente os padrões do produto e a imagem da marca, exigindo um sistema de garantia forte. Movley’s comprehensive inspection checklists address numerous quality issues effectively, offering tailored solutions that set it apart from traditional inspection methods. Common defeitos that manufacturers encounter include:
-
Dimensional Errors: These arise when items deviate from specified measurements, often due to machinery inaccuracies or human error during assembly. The implications of defeitos dimensionais can be severe, leading to costly rework and diminished customer satisfaction. The solution aids in reducing these risks by improving data gathering to track deviations effectively, ensuring that each item meets precise specifications.
-
Surface Flaws: This category encompasses scratches, dents, and discoloration that may occur during handling or processing. Defeitos na superfície detractam da atratividade estética do item e podem sinalizar problemas de qualidade subjacentes, afetando a confiança do consumidor. By utilizing the comprehensive monitoring services, manufacturers can identify these defeitos early in the manufacturing process, allowing for timely corrections that maintain item integrity.
-
Defeitos Materiais: Defeitos materiais surgem da utilização de materiais de qualidade inferior, o que pode comprometer o desempenho e a durabilidade do produto. Regular assessments of suppliers and materials, backed by strong data analysis, are crucial to reduce this risk and guarantee high-quality outputs. The platform allows manufacturers to maintain high standards by tracking material quality throughout the supply chain.
-
Defeitos de Montagem: Problemas, como componentes soltos ou encaixes inadequados, muitas vezes surgem devido à falta de monitoramento rigoroso nos processos de montagem. The data-driven maintenance strategies improve oversight, aiding in preserving quality and minimizing assembly errors. By implementing tailored checklists, the company ensures that each assembly step is thoroughly inspected.
-
Defeitos Funcionais: Esses defeitos impedem a funcionalidade pretendida de um produto e geralmente são identificados durante os testes de garantia. The proactive detection and correction of these issues are essential for upholding customer satisfaction and loyalty, supported by analytics that can foresee potential failures.
The platform has shown considerable value, as demonstrated by case studies revealing how brands such as Maurice Mann’s Amazon store regained $1 million in revenue and enhanced star ratings through thorough inspections. Such success stories emphasize the significance of a thorough control strategy in minimizing returns and improving customer retention by addressing preventable defeitos. A recent report highlights that 91% of manufacturing maintenance professionals prioritize enhancing data collection and analysis capabilities, reflecting a significant shift towards proactive, data-driven maintenance strategies.
As noted by Ankush Malhotra, Group CEO at Element Logic, > Predictive maintenance is becoming a need, not a want, especially as skilled labor is hard to come by and retain. By thoroughly grasping these typical issues and incorporating data-informed strategies through platforms such as Novelty, manufacturers can take the initial vital step toward effective control and ongoing enhancement in their production processes.
Effective Strategies for Detecting and Fixing Defects
To effectively identify and correct manufacturing issues, consider implementing the following strategies:
-
Regular Standards Audits: Conducting periodic audits of production processes is crucial for identifying deviations from established performance standards. This proactive approach not only facilitates early detection of defeitos but also fosters a culture of continuous improvement. As Shigeru Mizuno aptly stated,
Excellence needs to be constantly improved, but it is just as necessary to make sure that it never deteriorates.
Quality management not only creates customer trust and loyalty but drives continuous improvement and innovation, making regular audits an essential practice. The customized inspection standards, created specifically for each category, exemplify this approach, ensuring that unique characteristics are considered in the auditing process. -
Invest in Technology: Utilizing advanced inspection technologies, such as automated visual inspection systems and machine learning algorithms, can significantly improve flaw detection capabilities. Movley utilizes top-tier inspections that evaluate products with enhanced speed and precision in contrast to conventional manual inspections, ensuring that standards are maintained throughout the production process.
-
Training and Development: It is essential that employees are knowledgeable about standards and issue identification. Regular training workshops can bolster their skills in identifying and addressing issues promptly, thereby reducing the likelihood of defeitos slipping through the cracks. Movley’s commitment to empowering exceptional teams highlights the importance of equipping staff with the necessary skills to maintain high standards.
-
Feedback Loops: Establishing a system for gathering feedback from both customers and employees regarding product standards is essential. This feedback can yield valuable insights into potential issues that may not be immediately apparent during production, enabling timely interventions. Engaging with customers, as seen in Movley’s case studies, can further enhance understanding of quality issues.
-
Root Cause Analysis: Upon identifying issues, conducting a thorough root cause analysis is vital. This process uncovers the underlying reasons for defeitos and informs the implementation of corrective actions aimed at preventing future occurrences. Movley’s rich experience with brands demonstrates how effective root cause analysis can lead to significant improvements and revenue recovery.
-
Supplier Management: Collaborating closely with suppliers to ensure that materials meet strict performance standards is essential. Regular evaluations and standards checks can prevent substandard materials from entering the production line, thereby maintaining the integrity of the final product. The proactive inspections conducted by the company help safeguard against such risks, protecting brands from negative reviews and ensuring customer satisfaction.
-
Standards Checklists: Implementing standards checklists as essential tools in production can provide a systematic approach to management and control. The company collaborates closely with brands to develop tailored checklists that meet particular product requirements, aiding in identifying mistakes before they grow.
By implementing these approaches, producers can greatly reduce the occurrence of defeitos, improve product standards, and ultimately enhance overall customer satisfaction. Significantly, according to Return Logic, 60% of returns are due to avoidable issues, highlighting the importance of proactive control measures. The function of technology in error identification cannot be exaggerated; as demonstrated by firms that have effectively incorporated innovative management solutions, their strategy is a transformative factor for producers striving for excellence.
To learn more about how movies can help your brand achieve these goals, [Talk to Sales].
Implementing Quality Control Systems
To establish a robust quality control system that ensures consistent product quality and minimizes defects, follow these critical steps:
-
Define Excellence Standards: Begin by establishing clear excellence standards that align with industry benchmarks and meet customer expectations. Document these standards thoroughly and ensure they are conveyed efficiently to all employees, fostering a shared understanding of objectives.
-
Develop Inspection Protocols: Create detailed inspection protocols that specify the timing and methodology for product inspections throughout the manufacturing process. Clearly define acceptance and rejection criteria to ensure that all team members are aligned on standards expectations.
-
Utilize Statistical Process Control (SPC): Implement Statistical Process Control techniques to monitor production processes in real-time. By employing statistical methods to analyze process data, manufacturers can swiftly identify variations that may indicate potential defeitos, allowing for proactive interventions.
-
Continuous Improvement: Cultivate a culture of continuous improvement within your organization. Motivate staff to offer input and propose improvements to control procedures. Consistently assess and revise standards and protocols based on performance data and insights gained from staff contributions. This aligns with the leadership's aim to enhance performance, standards, and pride in workmanship while reducing failure causes.
-
Documentation and Reporting: Maintain meticulous documentation of all control activities, including inspection results and any corrective actions taken. This documentation is vital for tracking improvements over time and ensuring accountability across the manufacturing operation.
Integrating the inspection services can further enhance this framework, as they offer customized checks that address distinct item requirements, significantly decrease the chances of defeitos, and assist in preventing up to 60% of returns. Furthermore, the supplier audits conducted by the company are essential in assessing partners, ensuring standards and reliability, and promoting long-term collaboration. Customer testimonials emphasize the effectiveness of these services, with one client stating, "Movley assisted me in recovering $1 million in revenue by enhancing my product standard and reducing returns."
By leveraging these best-in-class inspections, D2C brand owners can protect their brand reputation and enhance customer experiences, ensuring that negative reviews—which deter 94% of potential buyers—are minimized. Ultimately, embracing a proactive control approach not only fosters a culture of pride in workmanship but also positions brands for operational excellence in today's competitive landscape.
Engaging Employees in Quality Improvement
Involving employees effectively in enhancement is essential for fostering a culture that prioritizes excellence. As Keuten, Senior Vice President and Microsoft Alliance Lead at Rightpoint, mentions, "It’s going to be a wonderful space to work in over the next decade," highlighting the significance of employee engagement in promoting excellence initiatives. Here are several strategies that can enhance this engagement:
-
Empower Employees: Encourage a sense of ownership among employees by empowering them to identify and report defeitos. Cultivating a non-punitive environment where concerns can be shared safely is critical. This method not only boosts accountability but also results in proactive problem-solving, aligning with Movley's strategy of preventing returns before they happen through customized checks. Considering that 60% of returns result from preventable issues, this empowerment is essential.
-
Incentivize Excellence Contributions: Implementing incentive programs that recognize and reward employees for their contributions to excellence improvement can significantly boost morale and motivation. Honoring achievements encourages a shared dedication to excellence, motivating teams to prioritize high standards in their work. Incorporating gamification elements can further motivate employees, making the engagement process more interactive and rewarding.
-
Cross-Functional Teams: Form cross-functional teams to tackle specific excellence challenges. By uniting different viewpoints, organizations can utilize diverse knowledge, resulting in creative solutions and enhanced cooperation among departments, similar to how the committed customer service team collaborates with clients to develop effective inspection plans. The organization's on-site inspections play a crucial role in these collaborative efforts.
-
Regular Training: Offering continuous training and development opportunities centered on management and identificação de defeitos guarantees that employees are well-informed about best practices. This investment in skill enhancement enables them to contribute effectively to improvement initiatives, supporting the preventive measures the company implements through on-site inspections.
-
Feedback Mechanisms: Establish robust feedback systems that enable employees to share their insights on processes and suggest enhancements. Regularly reviewing this feedback and implementing actionable changes can drive continuous improvement and foster a culture of engagement. Personalizing platforms and establishing clear communication plans can optimize HR technology for engagement, enhancing the effectiveness of these strategies.
By actively involving employees in improvement efforts and integrating Movley’s services, manufacturers can create a proactive environment that not only reduces defeitos but also enhances overall operational efficiency, aligning with the evolving landscape of manufacturing excellence and ensuring a positive customer experience while protecting brands from negative reviews.
Monitoring and Evaluating Quality Performance
To effectively monitor and evaluate performance standards, it is crucial to implement a systematic approach consisting of the following key steps:
-
Establish Key Performance Indicators (KPIs): Begin by defining KPIs that are closely aligned with your performance objectives. Metrics such as defect rates, which average around 2% in high-performing manufacturing sectors, customer complaints, and return rates are vital as they provide clear insights into your performance regarding defeitos. Importantly, as per Return Logic, 60% of returns arise from avoidable issues—an area where proactive measures, such as Movley’s on-site inspections, can have substantial impact. It's essential to select indicators that reflect both the effectiveness and efficiency of your processes.
-
Regular Reporting: Create a strong reporting system that consistently monitors performance metrics over time. Consistently produced reports will assist in recognizing long-term trends and emphasizing areas needing enhancement, ensuring that standards remain a focal point in your operations. As noted in the case study “Quotes on Performance Reporting,” effective visualization of these metrics can significantly enhance understanding and decision-making. This is especially crucial when considering that 94% of customers avoid making purchases based on bad reviews, underscoring the need for vigilance in protecting your brand reputation.
-
Conduct Root Cause Reviews: Whenever defects happen, it's important to conduct thorough root cause reviews. This systematic process enables teams to comprehend the underlying reasons for performance defeitos and devise strategies to prevent their recurrence. Documenting these findings fosters a culture of transparency and accountability, which aligns with the objectives and key results (OKRs) framework for clarifying goals and measuring progress.
-
Benchmarking: Compare your performance against industry benchmarks to understand how your manufacturing processes stack up against competitors. This analysis can uncover valuable opportunities for enhancement and inform strategic decisions moving forward.
-
Continuous Feedback Loop: Establish a continuous feedback loop that incorporates data from performance evaluations into future improvement initiatives. The company's on-site evaluations play a crucial role here, assisting in identifying issues early and preventing up to 60% of returns. This iterative process ensures that your management efforts remain dynamic, responsive, and aligned with evolving business objectives. Additionally, by leveraging Movley’s services, your team can focus on building the business rather than being bogged down by operational challenges, providing peace of mind and allowing for strategic growth.
While metrics serve as a powerful tool for monitoring performance, it's imperative to remember the wisdom of Ronald Coase:
If you torture the data long enough, it will confess to anything.
Thus, while striving for measurable outcomes, be cautious not to let metrics overshadow other critical aspects of management. By implementing these strategies, manufacturers can ensure that their quality improvement efforts are effective and contribute meaningfully to overarching business goals.
Conclusion
In the realm of manufacturing, ensuring product quality is not merely a necessity but a strategic imperative. This article has explored the various types of manufacturing defects that can jeopardize both brand reputation and customer satisfaction, highlighting the importance of robust quality control systems. From dimensional errors and surface flaws to functional defects, understanding these common issues is the first step in mitigating their impact.
Implementing effective strategies for detecting and addressing defects is crucial. Regular quality audits, investment in advanced technologies, and employee engagement all play pivotal roles in fostering a culture of continuous improvement. By equipping employees with the necessary training and tools, organizations can create an environment where quality is prioritized, ultimately enhancing operational efficiency and customer trust.
Furthermore, establishing a comprehensive quality control system is essential for maintaining high standards. Defining clear quality benchmarks, developing thorough inspection protocols, and utilizing data-driven approaches like Statistical Process Control can help manufacturers proactively manage quality challenges. The integration of platforms such as Movley exemplifies how technology can support these efforts, leading to significant reductions in preventable defects and returns.
In conclusion, the path to manufacturing excellence is paved with a commitment to quality at every level of the organization. By embracing proactive measures, engaging employees, and leveraging advanced technologies, manufacturers can not only improve product quality but also safeguard their brand's reputation in a competitive marketplace. As the industry continues to evolve, those who prioritize quality will undoubtedly position themselves for long-term success.