How to Conduct a Successful Control Inspection: A Step-by-Step Guide
Discover essential steps for effective control inspection to enhance product quality and customer satisfaction.
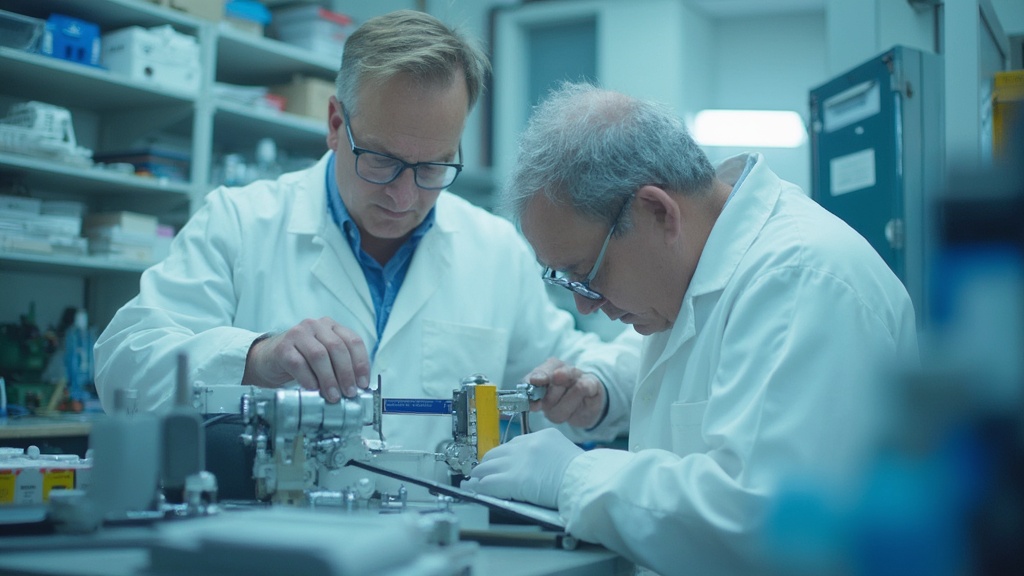
Introduction
In an increasingly competitive marketplace, the significance of quality control inspections has never been more pronounced. Industries ranging from manufacturing to electronics rely on these inspections to uphold product standards and foster customer trust. By implementing a robust quality control framework, companies can not only mitigate the risks of defects but also enhance their operational efficiency.
Movley’s integrated platform exemplifies how technology can streamline the inspection process, enabling direct-to-consumer brands to customize quality checks that align with their unique product specifications. This proactive approach not only prevents costly returns but also solidifies a brand's reputation in the eyes of discerning consumers.
As the following sections delve into best practices, preparation strategies, and common pitfalls, it becomes clear that effective quality control is not merely a regulatory requirement; it is a cornerstone of sustainable business success.
The Importance of Quality Control Inspections in Industry
Control inspection evaluations are essential across various industries, including manufacturing, apparel, and electronics. They play a pivotal role in control inspection to ensure that products meet established standards, thus reducing the risk of defects and improving client satisfaction. With Movley’s integrated platform, D2C brand owners can seamlessly perform control inspection on evaluations, enabling operational enhancements and customized quality checks tailored to unique products.
By conducting control inspections regularly, companies can identify potential issues early—preventing up to 60% of returns and safeguarding their brand reputation, as 94% of customers consider reviews before making a purchase. Furthermore, control inspection evaluations assist in identifying missing units, ensuring precise shipment counts and preventing discrepancies. The success narratives of brands such as Maurice Mann, who regained $1 million in revenue, and The Mindful Collective, which expanded to a 7-figure enterprise, illustrate how efficient oversight processes aid in overall achievement and sustainability.
Ultimately, nurturing trust and reliability among consumers is essential, and Movley’s top-notch evaluations serve as a control inspection, offering peace of mind and guaranteeing that manufacturing problems do not affect customers while improving their overall experience.
Preparing for a Successful Quality Control Inspection
To prepare for a quality control inspection, begin by reviewing relevant documentation such as previous evaluation reports, product specifications, and compliance standards. It's crucial to endorse the assessment strategy, enabling our service group to align the requirements with examiners efficiently. Assemble a dedicated evaluation team trained in the specific criteria, and communicate clear expectations to all stakeholders to minimize disruption to operations.
Plan the control inspection thoughtfully and gather necessary tools and equipment, such as checklists and measuring devices, to facilitate an efficient process. After the evaluation, you will receive a comprehensive report that includes photos, videos, and detailed assessment instructions, ensuring you can act on the results. With Movley’s tailored quality assessments, created in partnership with your quality personnel, you can ensure that evaluations are customized to your unique products, thereby enhancing operational efficiency and safeguarding your brand from negative feedback and customer experiences.
This proactive approach provides peace of mind, knowing that you are taking steps to prevent bad batches and returns.
Step-by-Step Process of Conducting a Quality Control Inspection
- Define Inspection Criteria: Establish clear criteria based on product specifications and regulatory requirements.
- Approve the Assessment Plan: Review and endorse the assessment plan to ensure that all necessary requirements are coordinated with our service group before proceeding.
- Conduct a Pre-Examination Meeting: Assemble the evaluation group to discuss roles, responsibilities, and the assessment agenda.
- Perform the control inspection: Utilize tailored checklists designed specifically for your product, ensuring that every unique aspect is evaluated. Document findings meticulously, and coordinate with our service team to ensure all requirements are met for the control inspection.
- Analyze Review Results: Review the comprehensive data collected during the evaluation, which includes multimedia elements like photos and videos, to identify trends, defects, or areas for improvement. This thorough analysis is crucial for protecting your brand from negative reviews and enhancing customer experiences.
- Report Findings: Compile a detailed report that outlines the evaluation results, including any nonconformities and recommended corrective actions, offering insights that are specific to your product category. Unlike conventional approaches, Movley offers a more thorough examination with customized suggestions.
- Follow Up: Arrange follow-up evaluations to ensure that corrective actions have been implemented and are effective, thus reinforcing your commitment to quality assurance and customer satisfaction.
Get Started: Reach out to us today to simplify your evaluation process and safeguard your brand.
Tips and Best Practices for Effective Quality Control Inspections
- Use Technology: Leverage Movley's integrated platform, which features real-time tracking capabilities to streamline the evaluation process for control inspection and enhance data accuracy.
- Involve All Stakeholders: Engage individuals from various departments to gain diverse viewpoints on performance issues, which Movley emphasizes through its detailed reporting and communication. For example, one client observed, 'The thoroughness and precision of their evaluations have been a game changer.'
- Continuous Training: Provide ongoing education for evaluation groups to keep them updated on best practices and new technologies, ensuring they are equipped to handle the proactive control inspection measures that Movley employs to prevent up to 60% of returns.
- Document Everything: Maintain detailed records of evaluations and findings to track progress and inform future assessments, fostering transparency and trust in the control inspection process, as evidenced by customer testimonials praising Movley's thoroughness. One user stated, "I was able to work with the factory to fix all the problems on my product thanks to the detailed feedback from Movley."
- Encourage Feedback: Create an environment where team members can share insights and suggestions for enhancing the review process, contributing to a culture of continuous improvement that Movley embodies as it supports brands like Hash Stash in scaling operations sustainably.
Avoiding Common Mistakes in Quality Control Inspections
- Neglecting Preparation: Failing to prepare adequately can lead to oversight and inefficiencies during the evaluation. Movley's platform connects directly with your storefront, enabling seamless monitoring of evaluations and ensuring that all aspects are covered. This proactive strategy aids in avoiding returns, as 60% of returns arise from avoidable issues.
- Ignoring Documentation: Not reviewing previous reports can result in repeating past mistakes. Our committed customer support team offers customized evaluation planning and oversees the process in real-time, assisting you in learning from previous assessments.
- Rushing the Process: Taking shortcuts during evaluations can compromise quality. Ensure thoroughness over speed; our detailed reports include photos, videos, and guidelines for control inspection that empower you to make informed decisions swiftly.
- Lack of Communication: Failing to communicate with group members can lead to misunderstandings and incomplete inspections. With our high-touch service, you'll always have access to your excellent team for any questions or concerns.
- Inconsistent Standards: Not adhering to established excellence standards can lead to variability in product standards. Maintain uniformity to guarantee dependability; our proactive assurance practices, including on-site evaluations, help prevent problems that could result in unfavorable feedback and customer discontent. Once you approve our control inspection plan, our service team will coordinate the requirements with our inspectors and get to work, ensuring thorough inspections and quality assurance.
Conclusion
Quality control inspections are integral to maintaining product standards and fostering customer satisfaction across various industries. By implementing a comprehensive quality control framework, companies can significantly reduce defects and prevent costly returns, as demonstrated by success stories from brands that have effectively utilized these inspections. Movley’s integrated platform stands out by offering tailored inspection processes that not only streamline operations but also enhance brand reputation through proactive measures.
Preparation is key to a successful inspection process. By reviewing documentation, assembling a trained inspection team, and utilizing technology for real-time tracking, companies can ensure that inspections are thorough and effective. Best practices such as continuous training and encouraging feedback further optimize the inspection process, leading to better outcomes and improved customer experiences.
Avoiding common pitfalls, such as inadequate preparation and poor communication, is essential for achieving the desired results from quality control inspections. By adhering to established standards and maintaining detailed documentation, organizations can learn from past mistakes and continuously improve their processes. Ultimately, prioritizing quality control is not just about compliance; it is a strategic approach that drives operational efficiency and builds lasting trust with consumers. Embracing these practices paves the way for sustainable business success in an ever-evolving marketplace.