Defining Supplier Corrective Action Request: Key Concepts Explained
Understanding Supplier Corrective Action Requests (SCAR) to improve supplier quality and accountability.
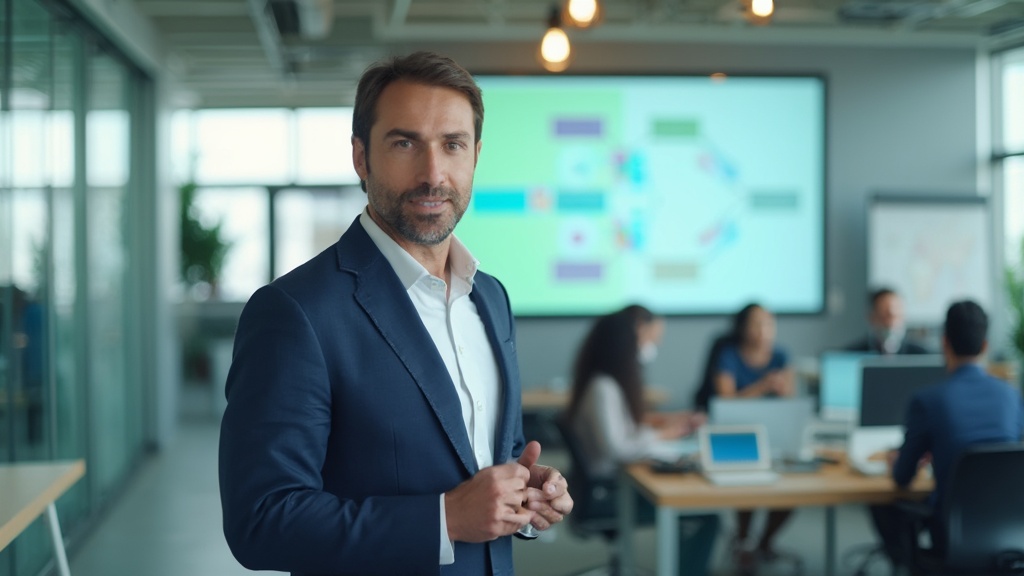
Introduction
In the complex world of supply chain management, maintaining high standards of quality is paramount. The Supplier Corrective Action Request (SCAR) process serves as a critical mechanism for addressing and resolving quality issues arising from suppliers' products or services. This formalized procedure not only identifies non-conformities but also ensures corrective and preventive measures are implemented to avoid future occurrences.
By fostering accountability and continuous improvement, SCAR enhances decision-making and control over supply chain operations, ultimately leading to more consistent and high-quality product outputs. This article delves into the intricacies of the SCAR process, its workflow, and the key components that make it an indispensable tool for quality management.
Definition and Purpose of SCAR
A Supplier Corrective Action Request is a formalized procedure used by companies to address and resolve quality issues stemming from suppliers' products or services. This procedure is essential for recognizing non-conformities, applying corrective actions to address these problems, and ensuring preventive measures are established to prevent recurrence. This mechanism not only communicates concerns but also enforces accountability and promotes continuous improvement in supplier performance. By centralizing data and standardizing procedures, companies can improve decision-making and gain better control over supply chain operations, ultimately fostering a more consistent and high-quality product output.
The SCAR Process and Workflow
The Supplier Corrective Action Request process is a structured approach designed to address and resolve quality issues effectively. It starts with recognizing an issue, which then leads to the issuance of a corrective action request to the supplier. Upon receiving the SCAR, the supplier carries out a thorough investigation to pinpoint the root cause of the issue. Following this, they develop a comprehensive corrective action plan aimed at rectifying the problem.
This plan is not merely formulated but also meticulously implemented and monitored to ensure its effectiveness. Throughout this procedure, detailed documentation is maintained to track progress and outcomes. The SCAR is only closed when the issue has been resolved to a satisfactory level, ensuring accountability at each step.
This methodical workflow is vital for maintaining high standards of quality management. As highlighted in the case of Siemens Digital Industries, a leader in industrial automation, maintaining robust quality control processes is essential for operational success across various sectors, from manufacturing to healthcare. Such structured approaches not only enhance operational efficiencies but also improve customer satisfaction and minimize errors, as demonstrated in various sectors including healthcare supply chains.
Key Components of a SCAR
A Supplier Corrective Action Request (SCAR) involves several key elements that are crucial for maintaining quality standards and ensuring compliance. It begins with a clear description of the non-conformity and identification of the affected products. This step is essential for understanding the scope of the issue and its potential impact.
Next, the schedule for corrective measures is established, outlining the steps and deadlines for addressing the problem. Suppliers are required to provide a thorough root cause analysis, which delves into the underlying reasons for the non-conformity. This analysis is vital for developing effective corrective measures that prevent recurrence.
A crucial element of the procedure is the development of a comprehensive remedial strategy. This plan should detail the steps to be taken, assign responsibilities, and set measurable objectives. Documentation plays a pivotal role throughout the SCAR process. It encompasses documentation of all communications, investigations, and the remedial measures taken. This thorough documentation ensures transparency and traceability, which are essential for compliance with industry standards and regulations.
For instance, Siemens Digital Industry has demonstrated the importance of integrating detailed corrective actions within their quality management systems. Their approach ensures that any non-conformities are swiftly addressed, maintaining the high standards expected in industrial automation and software solutions. By following a structured approach, businesses can enhance their operational efficiencies, reduce waste, and improve overall supply chain performance, ultimately benefiting both the supplier and the customer.
Root Cause Analysis in SCAR
'Root Cause Analysis (RCA) is a crucial element of the Supplier Corrective Action Request (SCAR) framework, aimed at systematically identifying the fundamental reasons for a non-conformity, rather than just addressing its symptoms.'. Utilizing techniques such as the 5 Whys and Fishbone Diagram, RCA delves deep into the underlying issues. For instance, Siemens Digital Industries has leveraged advanced data analysis to bridge physical and digital gaps, improving transparency and operational efficiency. By effectively identifying root causes, suppliers can implement corrective measures that not only resolve immediate issues but also prevent future occurrences, enhancing quality management across the board. Moreover, as highlighted by recent studies, a robust RCA process contributes to cost management and operational efficiency, ensuring that supply chains remain resilient and competitive.
Corrective and Preventive Actions in SCAR
Corrective steps are strategic measures taken to resolve specific non-conformities identified in Supplier Corrective Action Requests (Scars). These steps are vital to tackling immediate problems and making sure they do not happen again. Conversely, preventive measures aim to identify and eliminate potential causes of future non-conformities, creating a proactive approach to quality management. Both corrective and preventive measures are essential to the system, promoting a culture of ongoing enhancement and risk reduction within the distribution network. By embedding these practices, organizations can enhance operational efficiencies, increase customer satisfaction, and minimize risks, leading to a more resilient and reliable supply chain.
Documentation and Record-Keeping for SCARs
Comprehensive documentation and record maintenance are essential elements in the Supplier Corrective Action Request process. Thorough documentation of the issuance, supplier responses, investigation results, and corrective and preventive action plans must be carefully preserved. This rigorous documentation ensures transparency and provides a solid reference for future audits. Additionally, it plays a crucial role in demonstrating compliance with quality management standards, which is essential for regulatory adherence in industries like medical devices and pharmaceuticals. By ensuring proper documentation, organizations not only meet audit requirements but also foster a culture of accountability and continuous improvement, ultimately enhancing overall logistics chain resilience and reliability.
Benefits and Importance of SCAR in Supply Chain Management
Applying Supplier Corrective Action Requests can greatly enhance supply chain management for the better. By enhancing supplier accountability and driving quality improvements, these procedures not only reduce the risk of product failures but also minimize costs related to rework and returns. This proactive approach is essential for improving customer satisfaction. A case in point is the OneAstec initiative, where centralizing data from 17 subsidiary companies into one platform enabled more consistent and controlled reporting, ultimately leading to better decision-making and a deeper understanding of business impacts.
Furthermore, the advantages of SCAR methods reach beyond immediate cost reductions. By fostering stronger vendor relationships, companies can achieve higher service quality and operational performance, as evidenced by the increased focus on chain management in both public and private health sectors. For instance, a study highlighted that integrating logistics chain processes in hospitals has led to enhanced efficiencies, customer satisfaction, and quality of care while minimizing waste and medical errors.
News reports also highlight the significance of transparency and collaboration in distribution networks. Resilinc's announcement of the Top 30 most resilient providers in the high-tech sector for 2023 emphasizes how a high degree of transparency and ongoing collaboration can lead to chain intelligence and resilience. Likewise, the Gartner Supply Chain Top 25 ranking highlights how business performance and community opinion are crucial indicators of excellence in the chain.
Consequently, implementing specific methodologies not only tackles quality concerns but also fosters a more robust and effective supply chain, ultimately benefiting both the organization and its clients.
Best Practices for Implementing SCAR
To effectively implement Supplier Corrective Action Requests (SCAR), establishing clear communication channels with suppliers is crucial. This ensures that all parties are on the same page, facilitating a smoother resolution process. Establishing achievable deadlines for corrective measures is equally important, as it allows suppliers to address issues without unnecessary pressure, ultimately leading to more thorough and effective solutions.
Providing support during the investigation phase helps suppliers understand the root causes of problems and develop appropriate corrective actions. Consistent instruction on quality management concepts and related methodologies can enable both internal groups and suppliers, making certain they are adequately prepared to address challenges effectively.
Regularly assessing and improving these procedures based on previous experiences can greatly increase their effectiveness. For example, more than half of the instances in logistics management provide simulations of practice, offering a detailed account of evaluators' thinking and decision-making methods in response to contextual elements. This method can be utilized for such processes, enabling firms to gain insights from past instances and enhance their practices accordingly.
Moreover, leveraging data-driven insights can provide a strategic edge. Understanding the broader context, such as industry dynamics and global trade patterns, can help in making informed decisions and negotiating more effectively with suppliers. By adopting a comprehensive and iterative approach to SCAR, organizations can drive continuous improvement and maintain high-quality standards across their supply chains.
Conclusion
The Supplier Corrective Action Request (SCAR) process is an essential tool in supply chain management, aimed at addressing and resolving quality issues that arise from suppliers' products or services. By systematically identifying non-conformities and enforcing corrective and preventive measures, SCAR not only enhances supplier accountability but also fosters continuous improvement. This structured approach ensures that quality standards are maintained, ultimately leading to more consistent and reliable product outputs.
The workflow of the SCAR process is methodical, beginning with the identification of issues and culminating in the implementation of corrective actions. Key components such as root cause analysis, thorough documentation, and the establishment of clear timelines are instrumental in ensuring that quality management is both effective and compliant with industry standards. By integrating these elements, organizations can enhance operational efficiencies, reduce waste, and improve overall supply chain performance.
Moreover, the benefits of SCAR extend beyond immediate corrective actions. By fostering stronger supplier relationships and driving quality improvements, businesses can achieve higher service quality and operational performance. This proactive approach not only minimizes costs associated with rework and returns but also enhances customer satisfaction and builds a more resilient supply chain.
In conclusion, the SCAR process is not just a reactive measure but a strategic framework that empowers organizations to maintain high-quality standards, streamline operations, and promote a culture of accountability and continuous improvement within the supply chain. Implementing best practices in SCAR can lead to significant transformations in operational performance, ultimately benefiting both suppliers and customers alike.
Discover how Movley's expert inspections can help you implement an effective SCAR process today!